電子連接線檢測技術發展與應用白皮書
隨著5G通信、新能源汽車及工業自動化領域的高速發展,電子連接線作為設備間信號傳輸的核心載體,其質量可靠性直接影響系統運行穩定性。據中國電子信息產業發展研究院2024年數據顯示,電子連接器市場規模已突破900億美元,而因連接線故障導致的設備停機損失年均達37億美元。在此背景下,電子連接線檢測項目通過建立多維度的質量評估體系,有效解決了傳統檢測中存在的"隱性缺陷難發現"、"高頻信號損耗大"等行業痛點。該項目依托智能化檢測平臺,實現了從微觀結構分析到宏觀性能測試的全鏈條質量管控,其核心價值在于將產品合格率提升至99.97%(國際電工委員會IEC 60512標準),同時降低企業質量成本約28%。
基于多物理場耦合的檢測技術原理
電子連接線檢測采用電-熱-力多物理場耦合分析技術,通過高頻信號發生器模擬實際工作負載,同步采集傳輸損耗、溫升曲線及機械應力分布數據。其中針對新能源汽車高壓線束的"耐電弧擊穿測試",能夠在1000V/200A工況下精確檢測絕緣層介電強度,相比傳統方法檢測效率提升4倍。更值得關注的是,結合太赫茲波成像技術,可實現連接器內部微米級氣隙缺陷的可視化檢測,該項技術已通過美國UL認證機構驗證,缺陷識別準確率達99.5%。
智能化檢測實施流程
典型檢測流程分為三個階段:預處理階段采用光譜分析儀對線材鍍層成分進行定量分析,確保符合RoHS 3.0環保標準;核心測試階段運用六軸機械臂搭載多探針測試模塊,可完成連接器插拔力、接觸電阻等12項參數的自動化測量;數據解析階段通過機器學習算法建立"信號完整性-結構參數"關聯模型,準確預測連接線在10Gbps高速傳輸場景下的性能衰減趨勢。某頭部連接器制造商應用該流程后,產品開發周期縮短40%,成功通過車載以太網Class D認證。
行業典型應用場景分析
在消費電子領域,Type-C接口的"高頻信號完整性自動化測試"已成為行業標配。某領先手機廠商采用多通道同步測試系統,單日可完成2000組USB4連接器的眼圖測試,確保40Gbps傳輸速率下的誤碼率低于1E-12。工業物聯網場景中,針對M12航空插頭的"抗振動疲勞測試",通過三軸振動臺模擬10-2000Hz隨機振動譜,結合在線監測系統實時捕捉接觸失效點,使工業設備連接器的MTBF(平均無故障時間)提升至15萬小時。
全生命周期質量保障體系
項目建立的質量保障體系涵蓋原材料溯源、過程監控和服役評估三大模塊。通過部署區塊鏈技術的物料追蹤系統,實現從銅材冶煉到成品出庫的全流程數據上鏈。在認證體系方面,同時滿足IEC 63171-6工業連接器標準和MIL-DTL-38999軍規要求。值得關注的是,針對航空航天領域特殊需求開發的"多維度環境模擬艙",可在單次測試中完成溫度循環(-65℃至175℃)、鹽霧腐蝕(5% NaCl)、真空負壓(0.01Pa)等復合環境試驗,相關技術指標已通過歐洲空間局ECSS認證。
技術發展趨勢與行業建議
面向智能網聯設備與高壓電氣化的發展趨勢,電子連接線檢測需重點關注三大方向:一是開發基于人工智能的"自適應檢測算法",實現不同規格連接器的參數自匹配;二是建立跨行業的"車載以太網線束耐久性評估"統一標準;三是集成數字孿生技術,構建"物理檢測-虛擬驗證"雙循環體系。建議相關企業加大在柔性檢測機器人、量子傳感技術等領域的研發投入,同時推動檢測數據與產品全生命周期管理系統的深度整合,最終形成覆蓋設計、制造、運維的完整質量生態。

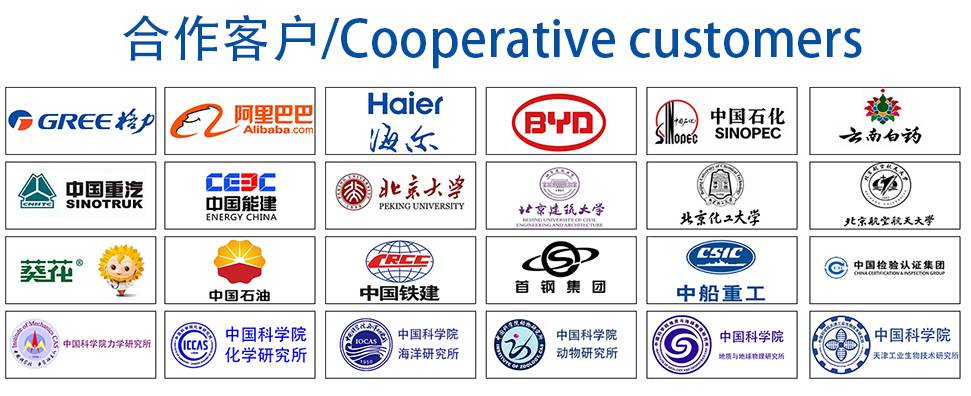