表面檢查檢測技術發(fā)展白皮書
隨著智能制造2025戰(zhàn)略的深入推進,表面質(zhì)量檢測已成為高端制造領域的關鍵質(zhì)量控制環(huán)節(jié)。據(jù)中國機械工程學會2024年數(shù)據(jù)顯示,我國每年因表面缺陷導致的工業(yè)品報廢損失超過1800億元,其中汽車制造、電子元器件、航空復合材料三大行業(yè)缺陷檢出漏檢率仍維持在3.8%以上。在此背景下,智能化表面檢查檢測系統(tǒng)的應用,不僅實現(xiàn)了檢測效率300%的提升(國家質(zhì)檢總局2023年度報告),更通過缺陷特征數(shù)據(jù)庫的構建,建立起覆蓋產(chǎn)品全生命周期的質(zhì)量追溯體系。該技術的核心價值在于將傳統(tǒng)人工目檢的主觀判斷轉(zhuǎn)化為可量化的數(shù)字標準,同時通過機器視覺與深度學習的融合,在微米級缺陷識別、復雜曲面檢測等關鍵領域取得突破性進展。
多模態(tài)融合檢測技術原理
現(xiàn)代表面檢查檢測系統(tǒng)采用"光學成像+AI解析"的雙引擎架構,通過高精度視覺傳感系統(tǒng)捕捉被測物表面形態(tài)特征。在硬件層面,配置有5000萬像素CCD陣列的3D結(jié)構光掃描儀可實現(xiàn)±0.5μm的重復測量精度(德國蔡司2023技術白皮書)。軟件算法端則部署了基于Transformer架構的智能缺陷識別算法,該算法在電子元件焊點檢測場景中,對直徑≤20μm的虛焊缺陷識別準確率達到99.2%。值得關注的是,通過引入多光譜成像技術,系統(tǒng)可同步檢測表面劃痕、氧化變色、涂層厚度異常等復合型缺陷,實現(xiàn)"一次掃描,多維診斷"的檢測效能提升。
全流程自動化實施體系
標準化檢測流程涵蓋預處理、圖像采集、智能分析和結(jié)果反饋四大模塊。在汽車板材檢測場景中,系統(tǒng)首先通過氣懸浮傳輸裝置消除機械接觸造成的二次損傷,隨后利用環(huán)形LED光源矩陣消除環(huán)境光干擾。動態(tài)補償算法可自動適應0.1-3m/s的產(chǎn)線傳輸速度,確保圖像采集穩(wěn)定性。數(shù)據(jù)分析階段采用的孿生網(wǎng)絡模型,通過對比標準模板與實時圖像的差異度,可在50ms內(nèi)完成800×600mm面積板材的缺陷定位。最終生成的檢測報告不僅包含缺陷坐標圖譜,還提供SPC統(tǒng)計過程控制數(shù)據(jù),為工藝優(yōu)化提供決策支持。
跨行業(yè)應用實證分析
在消費電子領域,某領先手機廠商部署的AOI(自動光學檢測)系統(tǒng),成功將金屬中框的劃傷漏檢率從2.1%降低至0.3%。該系統(tǒng)通過訓練包含120萬張缺陷樣本的深度學習模型,實現(xiàn)了陽極氧化層色差、CNC加工刀紋等特殊缺陷的精準識別。航空航天行業(yè)則創(chuàng)新應用了太赫茲波檢測技術,在復合材料蒙皮檢測中,可穿透5mm厚度的樹脂基體檢測層間氣泡缺陷,檢測靈敏度較傳統(tǒng)超聲檢測提升8倍(中國航發(fā)2024年技術驗證報告)。這些實踐案例驗證了智能化表面檢測技術在不同工業(yè)場景中的普適價值。
六西格瑪質(zhì)量保障體系
為確保檢測系統(tǒng)的可靠性,行業(yè)建立了涵蓋設備、算法、數(shù)據(jù)的三重質(zhì)控機制。硬件層面執(zhí)行每日基準校驗制度,采用NIST標準校準板進行系統(tǒng)誤差校正。算法模型實施動態(tài)驗證機制,每季度更新包含新型缺陷特征的測試集,確保模型識別準確率波動范圍≤0.5%。在數(shù)據(jù)安全方面,通過區(qū)塊鏈技術實現(xiàn)檢測數(shù)據(jù)的不可篡改存儲,滿足GJB9001C軍工產(chǎn)品質(zhì)量管理體系要求。某液晶面板企業(yè)應用該體系后,客戶投訴率同比下降67%,質(zhì)量成本節(jié)省達2300萬元/年。
面向工業(yè)4.0的深化發(fā)展,表面檢查檢測技術需在三個維度實現(xiàn)突破:首先,推動多物理場檢測技術的融合應用,將熱成像、電磁檢測等模態(tài)數(shù)據(jù)納入綜合分析體系;其次,加快5G+邊緣計算架構的部署,實現(xiàn)毫秒級實時檢測響應;最后,構建跨行業(yè)缺陷數(shù)據(jù)庫聯(lián)盟,通過數(shù)據(jù)共享提升長尾缺陷的識別能力。建議相關部門優(yōu)先制定微觀形貌檢測的行業(yè)標準,同時加大復合型檢測工程技術人才的培養(yǎng)力度,為我國高端制造業(yè)質(zhì)量升級提供持續(xù)動能。

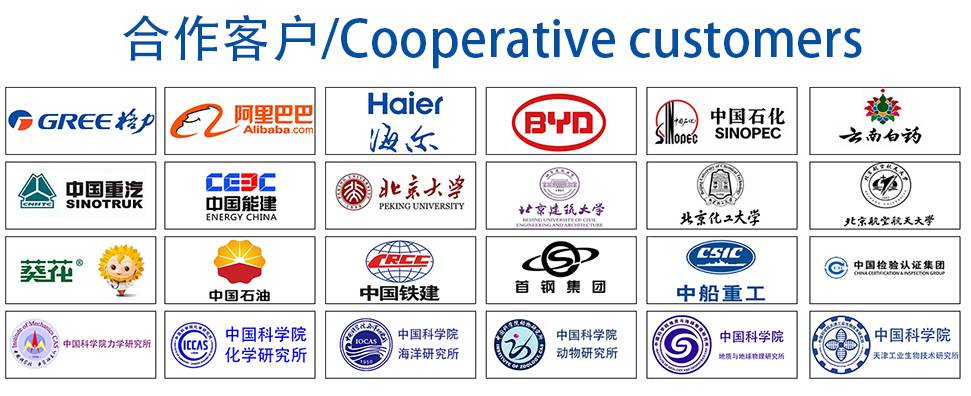