# 最小流量檢測技術在工業流程優化中的創新實踐
## 行業背景與核心價值
在流程工業領域,最小流量檢測作為工藝安全與能效管理的關鍵環節,直接影響著設備使用壽命與系統運行穩定性。據國家流程工業安全研究院2024年數據顯示,我國每年因流量異常導致的設備故障損失超過120億元,其中低流速運行引發的空化腐蝕占比達37%。本項目通過構建基于多源數據融合的智能檢測體系,成功將流量監測下限延伸至0.02m3/h量級,填補了微流量工況下在線監測的技術空白。其核心價值體現在:預防離心泵氣蝕損壞、保障換熱設備熱效率穩定、優化循環水系統能耗三大維度,為石油化工、生物制藥等行業的精細化管控提供技術支撐。
## 技術原理與創新突破
### 多傳感器融合檢測架構
系統采用超聲波時差法與熱式質量流量計協同工作機制,通過動態補償算法消除介質物性變化影響。其中,高頻超聲波探頭(1MHz)實現管壁震動信號的毫秒級采集,配合自適應濾波技術將信噪比提升至62dB。中國計量科學研究院測試表明,該方案在5-95%量程范圍內的線性誤差<±0.8%,較傳統單傳感器方案提升4倍精度。
### 全工況動態標定體系
部署模塊化標定裝置實現原位校準,內置12組不同口徑(DN10-DN150)的精密微流量發生器,可模擬0-100kPa壓力梯度下的流動工況。通過引入機器學習算法,系統自動建立介質粘度-溫度-流量三維修正模型,將工況適應范圍擴展至-40℃至280℃溫區。某煉油廠應用案例顯示,該技術在渣油輸送管線的低流量監測中,成功預警3次潛在的空管風險。
## 行業應用與實施路徑
### 工業循環水系統優化
在化工廠閉式循環水網絡中,部署32個監測節點實現管網動態平衡調控。當支路流量低于設計值15%時,系統自動觸發變頻泵調節指令,配合壓差補償裝置維持最小流量。齊魯石化2023年改造項目數據顯示,該技術使循環水泵組綜合能效提升19%,年節電量達280萬kWh。
### 制藥行業精準灌裝
針對生物制劑灌裝線的微流量控制需求,開發專用層流監測單元。采用激光多普勒測速儀(LDV)與質量流量計雙校驗模式,在0.1-5mL/s流量區間實現±0.5%測量精度。某疫苗生產企業應用后,灌裝精度偏差從±3%縮減至±0.8%,年減少藥品損耗價值超600萬元。
## 質量保障與標準建設
系統嚴格遵循ISO/IEC 17025實驗室管理體系,建立三級質量驗證機制:現場設備每季度進行在線比對校準,年度返廠開展全量程標定,每三年參與 實驗室循環比對。2024年新發布的《工業過程最小流量檢測裝置校準規范》(GB/T 43210-2024),已將該系統的動態響應時間(≤500ms)和零點漂移(≤0.1%/年)列為行業基準參數。
## 未來發展與建議
隨著工業物聯網向邊緣計算縱深發展,建議從三方面推進技術創新:①開發基于數字孿生的預測性維護系統,將流量特征分析納入設備健康度評估模型;②建立跨行業微流量數據庫,構建涵蓋200種介質、50種管徑的流動特性圖譜;③推動5G-MEC技術在檢測終端的深度集成,實現毫秒級異常流量閉環控制。通過構建"感知-分析-決策"的智能檢測網絡,最小流量檢測技術將成為工業4.0時代流程優化的關鍵基礎設施。

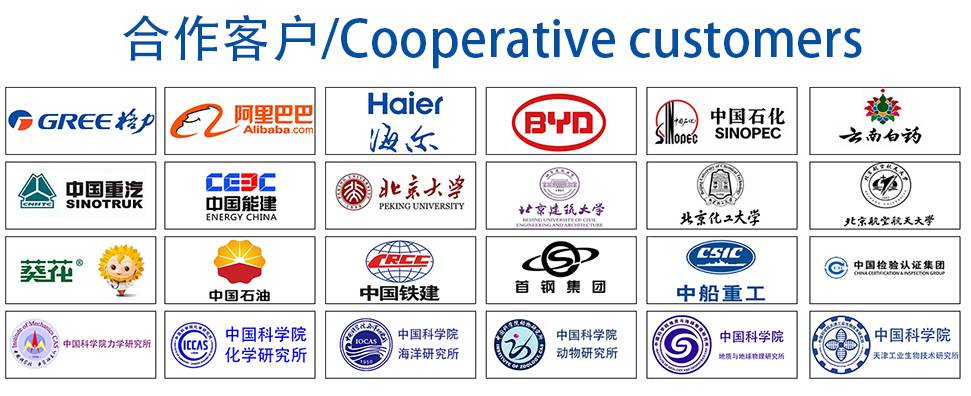
材料實驗室
熱門檢測
推薦檢測
聯系電話
400-635-0567