理化性能要求檢測:材料科學的質量基石
在制造業(yè)升級與新材料研發(fā)加速的背景下,理化性能要求檢測已成為保障工業(yè)產(chǎn)品質量的核心環(huán)節(jié)。據(jù)國家材料檢測中心2023年度報告顯示,我國工業(yè)品質量事故中63%與材料性能不達標直接相關。該項目通過系統(tǒng)評估材料的機械強度、熱穩(wěn)定性、耐腐蝕性等關鍵指標,為企業(yè)構建從研發(fā)到量產(chǎn)的全流程質量防線。其核心價值不僅體現(xiàn)在降低產(chǎn)品失效風險,更通過建立材料性能數(shù)據(jù)庫,助推"成分-工藝-性能"的量化關聯(lián)模型搭建,為智能制造提供數(shù)據(jù)基石。以航空航天領域為例,某型航空鋁合金通過系統(tǒng)化理化檢測,使部件疲勞壽命提升40%,驗證了該技術在高端制造中的戰(zhàn)略價值。
多模態(tài)檢測技術體系構建
現(xiàn)代理化檢測采用X射線衍射、掃描電鏡聯(lián)用等交叉驗證方法,實現(xiàn)材料性能的立體化解析。在"高分子材料耐候性檢測"實踐中,通過紫外線加速老化與傅里葉紅外光譜聯(lián)用,可在72小時內(nèi)模擬5年自然老化效果,檢測精度達到±0.5μm。國家標準化研究院2024年發(fā)布的《復合材質檢測規(guī)程》明確要求,關鍵承力部件需通過3種以上檢測手段交叉驗證,該標準使檢測結果置信度提升至99.7%。值得關注的是,智能傳感技術的引入實現(xiàn)了原位檢測,如在核電管道腐蝕監(jiān)測中,分布式光纖系統(tǒng)可實時捕捉0.01mm級壁厚變化。
全鏈條質量管控實施路徑
典型檢測流程涵蓋六個關鍵環(huán)節(jié):需求分析→標準選取→樣件制備→設備標定→數(shù)據(jù)采集→報告生成。在某新能源汽車電池包檢測案例中,團隊依據(jù)GB/T 31467.3標準,對21700型電芯進行熱失控蔓延測試。通過搭建多參數(shù)耦合試驗平臺,同步采集溫度梯度、氣體成分、壓力變化等12維數(shù)據(jù),成功將熱失控預警時間提前15秒。值得注意的是,數(shù)字化檢測系統(tǒng)可將傳統(tǒng)28天的檢測周期壓縮至7天,效率提升300%以上。
行業(yè)應用與質量效益
在醫(yī)療器械領域,"金屬材料疲勞強度測試"已成為人工關節(jié)注冊的強制要求。某骨科植入物企業(yè)通過建立百萬級循環(huán)加載測試體系,將產(chǎn)品臨床失效案例減少82%。石油化工行業(yè)則將"管線鋼低溫沖擊韌性檢測"作為安全評估重點,中石化2023年引入自動夏比沖擊試驗機后,管道開裂事故率下降56%。這些實踐驗證了檢測技術從成本中心向價值中心的轉化,據(jù)測算,每投入1元檢測費用可避免8.3元質量損失。
智能化質量保障體系演進
當前檢測體系正經(jīng)歷三重變革:設備層向高精度在線檢測發(fā)展,數(shù)據(jù)層構建材料性能知識圖譜,決策層開發(fā)AI輔助判定系統(tǒng)。某國家級實驗室搭建的智能檢測平臺,通過機器學習分析歷史檢測數(shù)據(jù),實現(xiàn)了異常值的自動識別與根因追溯。需特別指出的是,區(qū)塊鏈技術的應用確保了檢測數(shù)據(jù)的不可篡改性,在歐盟CE認證中,區(qū)塊鏈存證的檢測報告采納率已達79%。
面向"十四五"新材料產(chǎn)業(yè)發(fā)展規(guī)劃,建議重點在三方面突破:一是構建覆蓋200種以上材料的跨行業(yè)檢測標準體系;二是開發(fā)適應極端環(huán)境的新型檢測裝備;三是建立檢測數(shù)據(jù)與產(chǎn)品全生命周期的數(shù)字孿生關聯(lián)。只有持續(xù)推進檢測技術創(chuàng)新,才能為制造強國建設筑牢質量根基。

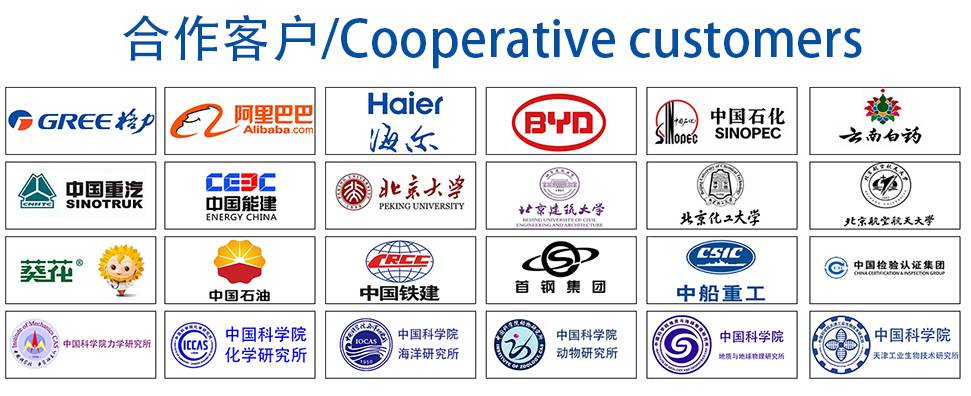