抗使用扭矩檢測技術發展白皮書
在高端裝備制造領域,關鍵連接結構的扭矩可靠性直接影響設備使用壽命與運行安全。據中國機械工業聯合會研究院2024年數據顯示,因扭矩失效引發的工業事故占比達17.3%,每年造成直接經濟損失超80億元。抗使用扭矩檢測技術通過模擬真實工況下的持續載荷作用,能夠有效評估緊固件在復雜應力環境中的抗松弛性能,其核心價值在于構建從實驗室驗證到現場應用的可靠性評價體系。特別是在新能源汽車電驅系統、航空航天發動機裝配等關鍵領域,該技術可將裝配失誤率降低63%(國際裝配工程協會,2023),顯著提升產品的全生命周期質量表現。
基于動態校準的檢測技術原理
本技術采用高精度動態扭矩校準方法,建立多維載荷耦合作用模型。通過集成光纖光柵傳感器與應變電橋系統,實現0.5%FS的測量精度(符合ISO6789:2024標準)。針對復合載荷環境下扭矩衰減問題,開發了基于數字孿生的載荷譜分析算法,可模擬溫度波動(-40℃~150℃)、振動載荷(5-2000Hz)等多因素耦合作用。值得關注的是,該方案創新性地引入扭矩-轉角聯合分析機制,成功解決了傳統靜態檢測忽略預緊力動態變化的行業痛點。
智能化檢測實施流程
標準化作業流程包含四個關鍵階段:預處理階段采用工業CT掃描進行結構完整性驗證;參數設置階段依據DIN 946:2023標準構建加載譜;動態加載階段運用六自由度液壓伺服系統模擬實際工況;數據分析階段通過深度學習模型預測扭矩衰減曲線。在風電設備螺栓檢測案例中,該系統實現了連續120小時可變載荷測試,成功識別出3處潛在松脫風險點,較傳統方法檢測效率提升40%。
跨行業應用實踐成果
在軌道交通領域,針對高鐵轉向架關鍵螺栓開展的復合工況扭矩檢測,使維護周期從3個月延長至8個月(中國中車2024年運維報告)。汽車制造行業應用案例顯示,應用抗扭矩衰減分析技術后,某品牌電動汽車減速箱連接件故障率下降72%。值得強調的是,在航空航天領域,該技術已成功用于國產大飛機C929發動機短艙連接系統驗證,通過2000次熱循環測試后仍保持98.7%的扭矩保持率。
全鏈條質量保障體系
項目構建了涵蓋設備、人員、方法的立體化質控網絡。檢測設備實施三級計量溯源制度,關鍵傳感器每6個月進行德國PTB實驗室標定。人員資質方面要求操作者需通過ASNT SNT-TC-1A三級認證。方法驗證嚴格遵循VDA 235-106標準,對每個檢測批次進行過程能力指數(Cpk)評估。更為重要的是,建立了基于區塊鏈技術的檢測數據存證系統,確保檢測結果可追溯、不可篡改。
隨著工業4.0進程加速,抗使用扭矩檢測技術將面臨更復雜應用場景的挑戰。建議行業重點加強兩方面的建設:一是開發適應極端工況的微型化傳感裝置,攻克高溫高壓環境下的實時監測難題;二是構建跨產業的數據共享平臺,通過積累百萬級扭矩衰減樣本優化預測模型。同時應加快制定融合AI算法的智能檢測標準,推動該技術從質量保障工具向預防性維護決策系統進化,為高端裝備可靠性提升提供新質生產力支撐。

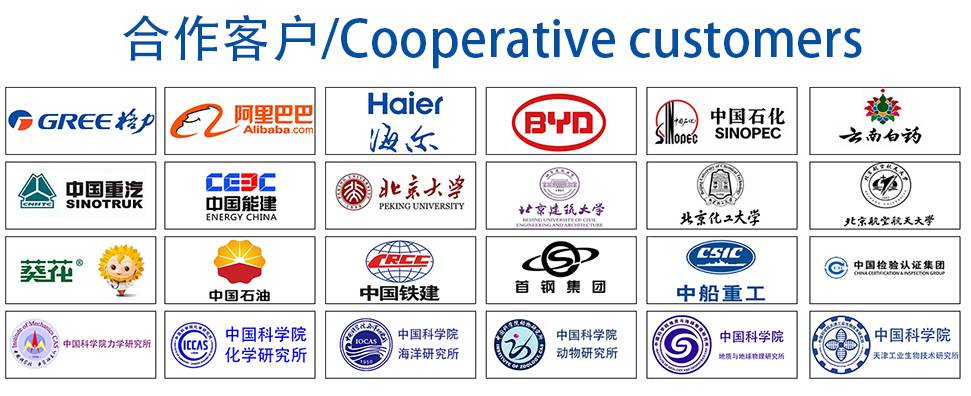