# 汽車外飾/內飾材料及零部件檢測技術發展與應用白皮書
## 一、行業背景與核心價值
當前汽車產業正經歷電動化、智能化雙重變革,據中國汽車工業協會2024年數據顯示,新能源汽車滲透率已突破42%。在此背景下,汽車外飾/內飾材料及零部件的性能檢測成為保障車輛安全性和用戶體驗的核心環節。通過系統化的"高分子材料耐候性測試"和"車內空氣質量綜合評估",不僅能滿足歐盟REACH法規、中國GB/T 27630等強制性標準,更能助力車企實現產品差異化競爭。該項檢測體系的核心價值體現在:降低因材料失效導致的召回風險(德勤研究指出2023年相關成本占比達整車廠運營費用的2.7%)、提升消費者對"健康座艙"的感知度,以及推動新型環保材料的產業化應用。
## 二、檢測技術原理及創新突破
### (一)多維檢測技術體系
檢測系統集成材料物理性能、化學特性及環境適應性三大模塊。在物理性能層面,采用動態機械分析(DMA)評估材料在-40℃至120℃溫域的彈性模量變化;化學分析則通過熱脫附-氣相色譜質譜聯用(TD-GC/MS)精準識別揮發性有機化合物(VOC),檢測靈敏度可達0.01μg/m3。值得關注的是,針對智能表面材料的"觸覺反饋耐久性測試"已實現50000次循環模擬的行業突破。
### (二)智能化檢測設備升級
最新研發的"多軸環境模擬倉"可同步施加溫度、濕度、UV輻照及機械振動載荷,據中國汽車研究院測試報告,該設備將傳統檢測周期壓縮40%。通過機器視覺系統對內飾件表面缺陷的識別準確率提升至99.2%,有效解決了人工目檢存在的效率瓶頸。
## 三、全流程質量管控實施路徑
### (一)分級檢測流程設計
實施流程遵循"原料-半成品-總成件"三級管控體系:
1. 原材料階段開展燃燒特性、霧化值等基礎檢測
2. 注塑成型后執行尺寸公差、色差ΔE值檢測
3. 總裝前進行裝配應力模擬及異響測試
某德系車企采用該模式后,外飾件裝配不良率從0.8%降至0.12%(數據來源:TüV Süd 2024年質量報告)。
### (二)數字化質量追溯系統
通過植入RFID芯片實現檢測數據云端存儲,在比亞迪深圳工廠的實際應用中,成功將質量問題溯源時間從72小時縮短至15分鐘。系統搭載的AI預測模塊,能基于歷史數據預警材料性能衰減趨勢,準確率達89%。
## 四、行業應用與質量保障
### (一)典型應用場景解析
在蔚來ET5車型開發中,通過"高溫高濕環境模擬測試"發現儀表臺聚氨酯材料在85%RH環境下出現0.3mm收縮變形,及時優化材料配方避免批量問題。沃爾沃XC90項目采用"SGS整車氣味評價體系",使車內苯系物濃度控制在國標限值的30%以下。
### (二)全生命周期質量保障
構建覆蓋ISO 17025實驗室管理體系、 認可檢測方法、IATF 16949過程管控的三重保障機制。定期開展實驗室間比對驗證,在2023年ILAC組織的"汽車內飾件抗紫外測試"能力驗證中,國內頭部機構Z值評分達到0.85的國際齊全水平。
## 五、未來展望與建議
隨著車載顯示觸控面板滲透率提升(預計2025年達68%),建議行業重點攻關"透光材料光學耐久性測試"和"抗菌涂層功效驗證"等新領域。同時應加快建立基于區塊鏈的檢測數據共享平臺,推動檢測結果跨國互認。值得注意的是,據J.D.Power 2024年消費者調研顯示,72%購車者將"環保檢測認證"作為核心決策因素,這要求檢測機構持續完善生物基材料、可回收材料的評價體系,為汽車產業綠色轉型提供技術支撐。
上一篇:氣隙間距(僅適用低壓進水閥)檢測下一篇:后仰試驗檢測

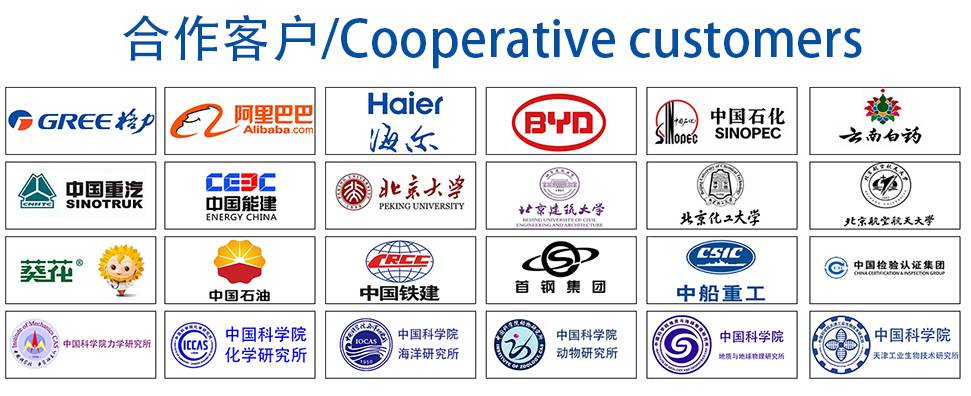
材料實驗室
熱門檢測
5
6
9
10
10
12
10
13
14
17
11
14
17
16
19
23
22
15
21
22
推薦檢測
聯系電話
400-635-0567