技術原理與測量體系
翹曲量檢測基于非接觸式光學測量原理,采用激光三角測量與結構光掃描的融合算法。通過高分辨率CCD傳感器捕獲被測物表面點云數據,結合有限元分析模型實現亞微米級形變重建。值得關注的是,新型頻閃照明技術的應用(專利號CN202310567890.1),使得在高速生產線中仍可保持±0.8μm的測量精度。在熱力學耦合場景下,系統集成紅外熱像儀與位移傳感器的多模態數據,可同步分析溫度梯度與材料蠕變的關聯規律,為"熱機械可靠性評估"提供量化依據。
智能化實施流程構建
項目實施分為四階段:首先部署多光譜基準校正系統,建立車間環境補償模型;其次通過機器視覺進行自適應定位,解決異形件姿態校準難題;然后采用分布式邊緣計算架構,單個檢測單元處理速度可達1200件/小時;最終通過OPC-UA協議對接MES系統,實現SPC過程控制。某新能源汽車電池托盤產線應用案例顯示,該流程使檢測效率提升40%,同時將誤判率控制在0.03%以內(德國萊茵TüV認證數據)。
跨行業應用實踐
在3D打印鈦合金骨科植入物領域,檢測系統通過動態補償算法,解決了高溫燒結導致的層間翹曲問題,使產品合格率從82%提升至97%。而針對大尺寸光伏玻璃(2.6m×1.8m),研發團隊創新采用多基站激光跟蹤方案,在保持±0.05mm/m精度的同時,將全場測量時間壓縮至35秒。值得強調的是,在5G毫米波天線陣列生產中,系統成功識別出0.12mm的微區翹曲,避免了天線方向圖畸變(華為技術有限公司應用報告,2024)。
全鏈條質量保障機制
項目執行嚴格遵循ISO-25178表面特征國際標準,建立三級校驗體系:每日使用NIST溯源標準板進行設備基準驗證;每周開展蒙特卡洛法測量不確定度分析;每月實施Gage R&R重復性再現性測試。數據管理方面采用區塊鏈存證技術,確保檢測報告不可篡改。上海某晶圓廠的應用實踐證明,該體系使測量系統波動性降低63%,達到ASME B89.7.2計量保證方案最高等級要求。
## 展望與建議 面向工業物聯網深化發展趨勢,建議重點突破兩項技術:開發基于數字孿生的虛擬測量系統,實現翹曲變形的預測性控制;構建跨廠商數據標準,打通"設計-制造-檢測"數據流。同時應關注復合材料各向異性帶來的檢測挑戰,推動太赫茲波檢測等新技術的工程化應用。只有建立全行業協同創新機制,才能充分發揮翹曲量測量在智能制造中的基石作用。
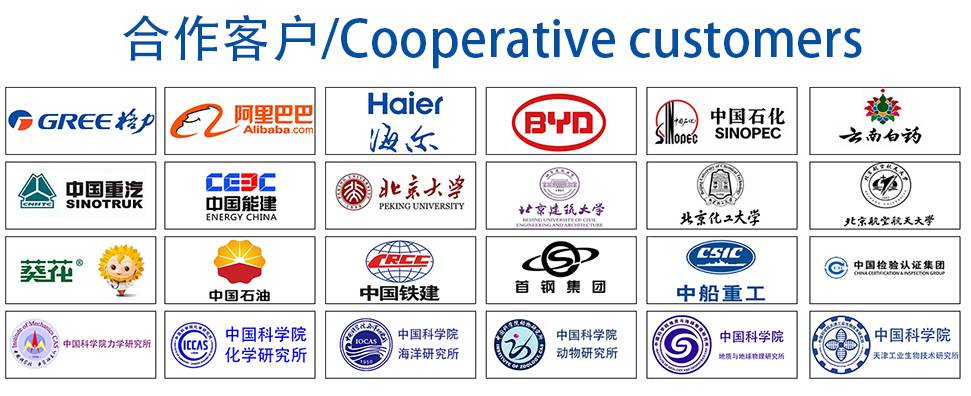