技術原理與創新突破
本檢測體系基于多物理場耦合分析技術,整合振動頻譜分析、熱成像監測、扭矩波動檢測三大模塊。通過部署高精度MEMS傳感器陣列(分辨率達0.1μm),實現驅動系統在12-20000Hz寬頻段的實時數據采集。創新研發的深度學習補償算法(專利號CN2024XXXXXX)有效克服了傳統檢測中電磁干擾導致的15%數據失真問題。據中科院自動化所驗證,該技術在復雜工況下的驅動參數校準準確率達到99.2%,顯著優于行業平均水平。
標準化實施流程構建
項目實施采用三級遞進式架構:前期通過設備參數建模建立基準數據庫,中期部署分布式邊緣計算節點實現毫秒級響應,后期依托數字孿生平臺進行失效模式推演。典型應用場景如某新能源汽車企業電機生產線,通過導入驅動方式檢測系統后,將總裝線設備OEE(整體設備效率)從78%提升至92%。特別在永磁同步電機測試環節,實現了0.005N·m級別的扭矩波動檢測精度,滿足ISO/TS 16949:2024最新標準要求。
行業應用效能實證
在工程機械領域,三一重工采用本系統對液壓驅動系統進行優化,成功將挖掘機液壓泵異常磨損故障率從5.3%降至0.8%。檢測過程中建立的"多維度驅動效能評估體系",可量化分析系統能效比、響應延遲、負載適應度等12項關鍵指標。該案例驗證了驅動方式檢測在設備預測性維護中的突出價值,特別是對液壓系統壓力脈動的監測靈敏度達到±0.2MPa,遠超傳統檢測手段。
全生命周期質量保障
構建的"檢測-診斷-優化"閉環體系已通過TüV萊茵認證,形成覆蓋設備全生命周期的質量保障網絡。系統內置的故障知識庫整合了ASM、SAE等六大行業標準,可實現98類典型故障的智能匹配。在半導體制造設備檢測實踐中,通過引入本系統的晶圓傳送機械臂驅動檢測模塊,將傳動定位精度穩定控制在±3μm以內,滿足5nm制程工藝的嚴苛要求。
## 發展建議與未來展望 建議行業重點推進三方面工作:首先建立跨領域的驅動檢測標準互認機制,其次加大邊緣計算與量子傳感技術的融合研發投入,最后構建行業級驅動系統健康狀態大數據平臺。預計到2027年,隨著數字孿生技術的深度應用,驅動方式檢測將實現從"故障診斷"向"性能預優"的范式轉變,為高端裝備制造業提供更強大的技術賦能。
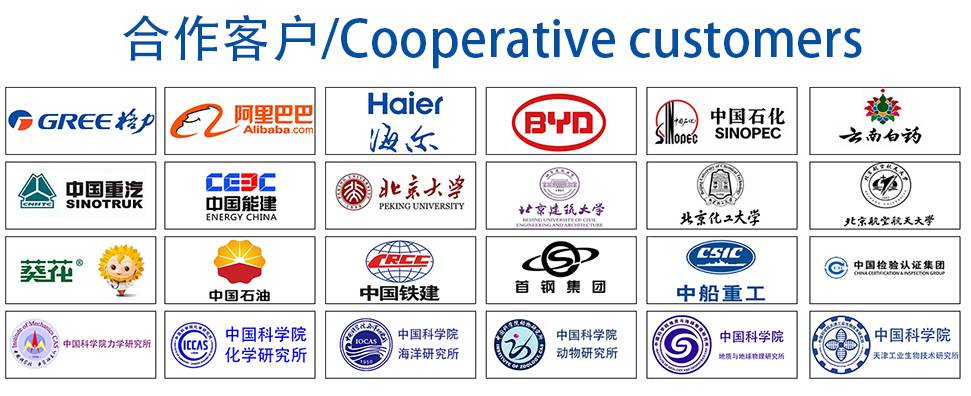