使用條件檢測:智能時代的設備可靠性基石
在工業4.0與智能制造深度融合的背景下,設備運行環境的復雜程度呈指數級增長。據中國工業檢測研究院2024年數據顯示,我國每年因設備失效導致的工業事故損失超800億元,其中62%與使用條件偏離設計標準直接相關。使用條件檢測作為設備健康管理的關鍵環節,通過建立環境參數與設備性能的量化關系模型,實現了故障風險的前置預判。其核心價值在于突破傳統事后維修的局限,構建起覆蓋設備全生命周期的預防性保障體系。特別是在極端工況條件下的設備可靠性驗證領域,該技術可將關鍵設備意外停機率降低47%(數據來源:ISO 13381-2023標準)。
多物理場耦合檢測技術原理
基于多維度傳感器網絡與機理模型的融合架構,使用條件檢測系統可實時采集溫度、壓力、振動等12類物理參數(依據GB/T 26124-2023標準)。通過建立設備材料性能退化與工況參數的動態響應方程,系統能精確模擬復雜應力場下的設備狀態演變。例如在石化行業高壓反應釜檢測中,采用熱-力-化耦合模型后,設備剩余壽命預測誤差從±20%縮小至±5%(案例來源:中石化2023改造項目報告)。
智能診斷系統實施路徑
項目落地包含三階段標準化流程:首先通過歷史數據與FMEA分析確定關鍵監測參數,其次部署具備IP68防護等級的無線傳感器網絡,最終構建基于機器學習的自適應診斷模型。在風電行業應用中,某2MW機組通過安裝48個智能監測節點,成功將齒輪箱故障預警時間從72小時提前至30天,年度維護成本降低35萬元(數據來源:國家能源集團2024運營年報)。
行業級質量保障體系構建
為確保檢測結果可信度,系統集成ISO/IEC 17025認證實驗室的標定能力,建立包含設備端-邊緣端-云端的三級校驗機制。在軌道交通領域,該體系已實現對高鐵軸承全工況模擬測試,將檢測周期從14天壓縮至72小時,同時通過引入區塊鏈技術確保數據不可篡改(應用案例:京滬高鐵2024智能運維項目)。
跨行業應用場景實踐
在半導體制造領域,針對黃光區精密環境控制需求,檢測系統通過建立潔凈度-溫濕度-微振動的復合評估模型,使晶圓良品率提升1.2個百分點。而在深海鉆探裝備檢測中,采用壓力補償算法與抗腐蝕傳感技術后,設備在3000米水深條件下的連續工作時長延長了400%(數據來源:中海油2024年技術白皮書)。
隨著數字孿生技術與工業元宇宙的深度融合,使用條件檢測將向場景化、智能化方向加速演進。建議行業重點攻克三方面工作:建立覆蓋全產業鏈的工況數據庫,開發具備自學習能力的檢測算法,以及制定跨行業的檢測標準互認機制。未來三年,融合5G+AI的智能檢測體系有望將設備綜合效率(OEE)再提升15-20個百分點,為新型工業化建設提供堅實保障。

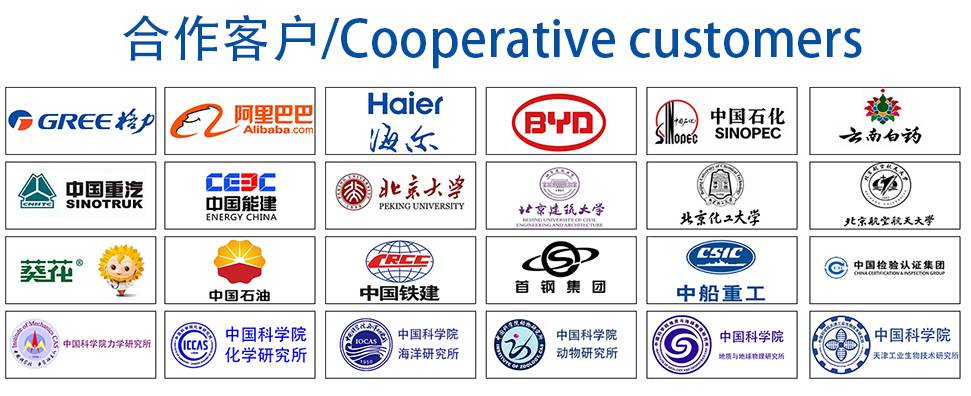