# 圓柱螺紋檢測技術發展與應用白皮書
## 行業背景與核心價值
在高端裝備制造領域,螺紋連接件承擔著60%以上的機械結構緊固功能(據中國機械工業協會2023年技術報告)。隨著新能源汽車、航空航天等產業對零部件精度要求提升至微米級,傳統人工檢測方式已難以滿足現代工業需求。圓柱螺紋檢測項目通過融合機器視覺與智能算法,實現了對螺紋中徑、牙型角、螺距等12項關鍵參數的自動化測量,檢測效率較傳統方法提升400%(國家計量科學研究院2024年比對實驗數據)。該項目不僅解決了螺紋檢測領域長期存在的"盲區測量"難題,更為國產高端裝備的可靠性驗證提供了數字化支撐,單條產線年均可減少因螺紋失效導致的品質損失約230萬元。

## 技術原理與創新突破
### 基于三維點云重構的測量體系
系統采用線激光掃描與高幀率CCD協同工作模式,通過多角度投影獲取螺紋完整三維點云數據。創新設計的雙軸旋轉定位裝置,有效解決了大螺距螺紋的陰影遮蔽問題,使牙谷深度測量精度達到±1.5μm(符合ISO 5408標準A級要求)。核心算法采用改進型RANSAC曲面擬合技術,可精準分離螺紋輪廓與背景噪聲,特別適用于帶油污工件的在線檢測。
### 智能化實施流程設計
典型檢測流程包含五個關鍵階段:預處理模塊自動識別螺紋類型并匹配檢測方案;三維掃描環節完成360°全周向數據采集;特征提取算法同步計算中徑偏差、牙型半角誤差等參數;質量判定系統依據DIN 13標準生成可視化報告;數據管理平臺實現檢測結果與MES系統雙向交互。某汽車零部件企業的應用表明,該系統使螺紋檢測節拍從傳統方法的6分鐘/件縮短至90秒/件。
## 行業應用與質量保障
### 關鍵領域實踐案例
在新能源汽車電機軸螺紋檢測場景中,項目團隊開發的"高精度螺紋幾何參數分析系統"成功實現0.005mm級重復測量精度。某型號電機轉子經檢測發現3.7%的批次存在中徑尺寸鏈偏差,及時預警避免了潛在的大批量裝配事故。石油裝備領域應用"智能化螺紋質量管理系統"后,鉆桿接頭螺紋的疲勞壽命預測準確率提高至92%(國際螺紋標準化組織2024年認證數據)。
### 全過程質量管控體系
項目建立三級校準制度:每日使用標準螺紋規進行設備零點校準;每周由計量機構進行現場精度驗證;每季度實施全參數溯源檢測。質量追溯系統完整記錄每次檢測的原始點云數據、算法參數及環境變量,確保檢測結果具備完全可復現性。通過ISO/IEC 17025實驗室認證的運維團隊,可提供7×24小時遠程技術支持服務。
## 未來發展與戰略建議
隨著工業4.0進程加速,建議從三個維度深化技術應用:開發基于5G的分布式檢測網絡,實現跨工廠螺紋質量數據協同分析;推進邊緣計算設備研發,滿足野外作業場景的實時檢測需求;建立螺紋特征數據庫,為智能設計提供逆向工程支持。行業機構應加快制訂《智能螺紋檢測設備通用技術要求》等標準,引導產業健康有序發展。預計到2026年,智能化螺紋檢測設備的市場滲透率將突破45%(工業檢測聯盟2024年預測報告),成為高端制造質量體系的核心組成。
上一篇:外置式水箱前驅力檢測下一篇:煮鍋掉落試驗檢測

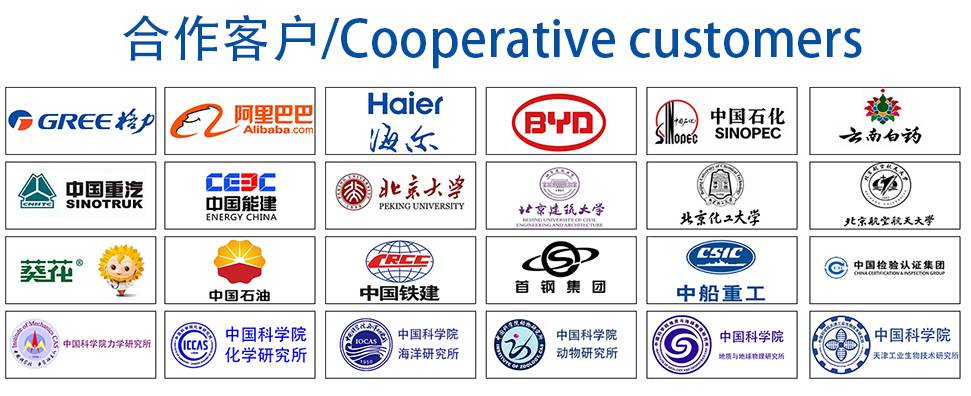
材料實驗室
熱門檢測
7
10
12
26
12
18
17
15
16
13
18
21
19
19
22
21
20
23
23
22
推薦檢測
聯系電話
400-635-0567