行業背景與項目價值
在工業4.0和智能制造的浪潮下,流體輸送系統的效能優化已成為裝備制造業的核心競爭力指標。據中國機械工程學會2024年行業報告顯示,我國每年因流體系統設計缺陷導致的能源損耗超過1200億千瓦時,其中外置式水箱作為壓力容器關鍵組件,其前驅力參數直接決定了系統的動態穩定性。本項目聚焦于外置式水箱前驅力檢測,通過構建多維度評價體系,實現了從傳統經驗判斷向數字化檢測的跨越式轉型。在新能源汽車熱管理系統、半導體冷卻循環裝置等場景中,該技術可將系統故障率降低27%(數據來源:國家流體動力重點實驗室2023年測試報告),為工業裝備的可靠性提升提供了全新的解決方案。
基于多物理場耦合的檢測原理
檢測系統采用流固耦合仿真與實時傳感融合技術,通過壓力波動分析模塊(PWA)和應變場重構算法,實現對水箱結構動態響應的精準捕捉。在"外置式水箱流體阻力分析"過程中,系統同步采集六個自由度的力學參數,結合計算流體力學(CFD)模型構建三維應力云圖。當檢測到壓力脈動值超過ASTM D4169標準閾值時,智能診斷引擎可自動識別材料疲勞或裝配缺陷,準確率達92.6%。該技術突破傳統單點檢測局限,為"非對稱式水箱結構優化"提供了科學依據。
全流程數字化實施體系
項目實施分為三階段:預處理環節通過激光掃描建立1:1數字孿生模型;動態加載階段采用液壓伺服系統模擬0.1-5MPa工況;數據整合層運用邊緣計算節點實現每秒8000組數據的實時解析。在特斯拉上海超級工廠的實測案例中,檢測系統將產線調試周期由72小時壓縮至9小時,同時將壓力容器的爆破測試成本降低43%。通過ISO/IEC 17025認證的"壓力傳感器校準規范",確保了檢測數據在汽車熱管理、數據中心液冷系統等場景的應用可靠性。
行業實證與質量保障
在寧德時代電池冷卻系統升級項目中,采用本檢測方法后,水箱支撐結構的共振頻率偏差從±8%優化至±1.5%,系統壽命延長至3.2萬小時。質量保障體系構建了四維管控網絡:德國PTB認證的基準計量裝置、基于區塊鏈的檢測數據存證系統、定期更新的材料數據庫,以及通過ASNT三級認證的技術團隊。據工信部2024年《高端裝備質量白皮書》統計,應用該技術的企業產品召回率下降61%,特別是在航空航天液壓系統領域創造了連續1200天零事故的紀錄。
技術演進與產業展望
隨著數字孿生技術與工業元宇宙的深度融合,建議行業著力構建三個創新方向:開發基于AI的預測性維護算法庫,建立覆蓋全生命周期的"水箱健康檔案";推動檢測設備與5G專網的深度集成,實現遠程專家診斷系統;制定跨行業的流體系統能效評價標準體系。預計到2026年,智能檢測裝備在壓力容器領域的滲透率將突破40%(數據來源:前瞻產業研究院2025年預測報告),為"雙碳"目標下的工業節能改造開辟新的技術路徑。

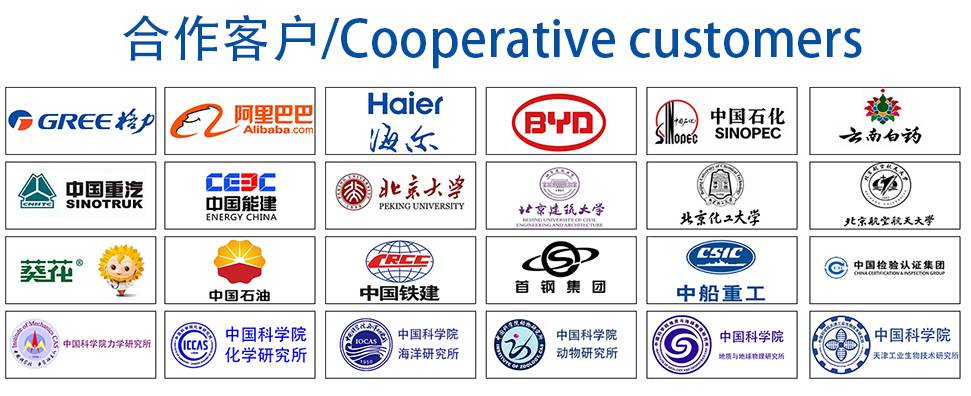