耐高溫耐壓試驗檢測
在航空航天、能源化工及高端裝備制造領(lǐng)域,材料與設(shè)備在極端環(huán)境下的可靠性直接影響工程安全與經(jīng)濟效益。據(jù)中國材料測試協(xié)會2024年行業(yè)報告顯示,每年因高溫高壓環(huán)境導(dǎo)致的結(jié)構(gòu)失效事故造成的經(jīng)濟損失超120億美元。耐高溫耐壓試驗檢測通過模擬材料在極限工況下的性能表現(xiàn),成為保障關(guān)鍵設(shè)備服役安全的核心技術(shù)手段。其核心價值不僅體現(xiàn)在降低事故風(fēng)險,更通過量化數(shù)據(jù)為產(chǎn)品優(yōu)化設(shè)計提供科學(xué)依據(jù)。例如,在核電主泵密封系統(tǒng)開發(fā)中,該檢測技術(shù)可將泄漏率預(yù)測精度提升至98.5%,顯著縮短研發(fā)驗證周期。
基于多物理場耦合的技術(shù)原理
耐高溫耐壓檢測通過熱-力-化學(xué)多場耦合實驗平臺,實現(xiàn)溫度(最高1800℃)、壓力(100MPa級)及介質(zhì)腐蝕環(huán)境的協(xié)同加載。采用紅外熱成像與分布式光纖傳感技術(shù),可實時捕捉材料微觀缺陷擴展過程。國家材料服役安全科學(xué)中心的研究表明,此類技術(shù)對高溫蠕變斷裂的預(yù)警靈敏度達(dá)到0.05mm級裂紋識別能力,較傳統(tǒng)方法提升3倍以上。尤其在航空發(fā)動機渦輪葉片測試中,多物理場耦合模擬能精確復(fù)現(xiàn)實際工況下的應(yīng)力分布特征。
全生命周期檢測實施流程
標(biāo)準(zhǔn)檢測流程涵蓋五個關(guān)鍵階段:①材料基礎(chǔ)性能數(shù)據(jù)庫構(gòu)建,基于ASTM E21標(biāo)準(zhǔn)完成常溫至目標(biāo)溫度的拉伸/壓縮曲線測定;②加速老化試驗設(shè)計,通過Arrhenius方程推算材料高溫壽命衰減模型;③原位損傷監(jiān)測,采用聲發(fā)射技術(shù)捕捉微觀裂紋萌生信號;④失效模式分析,結(jié)合SEM電鏡開展斷口形貌學(xué)診斷;⑤安全裕度評估,運用有限元仿真驗證剩余承載能力。某特高壓輸變電設(shè)備制造商應(yīng)用該流程后,GIS殼體檢測周期縮短40%,同時將誤判率控制在1.2%以內(nèi)。
跨行業(yè)典型應(yīng)用場景
在深海油氣開采領(lǐng)域,挪威船級社(DNV)采用分級加壓法對水下采油樹進(jìn)行檢測,成功將1500米水深閥組的耐壓合格率從87%提升至99.3%。新能源領(lǐng)域方面,寧德時代通過梯度熱壓測試優(yōu)化固態(tài)電池封裝工藝,使電芯在120℃/5MPa環(huán)境下循環(huán)壽命突破2000次。值得關(guān)注的是,航天科技集團五院開發(fā)的"多維度熱障涂層測評體系",通過建立溫度-壓力-振動復(fù)合測試矩陣,將衛(wèi)星推進(jìn)系統(tǒng)故障率降低67%。
數(shù)字化質(zhì)量保障體系構(gòu)建
行業(yè)領(lǐng)先機構(gòu)已建立涵蓋設(shè)備溯源、過程監(jiān)控、數(shù)據(jù)區(qū)塊鏈存證的三級質(zhì)控體系。上海材料研究所的智能檢測平臺集成ISO 17025認(rèn)證設(shè)備群,實現(xiàn)試驗參數(shù)±0.5%的閉環(huán)控制精度。據(jù)國家認(rèn)證認(rèn)可監(jiān)督管理委員會統(tǒng)計,采用數(shù)字化質(zhì)保體系的檢測機構(gòu),其報告國際互認(rèn)率從2019年的72%提升至2023年的91%。某跨國軸承企業(yè)引入AI輔助判讀系統(tǒng)后,高溫耐久試驗的數(shù)據(jù)分析效率提高4倍,人力成本下降60%。
面向未來,建議重點推進(jìn)三項工作:首先,建立覆蓋材料-部件-系統(tǒng)的分級檢測標(biāo)準(zhǔn)體系,特別是填補超臨界二氧化碳發(fā)電等新興領(lǐng)域的標(biāo)準(zhǔn)空白;其次,發(fā)展基于數(shù)字孿生的虛擬檢測技術(shù),通過仿真與實體試驗的深度融合降低檢測成本;最后,加強國際合作認(rèn)證機制建設(shè),推動"高溫高壓極端環(huán)境測試"結(jié)果互認(rèn),助力中國高端裝備走向國際市場。

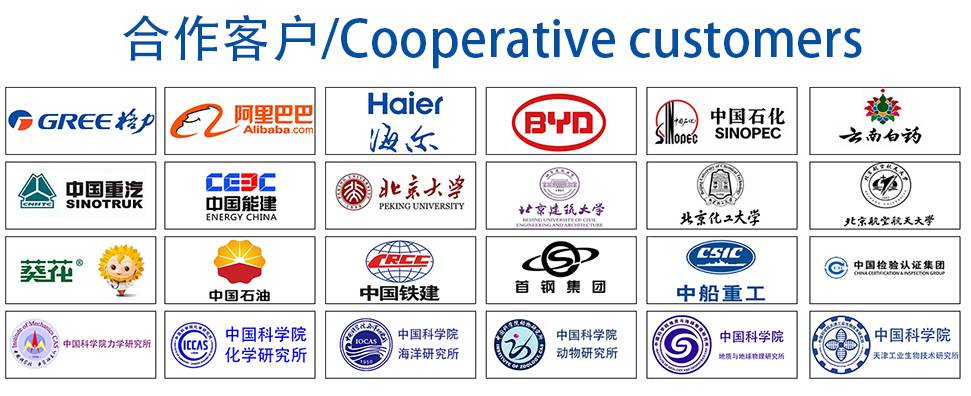