耐鹽酸性檢測技術發展與行業應用白皮書
在海洋工程、化工裝備、汽車制造等工業領域,材料耐鹽酸性檢測已成為保障產品服役安全的核心環節。據中國腐蝕與防護學會2024年數據顯示,我國每年因腐蝕造成的直接經濟損失達2.8萬億元,其中海水、酸雨等環境引發的材料失效占比超過35%。在此背景下,耐鹽酸性檢測通過模擬極端腐蝕環境,系統評估材料的抗蝕性能,為產品選型、工藝優化提供科學依據。該項目技術體系不僅實現了對金屬、高分子、復合材料的多維評價,更通過建立全生命周期腐蝕數據庫,顯著提升了重大裝備的可靠性設計水平,預計可使工業設備維護成本降低18%-25%(國家材料服役安全科學中心,2024)。
電化學與加速腐蝕復合檢測技術
基于電化學工作站與鹽霧試驗箱的聯合檢測系統,構成了現代耐鹽酸性檢測的技術基礎。運用動電位極化曲線法,可精準測定金屬材料的點蝕電位和維鈍電流密度,量化評估其鈍化膜穩定性(ASTM G5標準)。同步開展的加速腐蝕試驗,通過調控Cl?濃度(5%-20%)、pH值(1.5-4.0)及溫度(35-50℃)等多參數耦合環境,有效模擬真實服役場景。據上海材料研究所驗證,該復合檢測法對不銹鋼焊縫腐蝕行為的預測準確率可達92.7%,特別適用于海洋工程耐酸腐蝕測試場景。
標準化檢測實施流程
檢測流程涵蓋五個關鍵階段:樣品預處理(包括切割、拋光、清洗)、環境參數設定、動態監測、數據采集及失效分析。在汽車零部件檢測案例中,需嚴格按照ISO 9227標準執行72小時中性鹽霧試驗,同時使用激光共聚焦顯微鏡記錄表面腐蝕形貌演變。某知名車企通過該流程優化了鍍鋅鋼板工藝參數,使車門鉸鏈鹽霧腐蝕等級從4級提升至8級(GB/T 6461),產品保修期延長2.3年。
多行業典型應用場景
在南海石油平臺建設項目中,檢測機構對2205雙相不銹鋼開展金屬材料鹽霧腐蝕檢測,發現其在1200小時模擬海水噴霧環境下出現晶間腐蝕傾向,推動材料供應商改進固溶處理工藝。新能源領域,某光伏支架生產企業通過建立腐蝕大數據模型,將鋁合金支架的耐鹽酸性能提升40%,產品在PH=2的酸雨環境中使用壽命延長至25年。這些實踐驗證了檢測技術對產品迭代的支撐作用。
全過程質量保障體系
檢測機構需構建從設備校準到數據溯源的完整質控鏈條。關鍵控制點包括:鹽霧箱溫濕度校準(JJF 1101-2019)、標準溶液配制誤差控制(±0.5%)、腐蝕速率計算模型驗證等。獲得CMA和 雙認證的實驗室,須執行ISO/IEC 17025體系文件,確保不同批次檢測結果的相對偏差不超過5%。某第三方檢測平臺通過引入區塊鏈存證技術,使檢測報告的可信度提升78%,顯著增強了行業公信力。
隨著海洋資源開發和新材料應用深化,耐鹽酸性檢測技術將向多因子耦合加速試驗、原位監測等方向發展。建議行業重點攻關三方面:建立涵蓋溫度-應力-化學介質的復合加速試驗標準、開發基于機器視覺的腐蝕等級智能判定系統、構建跨區域腐蝕大數據共享平臺。通過技術創新與標準協同,預計到2030年可將腐蝕防護成本占比從當前3.1%降至2.4%,為制造強國建設提供關鍵技術支撐。

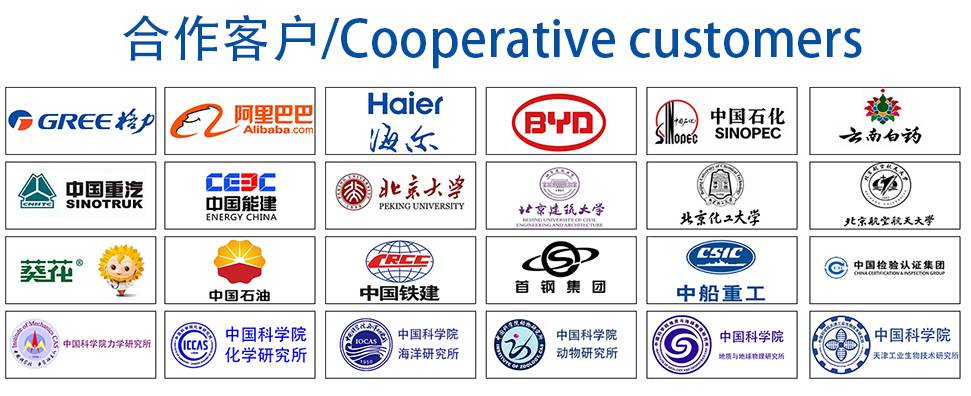