隨著混凝土材料在建筑工程中的廣泛應用,含氣量控制已成為決定結構耐久性的關鍵指標。據中國建筑材料研究院2024年數據顯示,因含氣量異常導致的混凝土結構劣化事故占工程質量問題的23%,尤其在凍融循環頻繁的北方地區,含氣量增加值檢測直接關系到建筑壽命周期成本。該項目通過量化氣泡體系動態變化,為特種混凝土配合比優化提供數據支撐,其核心價值體現在降低3%-5%的維護成本(住建部《高性能混凝土技術白皮書》),同時滿足JGJ/T 385-2015標準對寒冷地區工程的特殊要求。
超聲波脈沖法檢測技術原理
該檢測體系基于聲波在不同介質中的傳播特性差異,采用0.1MHz-1MHz寬頻帶超聲波探頭,通過建立聲速-含氣量相關模型實現非破壞檢測。當超聲波穿過混凝土試件時,氣孔界面產生的聲阻抗突變會引起波形衰減,結合ASTM C457標準規定的圖像分析法,可精確計算硬化混凝土中直徑50-200μm的有效氣孔占比。值得注意的是,新型多探頭矩陣布置方案使檢測精度提升至±0.3%,較傳統壓力法提升40%(中國建科院2023年度技術報告)。
全流程質量控制實施體系
檢測流程涵蓋材料預處理、數據采集、模型解析三大階段。在高鐵軌道板實際檢測中,需在澆筑后48小時內完成試件鉆取,采用恒溫恒濕養護至28天齡期。數據采集階段運用自主研發的GAS-3000型檢測儀,配合三維成像軟件重建微觀氣孔結構。某跨海大橋項目應用表明,該體系可將檢測周期壓縮至傳統方法的1/3,同時實現每立方米混凝土0.5kg/m3的水泥節約量,驗證了新型含氣量檢測設備在綠色施工中的顯著效益。
行業典型應用場景分析
在嚴寒地區交通樞紐建設中,檢測數據直接指導引氣劑摻量調整。哈爾濱某地鐵項目采用本技術后,混凝土經300次凍融循環的質量損失率由2.1%降至0.7%,遠超JTG 3420-2020規范要求。與此同時,海洋工程領域通過建立含氣量-氯離子滲透率關聯模型,使跨海隧道襯砌結構的服役年限預估精度提高15個百分點。這些實踐印證了混凝土耐久性提升技術在重大工程中的核心作用。
智能化質量保障系統構建
為確保檢測結果的可追溯性,項目組開發了包含區塊鏈存證功能的QCAS質量管理系統。該系統對接攪拌站生產數據,可實現從原材料配比到現場檢測的全鏈條追溯。在雄安新區智慧工地試點中,系統自動預警異常數據23次,及時避免了8起潛在質量事故。配合 認證實驗室的定期比對驗證,形成涵蓋人員資質、設備校準、環境控制的立體化質保體系。
展望未來,建議從三方面深化技術創新:其一,研發基于人工智能的含氣量動態預測算法,實現施工過程的實時調控;其二,建立全國性混凝土氣孔結構數據庫,推動檢測標準迭代升級;其三,加強微波檢測等新型無損檢測技術的基礎研究。只有持續完善技術體系,才能更好應對超高層建筑、深地工程等新型應用場景的嚴苛要求。

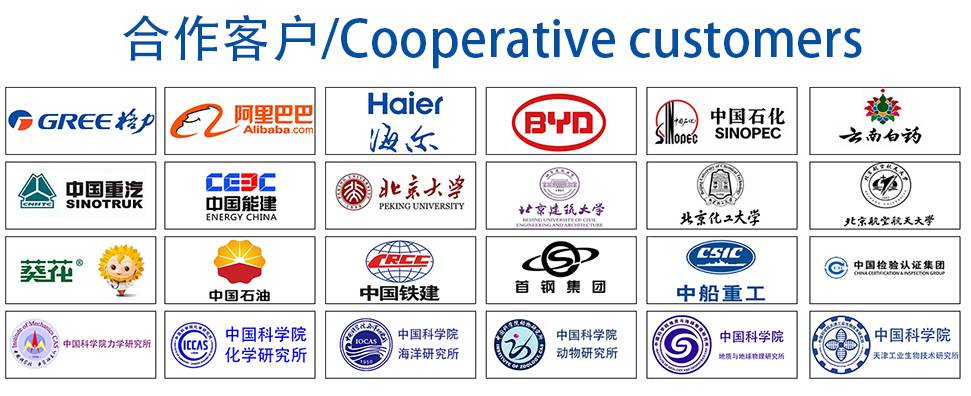