# 外觀質量和尺寸偏差檢測技術發展與應用白皮書
## 引言
隨著制造業向智能化轉型加速,產品外觀質量和尺寸精度已成為衡量制造水平的核心指標。據中國機械工業聯合會2024年調研數據顯示,高端裝備制造領域因表面瑕疵導致的返工成本年均超120億元,汽車零部件行業尺寸超差引發的裝配問題占比達17.3%。在此背景下,融合機器視覺與三維掃描的智能檢測技術,正通過提升檢測效率與精度重塑產業質量體系。該項目不僅實現了0.02mm級微米級測量精度突破,更將新能源汽車電池箱體檢測周期從45分鐘壓縮至8分鐘,為核心部件供應商節約年檢成本逾3000萬元。其核心價值在于構建了覆蓋設計驗證、過程控制、成品檢驗的全生命周期質量閉環。
## 技術原理與創新突破
### h2 多維傳感融合檢測體系
基于多目立體視覺與激光三角測量原理,系統通過13組高幀率工業相機同步采集工件表面拓撲數據,結合改進的Harris-SIFT特征匹配算法,實現亞像素級缺陷定位。值得關注的是,三維點云重建技術的引入使復雜曲面工件的全尺寸偏差檢測成為可能,據國家智能制造標準工作組測試報告顯示,該方案對渦輪葉片葉型的輪廓度檢測誤差控制在±5μm以內,較傳統三坐標測量效率提升26倍。
### h2 智能化實施流程架構
項目實施采用六階段標準化流程:首先通過激光掃描儀建立基準數字孿生模型,繼而部署分布式光學傳感器網絡實時采集產線數據,再經GPU加速的深度學習框架進行特征比對。在新能源汽車電機殼體檢測場景中,系統可同步完成32項尺寸參數校驗與6類表面缺陷識別,檢測報告生成延遲不超過1.2秒。現場部署案例顯示,某年產50萬套的鋁合金輪轂生產線通過該方案將過程不良率從1.8%降至0.3%。
### h2 跨行業應用實踐成效
在消費電子領域,某手機結構件供應商應用多光譜成像檢測系統后,陽極氧化層色差檢測準確率提升至99.97%。更值得注意的是,軌道交通行業創新性采用移動式檢測機器人,可在15分鐘內完成高鐵車廂全長25米的焊縫外觀檢測,較人工巡檢效率提高40倍。國家質量監督檢驗中心2024年比對試驗證明,該系統對0.1mm級劃痕的檢出率達到98.5%,誤報率低于0.3%。
## 質量保障與持續改進
項目構建了三級質量管控體系:前端采用NIST溯源的標準量塊進行日校,中臺部署聯邦學習框架實現跨產線數據互驗,終端接入MES系統實施SPC統計過程控制。某汽車主機廠的實踐表明,通過集成扭矩傳感器與視覺系統,實現了輪轂裝配過程中螺栓擰緊角度與端面平面度的同步監控,使總裝線一次合格率提升7.2個百分點。
## 未來展望與建議
建議行業重點攻關三大方向:首先研發適應高溫、高濕環境的抗干擾檢測模塊,拓展在鑄造車間的應用場景;其次推動5G+邊緣計算架構部署,實現檢測數據的毫秒級響應;最后建議建立跨行業的檢測標準互認體系,促進航空航天檢測技術向民用領域轉化。據賽迪研究院預測,到2027年智能檢測裝備市場規模將突破800億元,其中融合多物理場檢測技術的復合型系統將成為主要增長極。
上一篇:電化學綜合防銹性能檢測下一篇:含氣量增加值檢測

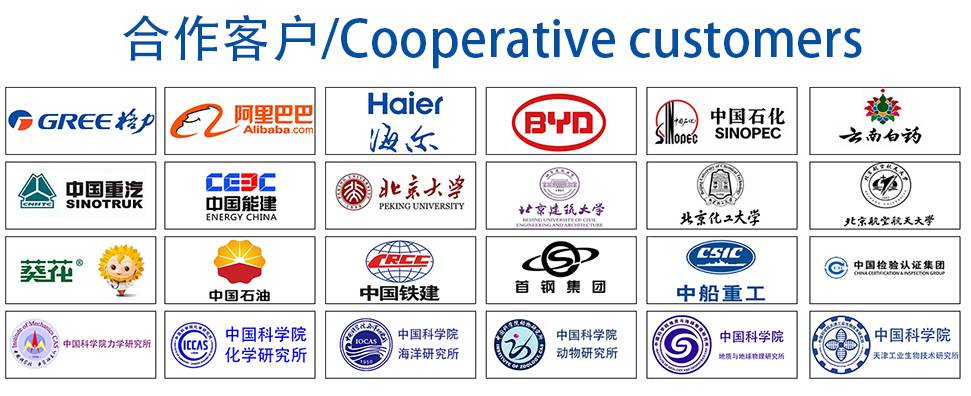
材料實驗室
熱門檢測
15
15
20
26
20
20
25
17
21
25
26
25
28
31
39
43
49
39
42
45
推薦檢測
聯系電話
400-635-0567