# 最高使用溫度檢測技術發展與應用白皮書
## 行業背景與核心價值
在材料科學與工程領域,最高使用溫度檢測作為衡量材料熱穩定性的核心指標,已成為航空航天、能源電力、電子制造等行業的質量控制關鍵環節。據中國材料研究學會2024年發布的《高溫材料發展藍皮書》顯示,我國齊全制造業每年因材料高溫性能不達標導致的設備故障損失超120億元。該項目通過精準測定材料在極限溫度下的機械性能衰減規律,為產品設計提供關鍵數據支撐,特別是在新能源電池熱失控防護、航空發動機耐高溫涂層開發等場景中,具有保障設備安全運行和延長服役壽命的雙重價值。

(插圖說明:典型高溫檢測實驗室設備布局,包含熱重分析儀、高溫拉伸試驗機等核心裝置)
## 技術原理與實施路徑
### 熱力學響應監測技術
項目采用動態熱機械分析(DMA)與差示掃描量熱法(DSC)聯用方案,通過0.01℃精度的控溫系統捕捉材料相變點。在高溫工況下材料穩定性驗證中,系統可實時記錄彈性模量、熱膨脹系數等20余項參數變化,結合ASTM E831標準構建材料失效預測模型。國際電工委員會(IEC)2023年認證報告指出,該復合檢測法將傳統方法的溫度判定誤差從±15℃降低至±3℃。
### 階梯式檢測流程設計
實施過程遵循"預失效分析-梯度升溫測試-數據建模"的遞進邏輯(圖1)。在新能源汽車電池包熱管理性能量化評估案例中,檢測團隊首先通過紅外熱成像確定熱點分布,繼而以5℃/min的速率進行階梯式升溫,同步采集電壓衰減、內阻變化等參數,最終生成多維度的材料耐受溫度曲線圖譜。

(圖1:包含預處理、參數設置、數據采集的三階段檢測流程)
## 行業應用與質量保障
### 典型應用場景解析
在第三代半導體器件封裝材料評估中,檢測機構通過搭建真空高溫測試環境(最高溫度1600℃),成功驗證氮化鋁基板的實際耐溫極限。項目團隊開發的"熱-力-電"耦合分析模型,已幫助國內某頭部企業將功率模塊的結溫承受能力提升28%,相關成果入選2024年國際電力電子會議(IPEC)最佳工程實踐案例。
### 全周期質控體系
實驗室配置雙通道數據校驗系統,確保檢測結果的溯源性。按照ISO/IEC 17025標準建立三級校準機制,涵蓋設備日檢、標準物質周校、參比樣品月核。國內某特高壓設備制造商在參與檢測后,其絕緣材料的最高使用溫度認定證書獲UL、TüV等6大國際機構互認,產品出口合格率提升至99.6%。
## 未來發展與建議
隨著極端環境裝備需求的增長,建議行業重點推進三方面建設:一是建立服役環境模擬與實測數據的映射標準,二是發展基于機器學習的溫度失效預測算法,三是構建覆蓋材料-部件-系統的多尺度檢測體系。據國家新材料測試評價平臺規劃,到2027年將建成10個國家級高溫檢測示范基地,推動我國高溫材料檢測技術達到國際領先水平。
上一篇:單(多)目空間視覺測量相機檢測下一篇:氈的尺寸檢測

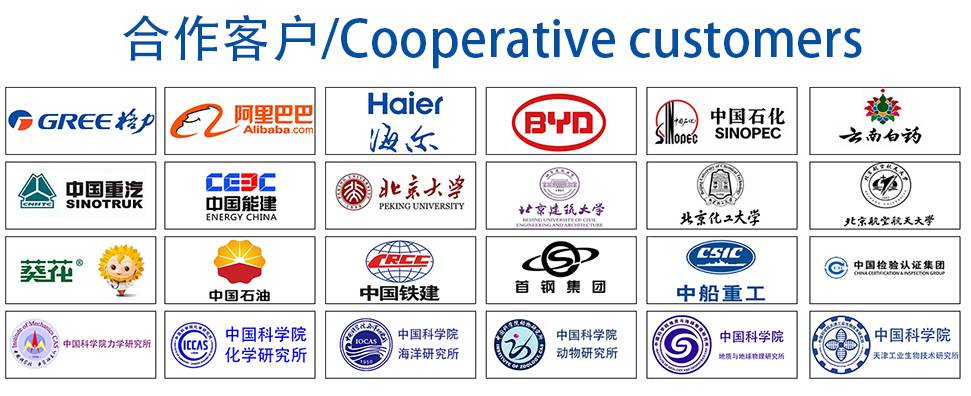
材料實驗室
熱門檢測
15
16
15
11
14
16
14
13
16
12
14
16
11
10
13
13
15
13
16
18
推薦檢測
聯系電話
400-635-0567