# 鋁及鋁合金成分添加劑檢測技術發展與應用白皮書
## 一、行業背景與戰略價值
隨著新能源汽車與航空航天產業的快速發展,2024年鋁合金市場規模預計突破2500億美元(據中國有色金屬工業協會數據)。在此背景下,鋁及鋁合金成分添加劑檢測作為金屬材料質量控制的關鍵環節,直接影響材料強度、耐腐蝕性及加工性能。當前行業面臨三大痛點:摻假添加劑導致的材料失效、微量元素控制失準引發的性能波動,以及再生鋁循環利用中的雜質累積問題。通過精準的成分檢測,企業可實現原料成本優化15%-20%(國家新材料測試評價中心案例),同時推動高強輕量化鋁合金的研發突破。其核心價值體現在質量溯源體系構建、生產工藝優化和產品全生命周期管理三大維度。

## 二、技術體系與實施路徑
### h2 1. 多模態檢測技術融合
當前主流檢測體系結合光譜分析(OES)、質譜分析(ICP-MS)和X射線熒光光譜(XRF)三大技術。以電感耦合等離子體質譜法為例,其檢測限可達ppb級,能精準識別硼、鈦等微量添加劑。值得注意的是,XRF技術憑借無損檢測特性,在再生鋁現場快速篩查中展現獨特優勢,某汽車板材生產商通過部署在線XRF系統,使檢測效率提升300%。
### h2 2. 全流程質量管控模型
典型檢測流程包含四個關鍵階段:
1. **前處理標準化**:采用數控切割機制備φ30mm標準試樣,表面粗糙度控制在Ra0.8μm以內
2. **儀器參數優化**:建立包含32種元素的特征譜線數據庫,能量分辨率設置≤0.02nm
3. **數據智能解析**:應用機器學習算法校正基體效應,某研究院驗證顯示算法可使鐵元素檢測誤差降低67%
4. **結果可視化輸出**:生成符合ISO/IEC 17025標準的數字化檢測報告
### h2 3. 行業應用范式創新
在航空航天領域,某型號航空鋁材通過建立"添加劑-工藝參數-力學性能"關聯模型,使材料延伸率波動范圍從±5%壓縮至±1.5%。新能源汽車電池托盤生產中,企業運用動態成分監控系統,成功將鎂元素偏差率控制在0.03%以內,產品疲勞壽命提升2.8倍。這些實踐印證了"鋁合金添加劑精準調控"技術路線的可行性。
## 三、質量保障與標準演進
行業現已構建四級質量保障體系:
- **設備層**:強制周期性計量校準,配備NIST標準物質
- **操作層**:實施ASTM E1251-17a標準操作程序
- **數據層**:建立實驗室信息管理系統(LIMS),數據完整率達99.98%
- **認證層**:通過 、NADCAP等國際認證
最新發布的GB/T 20975.35-2024標準,首次將鋰、鈧等戰略元素納入強制檢測范疇,標志著檢測技術從通用型向專用型轉變。值得關注的是,數字化證書上鏈存證等創新應用,正在重構質量信任體系。
## 四、發展趨勢與策略建議
面向2025年,行業發展呈現三大趨勢:微型化檢測設備滲透率將突破40%、AI輔助決策系統覆蓋率預計達75%、檢測-工藝閉環控制系統將成為高端制造標配。建議行業重點布局:
1. 開發適用于鋁熔體原位檢測的微型傳感器陣列
2. 建立覆蓋全產業鏈的添加劑成分數據庫
3. 推動檢測標準與歐盟REACH法規接軌
4. 培育"檢測服務+工藝優化"的增值服務模式
隨著"雙碳"戰略深入推進,鋁及鋁合金成分檢測技術將在材料循環經濟中發揮更重要作用。建議龍頭企業牽頭組建檢測技術聯盟,共同攻克高純鋁(99.999%)雜質檢測等"卡脖子"難題,推動我國從鋁合金生產大國向技術強國跨越。
上一篇:電動汽車用電子元器件檢測下一篇:惡臭(臭氣)檢測

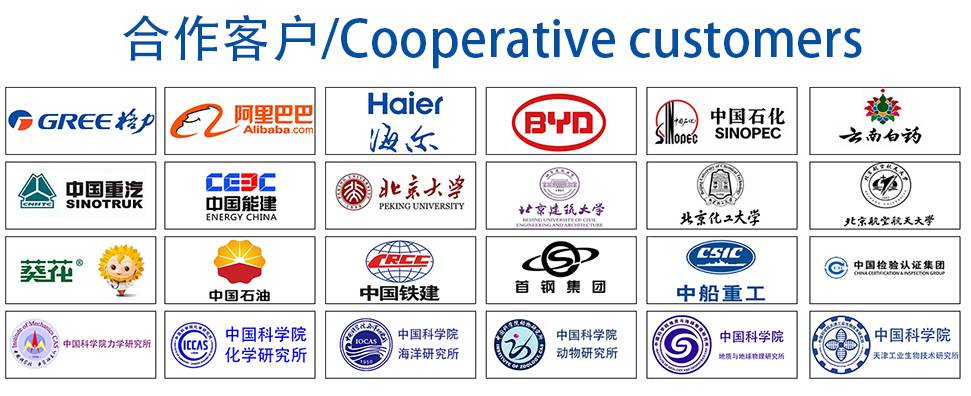
材料實驗室
熱門檢測
推薦檢測
聯系電話
400-635-0567