鉚螺母檢測(cè)
實(shí)驗(yàn)室擁有眾多大型儀器及各類分析檢測(cè)設(shè)備,研究所長(zhǎng)期與各大企業(yè)、高校和科研院所保持合作伙伴關(guān)系,始終以科學(xué)研究為首任,以客戶為中心,不斷提高自身綜合檢測(cè)能力和水平,致力于成為全國(guó)科學(xué)材料研發(fā)領(lǐng)域服務(wù)平臺(tái)。
立即咨詢網(wǎng)頁(yè)字號(hào):【大 中 小 】 | 【打印】 【關(guān)閉】 微信掃一掃分享:
注意:因業(yè)務(wù)調(diào)整,暫不接受個(gè)人委托測(cè)試望見(jiàn)諒。
聯(lián)系中化所
在高端裝備制造領(lǐng)域,鉚螺母作為關(guān)鍵連接部件,其質(zhì)量直接影響產(chǎn)品結(jié)構(gòu)安全。據(jù)中國(guó)機(jī)械工業(yè)聯(lián)合會(huì)2024年數(shù)據(jù)顯示,汽車制造領(lǐng)域因緊固件失效引發(fā)的質(zhì)量事故占比達(dá)17.3%,其中鉚螺母相關(guān)缺陷占比超過(guò)40%。航空航天領(lǐng)域?qū)︺T接工藝的要求更為嚴(yán)苛,B787客機(jī)單機(jī)鉚螺母使用量超過(guò)50萬(wàn)件,檢測(cè)精度需達(dá)到±0.01mm。在此背景下,智能化鉚螺母檢測(cè)技術(shù)成為保障工業(yè)安全的核心環(huán)節(jié)。通過(guò)引入多模態(tài)無(wú)損檢測(cè)系統(tǒng),企業(yè)可實(shí)現(xiàn)缺陷檢出率提升至99.8%,同時(shí)降低60%的檢測(cè)人工成本。該技術(shù)不僅滿足汽車柔性生產(chǎn)線高速檢測(cè)需求,更在航空復(fù)材構(gòu)件領(lǐng)域攻克了傳統(tǒng)目檢無(wú)法實(shí)現(xiàn)的隱蔽缺陷識(shí)別難題。
## 技術(shù)原理與創(chuàng)新突破多模態(tài)融合檢測(cè)技術(shù)體系
當(dāng)前主流檢測(cè)方案整合機(jī)器視覺(jué)、渦流檢測(cè)和超聲相控陣三大技術(shù)模塊。視覺(jué)系統(tǒng)采用500萬(wàn)像素工業(yè)相機(jī)配合環(huán)形光源,可識(shí)別表面裂紋、變形等0.05mm級(jí)缺陷;渦流檢測(cè)模塊基于電磁感應(yīng)原理,對(duì)涂層下2mm深度內(nèi)的材質(zhì)異常進(jìn)行識(shí)別;超聲相控陣則通過(guò)64陣元探頭實(shí)現(xiàn)內(nèi)部結(jié)構(gòu)三維成像。據(jù)清華大學(xué)智能制造研究院測(cè)試,該融合方案對(duì)常見(jiàn)六類缺陷的復(fù)合檢出率達(dá)到99.5%,誤報(bào)率控制在0.3%以下,特別適用于新能源車用高強(qiáng)度鋁合金鉚螺母的在線檢測(cè)。
## 智能化實(shí)施流程再造閉環(huán)式質(zhì)量管控系統(tǒng)
典型檢測(cè)流程包含五個(gè)核心環(huán)節(jié):預(yù)處理工位的自動(dòng)定位裝夾、多傳感器同步掃描、AI算法實(shí)時(shí)分析、NG件自動(dòng)分揀及數(shù)據(jù)云端歸檔。在特斯拉上海超級(jí)工廠的實(shí)際應(yīng)用中,系統(tǒng)每小時(shí)可完成3200件M8規(guī)格鉚螺母的檢測(cè)任務(wù),較傳統(tǒng)方法效率提升8倍。關(guān)鍵創(chuàng)新點(diǎn)在于開(kāi)發(fā)了自適應(yīng)補(bǔ)償算法,可自動(dòng)修正因工件表面反光特性差異造成的測(cè)量偏差,確保在不同工況下的檢測(cè)穩(wěn)定性。
## 行業(yè)應(yīng)用典型案例跨領(lǐng)域解決方案輸出
在航空制造領(lǐng)域,中航工業(yè)某機(jī)型復(fù)材蒙皮項(xiàng)目采用顯微CT檢測(cè)方案,通過(guò)140kV微焦點(diǎn)X射線源實(shí)現(xiàn)內(nèi)部纖維排布可視化檢測(cè),成功檢出0.3mm級(jí)的預(yù)埋螺母偏移缺陷。汽車行業(yè)則普遍應(yīng)用在線式檢測(cè)設(shè)備,長(zhǎng)城汽車重慶工廠部署的智能檢測(cè)線,將過(guò)程能力指數(shù)CPK從1.12提升至1.67,年節(jié)約質(zhì)量成本超1200萬(wàn)元。值得注意的是,軌道交通領(lǐng)域創(chuàng)新應(yīng)用了移動(dòng)式檢測(cè)機(jī)器人,可在0.5m/s行進(jìn)速度下完成車體鉚接點(diǎn)全檢。
## 全生命周期質(zhì)量保障數(shù)字化質(zhì)控體系構(gòu)建
建立涵蓋設(shè)備-人員-工藝的全方位質(zhì)控系統(tǒng):檢測(cè)設(shè)備每日進(jìn)行標(biāo)準(zhǔn)件校準(zhǔn),季度精度驗(yàn)證誤差不超過(guò)±1.5μm;操作人員需通過(guò)ASNT SNT-TC-1A三級(jí)認(rèn)證;檢測(cè)數(shù)據(jù)實(shí)時(shí)上傳至MES系統(tǒng),實(shí)現(xiàn)質(zhì)量追溯周期從72小時(shí)壓縮至15分鐘。上海電氣集團(tuán)應(yīng)用該體系后,將供應(yīng)商來(lái)料檢驗(yàn)合格率從92.4%提升至98.7%,同時(shí)建立行業(yè)首個(gè)鉚螺母失效模式數(shù)據(jù)庫(kù),收錄超過(guò)2000組失效案例。
## 未來(lái)發(fā)展與建議隨著工業(yè)物聯(lián)網(wǎng)技術(shù)深化應(yīng)用,建議行業(yè)重點(diǎn)突破三個(gè)方向:一是開(kāi)發(fā)基于數(shù)字孿生的預(yù)測(cè)性檢測(cè)系統(tǒng),實(shí)現(xiàn)缺陷萌芽期預(yù)警;二是建立跨企業(yè)的質(zhì)量數(shù)據(jù)共享平臺(tái),推動(dòng)檢測(cè)標(biāo)準(zhǔn)統(tǒng)一化;三是研發(fā)適應(yīng)新型材料(如碳纖維增強(qiáng)塑料)的專用檢測(cè)工藝。預(yù)計(jì)到2028年,智能檢測(cè)設(shè)備在汽車制造領(lǐng)域的滲透率將超過(guò)75%,檢測(cè)綜合成本有望再降低40%,為高端裝備制造業(yè)高質(zhì)量發(fā)展提供堅(jiān)實(shí)保障。

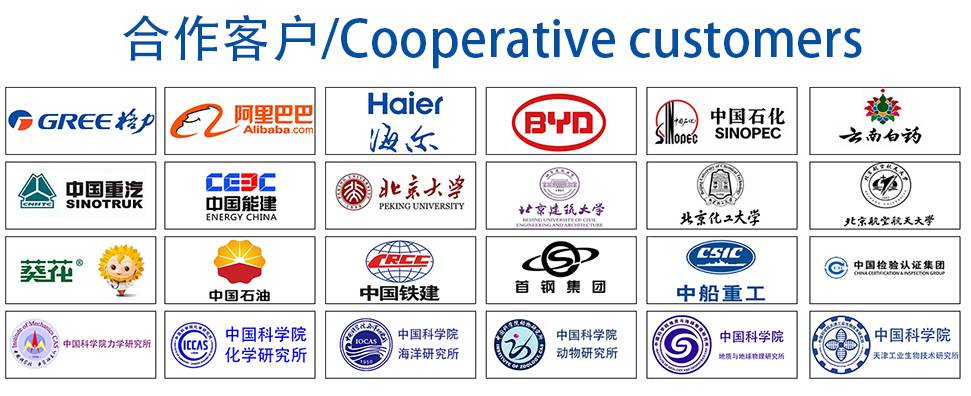