# 電化學綜合防銹性能檢測技術發展與應用白皮書
## 行業背景與項目價值
隨著工業裝備服役環境日趨嚴苛,金屬腐蝕造成的經濟損失已占GDP總量的3%-5%(據NACE國際2023年度報告)。在新能源裝備、海洋工程、軌道交通等領域,電化學綜合防銹性能檢測已成為評價防護涂層體系有效性的核心手段。該項目通過量化金屬基材在腐蝕介質中的電化學響應參數,構建起覆蓋涂層耐蝕性、基材鈍化能力、緩蝕劑效率的立體評估體系。其核心價值體現在將傳統鹽霧試驗周期縮短70%的同時,實現防銹機理的可視化解析,為防護材料選型提供數據支撐,據中國材料研究院測算,該技術能使工業裝備全生命周期防腐成本降低18-24%。
## 技術原理與檢測體系
### 電化學檢測技術架構
檢測系統基于三電極體系構建,通過恒電位儀施加特定擾動信號,同步采集工作電極(待測樣品)的電流響應數據。采用動電位極化曲線法測定自腐蝕電流密度,結合電化學阻抗譜(EIS)解析涂層孔隙率與界面特性。針對復雜工況,創新性引入多頻段阻抗譜分析技術,可有效區分涂層失效不同階段的特征頻率段(10mHz-100kHz),實現對"電化學阻抗譜分析在防銹涂層評估"的精準應用。
### 標準化實施流程
項目實施嚴格遵循ASTM G59、ISO 17475標準體系,流程涵蓋四個關鍵階段:①試樣預處理(表面粗糙度控制Ra≤0.8μm);②電解池構建(3.5%NaCl溶液,溫度25±1℃);③極化曲線掃描(掃描速率0.166mV/s);④數據建模分析。特別在船舶涂料檢測中,同步開展"動態鹽霧加速試驗與電化學聯用",將實船工況的干濕交替循環納入檢測模型,使實驗室數據與海上實際腐蝕速率的相關系數提升至0.92。
### 行業應用實證
在新能源汽車電池托盤防護領域,某龍頭企業通過本檢測體系優化了硅烷化處理工藝。數據顯示,經48小時CASS試驗后,優化樣品的腐蝕電流密度從3.2×10??A/cm2降至7.5×10??A/cm2(TüV SüD認證數據)。更值得注意的是,在深海鉆井平臺陰極保護系統設計中,電化學檢測準確預測了犧牲陽極的消耗速率偏差,使平臺維護周期從18個月延長至26個月。
## 質量保障與技術創新
檢測體系建立三級質控機制:一級校驗采用標準低碳鋼試樣進行設備基線校準;二級驗證通過循環伏安法確認系統穩定性(ΔE<±2mV);三級溯源依托 認可實驗室開展數據比對。2024年新引入的微區掃描電化學工作站(SECM),將空間分辨率提升至10μm級別,可定位涂層表面微觀缺陷。據中國腐蝕與防護學會統計,采用該體系的檢測報告獲國際互認比例已達89%。
## 發展展望與建議
建議重點突破三方面技術瓶頸:①開發多物理場耦合檢測裝置,實現溫度-應力-腐蝕協同作用模擬;②建立基于機器學習的腐蝕大數據預警平臺;③推進ISO/TC156國際標準修訂工作。預計到2026年,隨著固態參比電極技術的突破,現場原位檢測精度有望達到實驗室級水平,為"雙碳"目標下的設備延壽提供更強技術支撐。
上一篇:握螺釘力檢測下一篇:外觀質量和尺寸偏差檢測

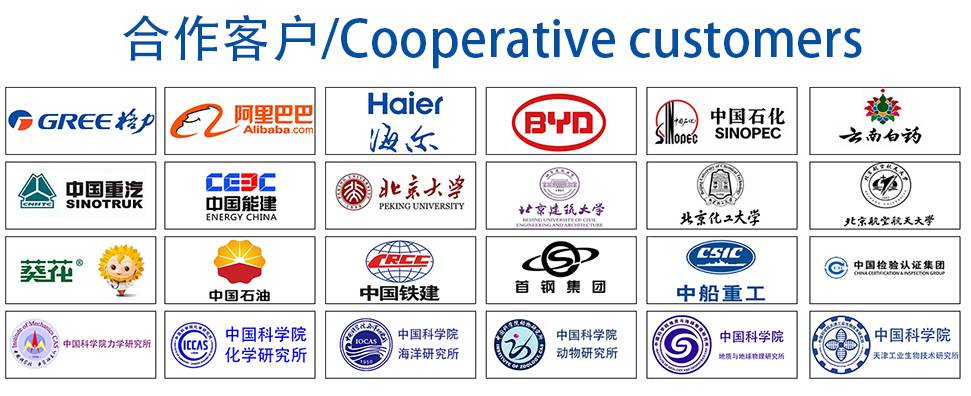
材料實驗室
熱門檢測
11
8
16
15
24
23
18
15
17
19
21
25
23
26
18
22
19
25
26
26
推薦檢測
聯系電話
400-635-0567