立方體抗壓強度試驗檢測技術白皮書
隨著建筑行業向高質量發展轉型,混凝土結構的安全性評估已成為工程質控的核心環節。立方體抗壓強度試驗作為建筑材料力學性能檢測的基準方法,被納入82%國家的強制性驗收標準(據國際建筑材料協會2023年度報告)。該項目通過測定標準養護條件下150mm×150mm×150mm試件的極限承載力,為混凝土配合比優化、施工工藝調整及結構耐久性評估提供關鍵數據支撐。其核心價值體現在三方面:一是構建了從實驗室到工程現場的標準化質量傳遞鏈條;二是為超高層建筑、大跨度橋梁等特種工程的結構安全提供了量化依據;三是推動形成了覆蓋原材料、生產、施工全周期的質量追溯體系。
1. 檢測技術原理與標準化體系
試驗依據GB/T 50081-2019《混凝土物理力學性能試驗方法標準》,采用液壓伺服壓力試驗機對標準養護28天的立方體試件進行軸向加載。通過測量試件破壞時的最大荷載值,按公式fcu=F/A計算抗壓強度,其中A為試件承壓面積。值得注意的是,試件尺寸效應修正系數需根據《公路工程水泥混凝土試驗規程》JTG 3420-2020進行調整,確保檢測結果可比性。該方法的相對誤差可控制在±2%以內(中國建材研究院驗證數據),成為工程質量糾紛仲裁的法定依據。
2. 全流程標準化實施體系
檢測流程涵蓋五個關鍵階段:①現場取樣階段,要求每100m3混凝土至少制作3組試件,預拌混凝土攪拌站需執行每日強度抽檢;②試件制備階段,嚴格按ISO 1920-3:2019標準控制振搗頻率與養護溫濕度;③試驗加載階段,采用0.5MPa/s±0.05MPa/s的速率控制要求,配備激光對中裝置確保荷載作用線偏差小于1mm;④數據處理階段,運用Grubbs準則剔除異常值,當組內極差超過15%時強制復檢;⑤報告生成階段,同步上傳區塊鏈存證系統,實現檢測數據的不可篡改性。某跨海大橋項目通過該體系,將強度離散系數從8.7%降至4.2%。
3. 典型行業應用場景分析
在高鐵無砟軌道板生產中,強度檢測數據直接決定CRTSⅢ型板式軌道的服役壽命。某線路項目通過建立強度-彈性模量-耐久性的多維關聯模型,將軌道板設計壽命從60年提升至100年。裝配式建筑領域,預制構件廠運用強度檢測數據進行蒸汽養護制度優化,使脫模強度達標時間縮短40%。值得注意的是,在超高性能混凝土(UHPC)應用中,需配套2000kN級以上試驗機并改進端面處理工藝,某200米跨度人行懸索橋項目據此實現了178MPa的特種混凝土強度精準檢測。
4. 質量保障與技術創新
實驗室需建立ISO/IEC 17025:2017兼容的管理體系,關鍵控制點包括:溫濕度聯鎖監控系統(養護室20±2℃、RH≥95%)、力值溯源鏈(每半年進行測力環檢定)、數據完整性保障(三級審核+電子簽名)。新興技術方面,基于機器視覺的試件裂紋自動識別系統可將破壞形態判定效率提升300%,而嵌入式壓力傳感芯片實現了澆筑現場實時強度監測。某特級檢測機構引入AI強度預測模型后,28天強度預測準確率達92.3%。
5. 行業發展建議與展望
建議從三方面推進技術創新:一是開發適用于3D打印混凝土的非接觸式強度檢測方法,二是建立基于BIM的強度數據全生命周期管理系統,三是制定納米混凝土等新材料的專用檢測規程。據中國建筑科學研究院預測,到2025年智能檢測設備的市場滲透率將達45%,推動檢測成本降低30%以上。行業亟需構建"標準試件-數字孿生-實體結構"的多維驗證體系,為智能建造時代提供更精準的強度數據支撐。

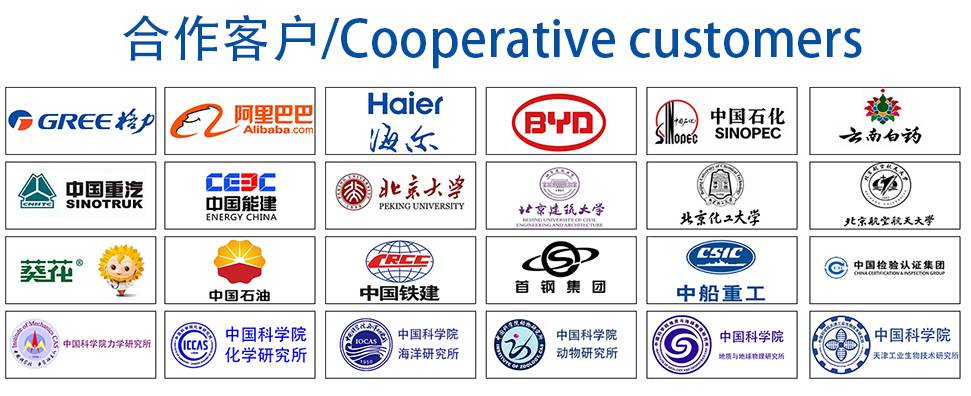