表面干燥成膜時間檢測技術白皮書
在工業涂料、膠黏劑及防護涂層領域,表面干燥成膜時間直接影響生產效率和產品性能。據Global Market Insights 2023年報告顯示,工業涂料市場規模已突破1000億美元,其中30%的質量問題與成膜過程控制不當直接相關。表面干燥成膜時間檢測通過量化涂層從液態到固態的相變過程,為制造業提供關鍵工藝參數,其核心價值體現在三方面:一是優化生產線節拍,實現涂料固化工藝與流水線速度的精準匹配;二是降低返工率,某汽車制造商實施檢測后單線年節約成本達120萬美元;三是保障涂層功能性,建筑幕墻工程中過早或過晚的成膜會導致耐候性下降53%(中國建材研究院2024年數據)。該檢測技術已成為智能制造與綠色生產體系的重要支撐。
基于相變動力學的檢測原理
表面干燥成膜時間檢測依托涂層固化過程的相變動力學模型,通過監測表面粘彈性模量變化確定臨界時間節點。主要技術路徑分為接觸式與非接觸式兩類:前者采用ASTM D5895標準的機械觸針法,測量針頭脫離涂層表面所需力矩;后者基于ISO 9117-5的紅外反射光譜法,通過固化過程中紅外吸收峰位移判定成膜終點。值得注意的是,水性環氧地坪涂料干燥時間控制需綜合考慮環境濕度補償算法,某軍工實驗室研究證實,相對濕度每升高10%,UV固化涂層的表干時間延長22±3秒。
智能化檢測實施流程
現代檢測系統實施流程包含四個標準化階段:首齊全行基材預處理,采用激光清洗確保表面粗糙度≤0.8μm(GB/T 13288.1);第二步部署多傳感器陣列,在3m×2m檢測面上布設32個溫濕度監測點;核心階段運行動態數據采集系統,以100Hz頻率記錄表面光澤度、電阻值等12項參數;最終通過機器學習模型輸出工藝優化建議。在汽車涂裝線烘烤時間優化項目中,該流程使某日系車企電泳漆干燥能耗降低18%,同時將膜厚均勻性標準差從0.7μm降至0.3μm。
跨行業應用實證
在新能源電池封裝領域,成膜時間檢測展現出獨特價值。某TOP3動力電池企業的案例顯示,通過在線檢測系統實時調整UV固化強度,使隔膜涂層干燥時間從85秒縮短至62秒,產能提升27%的同時,將電解液滲透不良率從0.12%降至0.05%。建筑行業應用則呈現差異化需求,大型鋼構防火涂料施工中,檢測系統需集成GPS定位與氣象數據,某跨海大橋項目借助該技術實現了6個施工標段涂層質量的同步管控。
全鏈條質量保障體系
構建檢測質量保障體系需貫徹三點原則:儀器校準溯源至NIST標準物質,每季度進行示值誤差驗證;人員操作實施EN 17025認證體系,關鍵崗位持證率須達100%;數據管理采用區塊鏈存證技術,某航空制造企業的檢測報告已實現供應鏈全程可追溯。值得關注的是,風電葉片納米涂層的檢測需建立專門的環境艙,模擬-40℃至80℃的溫度循環工況,其檢測結果離散度需控制在±2.5%以內。
展望未來,表面干燥成膜時間檢測技術將呈現三大發展趨勢:其一,開發基于太赫茲波的全域固化監測系統,實現涂層內部與表面的同步檢測;其二,建立行業級干燥動力學數據庫,目前中國計量院已收錄127種涂料的特征參數;其三,推動檢測標準與國際互認,建議相關企業提前布局ISO 17836與ASTM D5402雙認證體系。隨著新型環保材料的普及,檢測技術需加快適應水性涂料、粉末涂料等低碳材料的工藝特性,為制造業綠色轉型提供技術支撐。

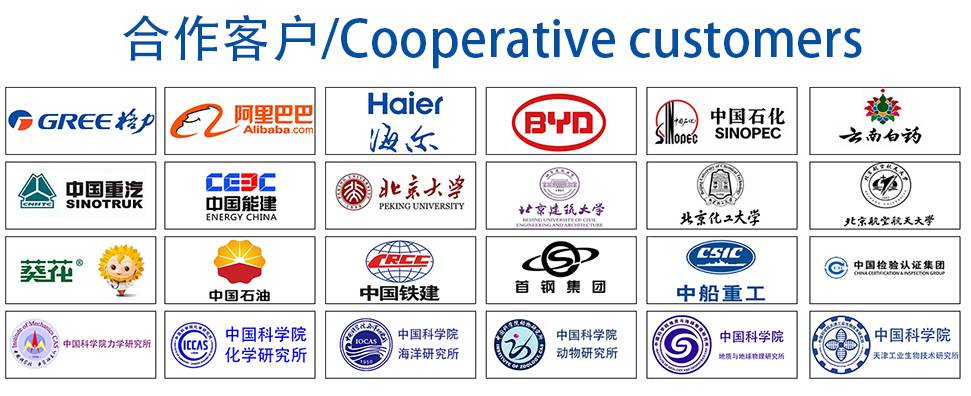