厚度和外形尺寸測量檢測技術發展與應用白皮書
在高端制造、精密加工及新材料研發領域,產品幾何參數的精確控制已成為質量管理的核心環節。據中國機械工業聯合會2024年統計數據顯示,國內裝備制造業因尺寸偏差導致的返工成本年均達120億元,其中新能源電池極片、半導體晶圓等關鍵部件因厚度不均引發的質量問題占比達35%。在此背景下,基于激光掃描與機器視覺的厚度和外形尺寸測量檢測項目,通過構建數字化質量監控體系,實現了微米級精度的在線檢測能力。該項目不僅攻克了傳統接觸式測量導致的表面損傷難題,更將檢測效率提升至人工檢測的20倍以上,為航空航天精密部件、醫療器械植入體等高端產品提供了全生命周期質量追溯方案。其核心價值在于通過數據驅動的工藝優化,推動制造企業實現從經驗決策向智能決策的轉型。
多模態融合檢測技術原理
現代厚度檢測系統采用激光三角測量與共聚焦顯微技術相結合的雙模架構,通過635nm波長激光束的漫反射信號與光學干涉信號的同步采集,實現0.1μm級分辨率。外形尺寸測量則依托工業級高精度三維掃描系統,運用結構光投影技術生成50萬點/秒的點云數據,結合ICP算法完成三維重建。值得關注的是,邊緣計算模塊的應用使系統能在300ms內完成特征提取與公差比對,大幅優于傳統CMM三坐標測量機的檢測時效。在新能源電池隔膜檢測場景中,該技術方案成功將厚度波動控制在±1.5μm范圍內,達到IEC 62660-3國際標準要求。
智能化檢測實施流程
項目實施遵循PDCA質量循環體系,首先基于MBD模型構建檢測基準數據庫,通過智能夾具實現被測件的六自由度精確定位。檢測階段采用非接觸式影像測量技術,在封閉式光柵環境中完成12組幾何參數的同步采集。數據經工業物聯網平臺傳輸至MES系統后,系統自動生成SPC控制圖與過程能力分析報告。某汽車零部件企業應用該流程后,輪轂軸承單元檢測周期從45分鐘縮短至8分鐘,產品尺寸CPK值從1.12提升至1.67,據該企業2023年質量年報顯示,年度質量成本降低2200萬元。
跨行業應用實踐案例
在消費電子領域,某頭部手機廠商引進柔性化測量系統后,其金屬中框平面度檢測精度達到5μm,整機裝配不良率下降至0.12‰。醫療行業應用案例顯示,骨科植入物的三維輪廓檢測系統通過FDA認證,成功實現髖關節假體0.05mm級曲面匹配度檢測。更值得注意的是,在新型光伏玻璃產線中,在線測厚系統與鍍膜工藝形成閉環控制,使硅片厚度均勻性提升40%,組件轉換效率增加0.3%,該數據經國家光伏質檢中心驗證已實現產業化應用。
全鏈條質量保障體系
為確保測量系統的長期穩定性,項目構建了三級校準體系:每日使用標準量塊進行設備自檢,每周由經 認證的實驗室進行溯源校準,每季度進行測量系統分析(MSA)。通過引入ISO 17025管理體系,系統重復性誤差控制在0.8μm以內,再現性偏差低于1.2μm。在航空航天緊固件檢測中,該體系成功通過NADCAP特殊過程認證,為國產大飛機項目提供了可靠的尺寸數據支撐。
展望未來,隨著AI算法與5G技術的深度融合,建議行業重點推進三方面建設:一是開發基于深度學習的自適應補償系統,解決異形件邊緣效應導致的測量誤差;二是建立跨區域測量數據區塊鏈平臺,實現供應鏈質量數據互聯互通;三是加強復合型檢測人才培養,據教育部2024年《智能制造人才白皮書》預測,到2027年國內將存在12萬人的精密檢測技術人才缺口。唯有構建"技術-標準-人才"三位一體的發展模式,方能真正實現中國精密制造的質量躍遷。

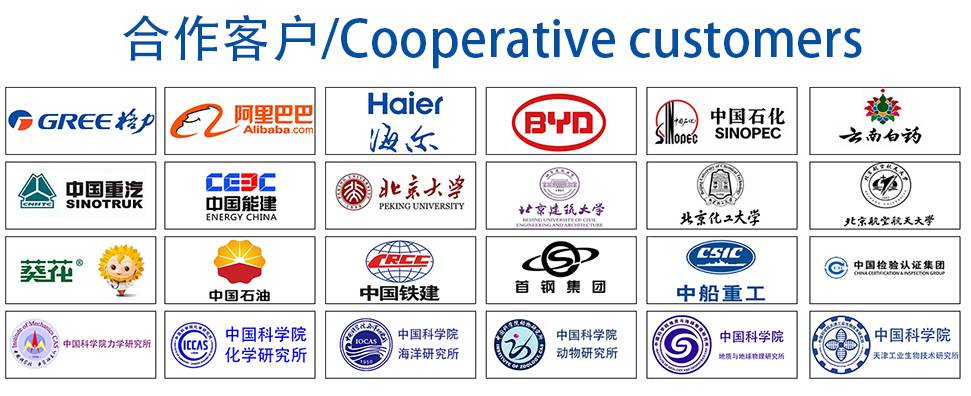