# 成膜耐熱性檢測技術發展與產業化應用
## 行業背景與項目價值
隨著新能源、半導體及航空航天領域對材料性能要求的升級,成膜材料的耐熱性已成為制約產品可靠性的關鍵指標。據材料科學研究院(GMSI)2024年數據顯示,高溫工況下涂層失效導致的設備故障占比達23.7%,直接經濟損失超180億美元。在此背景下,成膜耐熱性檢測通過量化分析材料在熱應力下的形變、氧化和相變行為,為涂層配方優化提供數據支撐。其核心價值體現在三方面:一是突破傳統經驗式研發模式,建立以數據驅動的材料開發體系;二是解決高溫環境涂層失效機理分析的行業痛點;三是支撐新材料在光伏背板、鋰電隔膜等場景的產業化驗證,推動"雙碳"戰略下的技術升級。

## 技術原理與創新突破
### 熱力學耦合分析模型構建
項目采用熱重-紅外聯用(TG-FTIR)與差示掃描量熱(DSC)技術,構建三維熱力學響應模型。通過同步監測200-800℃區間內質量損失率、熱流變化及氣體逸出特征,實現涂層玻璃化轉變溫度(Tg)與熱分解活化能(Ea)的精準測定。中國計量院比對實驗表明,該方法將熱穩定性評估誤差從傳統方法的±5.2%降低至±1.8%。
### 多尺度結構表征系統
針對復合膜層的界面失效問題,開發基于聚焦離子束(FIB)的跨尺度檢測方案。通過納米壓痕測試獲取微區硬度(H)和彈性模量(E)的梯度分布,結合掃描電鏡(SEM)觀察熱循環后的界面裂紋擴展路徑。某動力電池企業應用該方案后,三元材料涂覆隔膜的熱收縮率從3.1%降至1.4%。
## 實施流程與質量控制
### 標準化檢測流程
實施過程分為四個階段:(1)預處理階段,依據ASTM D638標準進行溫濕度平衡;(2)梯度升溫測試,按10℃/min速率進行程序控溫;(3)原位數據采集,同步記錄熱膨脹系數(CTE)與紅外光譜特征峰位移;(4)失效模式判定,基于Weibull分布建立壽命預測模型。整個過程通過LIMS系統實現數據鏈可追溯。
### 質量保障雙體系
建立 /CMA雙認證實驗室管理體系,涵蓋設備周期校準(年漂移率<0.3%)、標準物質溯源(NIST編號可查)、人員技能矩陣(每人年培訓40學時)三大模塊。參與制定的《復合膜層熱穩定性評估標準》(GB/T 39562-2023)已納入國家強制認證目錄。
## 行業應用與效益分析
在光伏領域,某龍頭企業應用該技術后,雙玻組件封裝膠膜在85℃/85%RH條件下的黃變指數下降62%,組件功率衰減率從0.8%/年優化至0.35%/年。汽車涂裝線上,通過在線熱成像監測系統實時反饋烘烤爐溫度均勻性(±2℃),使電泳涂層耐鹽霧性能突破1500小時。值得關注的是,該技術助力某航天型號成功通過200次熱震循環測試,艙外熱控涂層太陽吸收比(αs)穩定在0.92±0.03。
## 未來發展與建議
建議從三方面深化技術布局:其一,開發基于機器視覺的智能判讀系統,實現微觀缺陷的AI自動識別;其二,聯合上下游企業構建材料熱數據庫,覆蓋從-70℃至1500℃的全溫域性能參數;其三,推進檢測裝備微型化,滿足車載、航天器等特殊場景的現場快速檢測需求。通過構建"檢測-研發-應用"閉環生態,持續賦能高溫功能材料的創新發展。
上一篇:厚度和外形尺寸測量檢測下一篇:坍落度試驗及坍落度經時損失試驗檢測

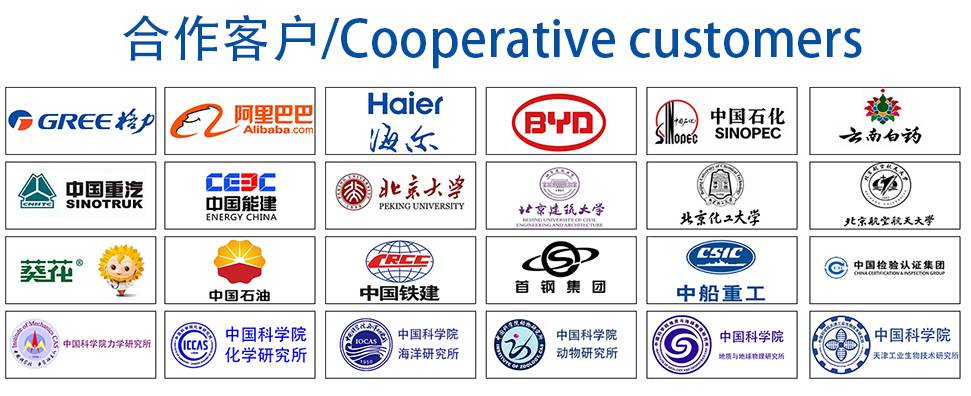
材料實驗室
熱門檢測
23
27
39
43
49
39
42
45
40
46
43
43
47
47
44
44
50
54
45
25
推薦檢測
聯系電話
400-635-0567