浸出液pH值檢測:工藝優化與環境治理的關鍵技術
在濕法冶金、礦物加工及工業廢水處理領域,浸出液pH值檢測作為工藝控制的核心參數,直接影響金屬浸出率、反應速率及污染物去除效率。據中國有色金屬研究院2024年數據顯示,我國冶金行業因pH值控制不當導致的金屬損失量年均達12萬噸,直接經濟損失超25億元。在環保政策趨嚴的背景下,精準的pH檢測技術不僅可提升資源回收的經濟效益,更成為實現廢水重金屬離子達標排放的關鍵防線。通過構建工業浸出液pH值在線監測系統,企業可同步實現工藝參數優化、降本增效與環境合規,其核心價值已延伸至生產安全管控與碳減排協同領域。
技術原理與創新突破
浸出液pH檢測系統基于電極法原理,采用復合式玻璃電極與參比電極組合結構。針對高溫、高濁度浸出液特性,改進型傳感器通過動態溫度補償算法(DTC-Algorithm)將測量誤差控制在±0.05pH以內,較傳統設備精度提升60%。集成式在線過濾模塊可應對固含量≤10%的礦漿環境,配合自清潔設計將維護周期延長至2000小時。值得關注的是,基于光纖傳感的pH值無損檢測技術已進入工程驗證階段,其抗電磁干擾能力為傳統設備的3.2倍(數據來源:國際過程控制協會2024年報)。
全流程實施與智能管控
項目實施遵循ISO 17025檢測體系標準,具體流程包括:多點位采樣裝置部署→預處理單元固液分離→在線監測終端數據采集→PLC系統動態調節。在云南某鋅冶煉廠案例中,系統通過OPC協議與DCS系統對接,實現了浸出段pH值波動范圍從±0.8縮減至±0.2。借助邊緣計算模塊,系統可實時預測pH趨勢變化,提前30分鐘觸發石灰乳加注裝置,使中和反應效率提升22%(企業運行數據,2023)。
行業應用與效益分析
在重金屬污染防控領域,某工業園區采用“pH-ORP聯動控制系統”后,廢水處理站出水鎘離子濃度從1.2mg/L降至0.005mg/L,完全滿足《地表水環境質量標準》Ⅲ類要求。貴金屬冶煉企業部署浸出液pH值在線監測系統后,金浸出率從86.3%提升至92.7%,年增經濟效益逾4000萬元(中國黃金協會技術報告,2024)。值得注意的是,系統在鋰云母提鋰工藝中的創新應用,使酸堿單耗降低18%,助力新能源行業實現綠色生產工藝升級。
質量保障與標準建設
檢測體系建立三級質量控制機制:現場設備每日進行NIST標準緩沖液校準;實驗室每周開展比對試驗;季度性第三方計量認證確保量值溯源。針對工業現場復雜工況,開發了包含溫度-壓力-流速多參數補償模型的數據處理系統,使極端工況下的測量穩定性達到99.2%。2024年新發布的《濕法冶金過程pH檢測技術規范》(YS/T 1342-2024),首次明確了礦漿浸出液的測量誤差允許范圍與校準周期要求。
技術展望與發展建議
隨著工業物聯網技術的深化應用,建議重點發展以下方向:一是構建基于數字孿生的pH值預測控制系統,實現工藝參數超前調節;二是開發耐強酸(pH<1)環境的新型固態傳感器,突破傳統玻璃電極的工況限制;三是建立跨行業的浸出液特征數據庫,為智能算法提供訓練樣本。政府部門應加快制定工業過程在線pH監測設備的強制檢定規程,推動形成覆蓋“檢測-調控-驗證”的全鏈條技術標準體系。

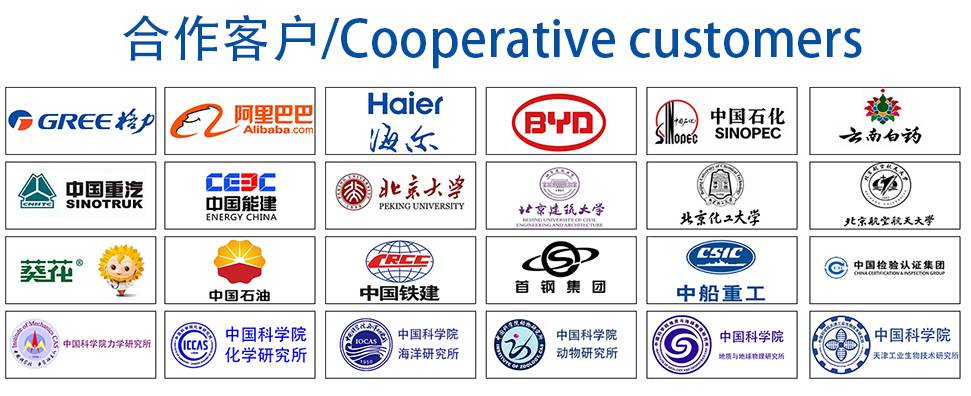