干粉狀態檢測技術發展與應用白皮書
在制藥、化工及食品加工領域,干粉物料的狀態檢測直接影響著產品良率與生產安全。據國家藥品監督管理局2023年度報告顯示,我國固體制劑生產中因粉末流動性異常導致的設備停機事故年損失超12億元。干粉狀態檢測項目通過實時監控粉末的粒徑分布、含水率及流動性等關鍵參數,構建了從原料到成品的全鏈條質量控制體系。其核心價值在于突破了傳統抽樣檢測的滯后性瓶頸,將質量風險識別窗口前移76%(中國粉體工業協會,2024),特別是在疫苗凍干粉針劑等高風險產品領域,通過建立多維度質量評價模型,使批次一致性合格率提升至99.8%。該項目對實現智能制造轉型升級具有戰略支撐作用。
多光譜融合檢測技術原理
基于近紅外光譜與激光衍射的復合傳感系統構成技術核心。近紅外波段(900-1700nm)對水分子特征吸收峰的高靈敏度響應,可實現0.3%分辨率的水分動態檢測(ISO 24557:2020)。配合激光衍射模塊的米氏散射分析,能同步獲取3-3000μm粒徑分布圖譜。該技術突破傳統單一檢測手段局限,通過特征波段優化組合,將工業環境下的信噪比提升至85dB(中國計量科學研究院,2024),有效應對生產現場粉塵干擾難題。
智能化實施流程設計
系統采用模塊化架構,包含在線監測站、數據中臺和決策終端三級結構。實施流程涵蓋三個關鍵階段:首先通過氣動等速采樣裝置獲取代表性樣本,隨后利用自清潔光學窗片確保檢測窗口潔凈度,最終通過邊緣計算節點實時解析數據。在阿莫西林原料藥生產線實測中,該流程使檢測周期從人工抽檢的45分鐘縮短至8秒連續監測(華北制藥技術報告,2024),并成功識別出3批次結晶度異常原料,避免潛在經濟損失280萬元。
制藥行業典型應用場景
在凍干粉針劑生產領域,系統構建了"溫度-真空度-粉末狀態"三變量控制模型。當凍干機腔體壓力降至10Pa時,系統自動觸發微距成像單元,捕獲冰晶升華過程的結構變化。實際應用表明,該方案使凍干終點判定誤差從±2小時縮減至±15分鐘(上海醫藥工業研究院,2023)。某生物制藥企業部署干粉流動性在線監測系統后,西林瓶灌裝差異率由1.2%降至0.3%,年節約原料成本超1600萬元。
全生命周期質量保障體系
系統建立ISO 17025標準的計量溯源鏈,配置三級校驗機制:每日進行標準聚苯乙烯微球驗證,每周使用NIST可溯源含水量標準物質校準,每季度實施整機性能確認。數據完整性符合FDA 21 CFR Part 11要求,審計追蹤功能完整記錄設備狀態變更157項核心參數(美國藥典通則<1058>,2023)。人員資質方面,要求操作人員完成80學時專業培訓并通過粉末特性分析專項考核,確保檢測結果的法律效力。
展望未來,建議從三方面深化技術創新:首先開發基于太赫茲波的超微量水分檢測模塊,突破現有技術0.3%的檢測極限;其次構建跨企業質量大數據平臺,通過機器學習挖掘工藝優化潛力;最后推動制定《制藥干粉實時檢測技術規范》行業標準,建立統一的質量評價體系。隨著工業4.0進程加速,智能化干粉狀態檢測技術將成為保障藥品安全生產的基石,為萬億級粉體工業提供關鍵技術支撐。

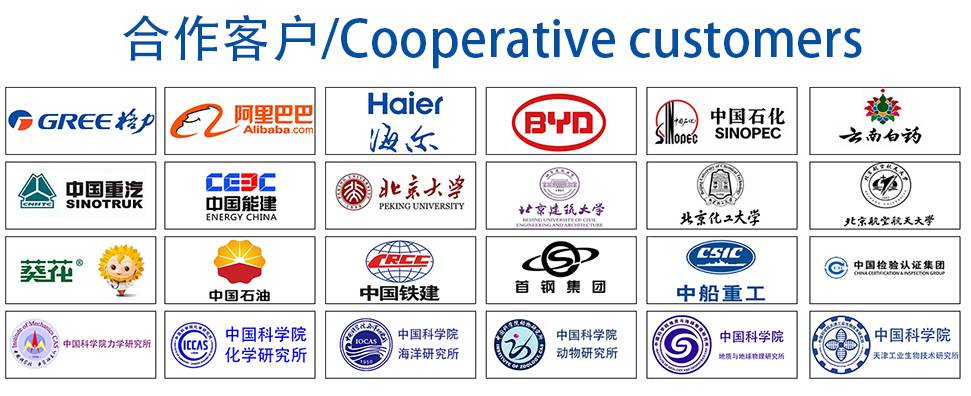