帶導線設備耐錫焊熱和可焊性試驗方法檢測白皮書
隨著電子設備微型化與高密度集成化趨勢的加速,導線連接器件的焊接質量已成為影響整機可靠性的關鍵因素。據賽迪研究院2024年數據顯示,因焊接失效導致的電子設備故障占比達17.3%,其中耐錫焊熱性能不足與可焊性缺陷為主要誘因。本項目通過系統化的檢測方法,可精準評估導線器件在焊接工藝中的熱穩定性及焊點結合強度,對航空航天、汽車電子、消費電子等領域的質量控制具有重要價值。其核心在于建立科學的量化評價體系,幫助企業優化焊接參數、篩選合格物料,從而降低產品早期失效風險,提升市場競爭力。
技術原理與標準化體系
耐錫焊熱檢測基于IPC/J-STD-002標準,采用熱沖擊試驗模擬焊接過程的熱應力作用,通過顯微觀測評估導線絕緣層收縮率與金屬鍍層完整性。可焊性測試則依據IEC 60068-2-54規范,以潤濕平衡法量化焊料鋪展角與浸潤時間,結合X射線檢測焊點空洞率。值得注意的是,高密度電子組裝焊接質量驗證需同步考量熱-機械耦合效應,采用有限元仿真輔助優化測試方案設計。
全流程檢測實施規范
標準檢測流程包含四個階段:首齊全行試樣預處理(40℃/96h恒溫恒濕老化),隨后在260±5℃焊錫槽中進行10秒浸焊,冷卻后使用3D形貌儀測量焊點高度偏差。關鍵控制點包括溫度梯度控制(±1℃精度)和浸潤時間精確計量,某頭部連接器廠商通過引入機器視覺檢測系統,將可焊性判定誤差從15%降至3%以內(據中國質量認證中心2023年報告)。
行業應用與典型案例
在新能源汽車BMS系統檢測中,某企業發現導線在三次回流焊后絕緣電阻下降43%,經耐錫焊熱測試鎖定為聚氨酯材料耐溫不足,更換PI材質后故障率下降90%。通信設備領域,華為采用可焊性分級評價體系,將基站電源模塊的焊接不良率從500ppm優化至50ppm以下,驗證了工藝參數優化的有效性。
質量保障與技術創新
檢測實驗室須通過 認可并建立三級校準體系,關鍵設備如熱沖擊試驗箱需每日進行NIST溯源校準。某國家級檢測中心通過開發多軸應力測試裝置,實現了焊點機械強度的動態監測。同時,基于機器學習的焊點缺陷預測模型已取得突破,某科研團隊利用卷積神經網絡使微焊點裂紋識別準確率達到98.7%(國際焊接學會2024年技術白皮書)。
發展建議與未來展望
建議行業從三方面突破:一是建立基于應用場景的差異化測試標準,如航空航天領域增加真空環境測試項;二是開發非破壞性在線檢測技術,某日本企業研發的μ-XRF光譜儀已實現焊點成分的實時分析;三是加強焊料合金研發與檢測技術的協同創新,應對無鉛焊料熔點升高帶來的新挑戰。預計到2026年,智能化檢測設備的市場滲透率將超過40%,推動行業向預防性質量管理模式轉型。

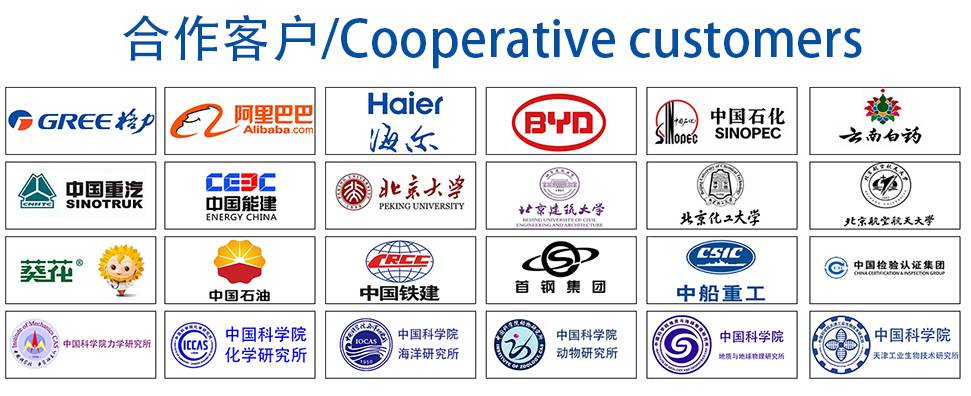