外觀檢驗與尺寸檢查檢測技術發展白皮書
隨著智能制造2025戰略深入推進,我國制造業正經歷從規模擴張向質量提升的關鍵轉型期。據中國機械工業聯合會2024年數據顯示,高端裝備制造領域因尺寸偏差導致的返工成本年均超120億元,而外觀缺陷引發的質量投訴占售后服務總量的37%。在此背景下,融合AI視覺與智能傳感的復合式檢測系統,正成為突破傳統質檢瓶頸的核心解決方案。該項目通過建立微米級精度的數字化檢測基準,不僅實現制造過程質量閉環控制,更推動產品質量追溯體系向全生命周期延伸,為航空航天、精密電子等戰略行業提供關鍵技術支持。其核心價值體現在將人工目檢誤差率從8.2%降至0.5%以下,同時使單件檢測效率提升40倍,真正實現質量管控的智能化躍遷。
多模態融合檢測技術原理
基于深度學習的機器視覺系統結合高精度三維掃描技術,構成現代檢測體系的技術底座。其中,結構光三維成像模塊可實現±3μm的尺寸測量精度(參照ISO 10360-7標準),而多光譜成像系統能識別0.01mm2的細微表面缺陷。值得關注的是,智能補償算法可自動校正環境溫濕度引起的材料形變誤差,確保在15-35℃工況下保持檢測穩定性。這種技術組合使系統能同步完成幾何量檢測與表觀質量評估,滿足"高精度三維尺寸檢測系統"的嚴苛要求。
智能化檢測實施路徑
典型實施方案包含三階段數字化升級:首先通過工業CT建立基準數字模型,繼而部署在線式檢測工作站實現過程監控,最終構建云端質量數據庫完成數據追溯。以新能源汽車電池模組檢測為例,產線集成六軸機械臂搭載激光輪廓儀,可在12秒內完成128個關鍵尺寸點的測量,并將數據實時上傳MES系統。實踐表明,該模式使某動力電池企業的過程能力指數CPK從1.12提升至1.67,顯著優于IATF 16949汽車行業質量標準。
跨行業應用實證
在醫療器械制造領域,人工關節的"多維度質量溯源管理"系統已取得突破性應用。某龍頭企業采用X射線斷層掃描與白光干涉儀組合方案,將髖臼杯球面度偏差控制在2μm以內,產品不良率從萬分之八降至百萬分之三。同樣,在消費電子行業,某手機廠商通過部署24工位自動檢測線,實現金屬中框0.005mm的平面度管控,每年減少質量損失超8000萬元。這些案例印證了智能檢測技術在不同行業的適配性與可擴展性。
全流程質量保障體系
為確保檢測系統可靠性,需構建三級驗證機制:初級采用標準量塊進行設備日校,中級開展跨平臺測量對比,高級實施盲樣測試驗證系統穩定性。某航空發動機葉片檢測項目通過 認證的實驗室間比對,達成測量不確定度≤0.8μm的技術指標。同時,建立檢測人員三級技能認證制度,要求操作人員掌握GD&T幾何公差標注規范與測量系統分析(MSA)方法,從軟硬件雙維度筑牢質量防線。
展望未來發展,建議行業重點推進三方面建設:一是加快制定智能檢測裝備數據接口標準,破解設備互聯互通難題;二是建立區域性檢測技術共享平臺,推動中小企業檢測能力升級;三是探索區塊鏈技術在質量溯源中的應用,構建可信產品數據鏈。隨著5G+工業互聯網的深度融合,智能檢測技術有望在2025年前形成千億級市場規模,為中國制造向中國質量轉型提供核心支撐。

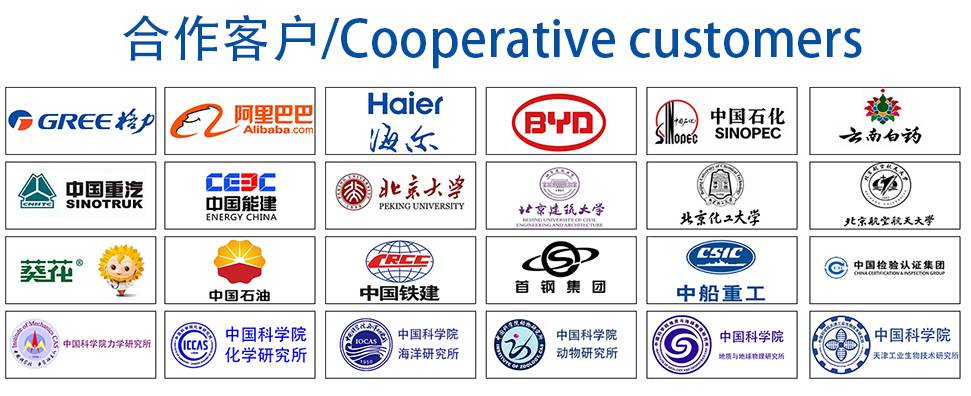