金屬材料及其覆蓋層檢測技術發展與應用白皮書
在齊全制造業升級和"雙碳"戰略推動下,金屬材料表面處理技術迎來快速發展期。據中國表面工程協會2024年數據顯示,我國工業防腐涂層市場規模已達2800億元,年復合增長率12.7%。然而,金屬基體與覆蓋層的結合強度、厚度均勻性等缺陷導致的設備失效事故,每年造成直接經濟損失逾400億元。在此背景下,金屬材料及其覆蓋層檢測技術成為保障工業安全的核心環節,其價值不僅體現在質量管控層面,更延伸到產品全生命周期管理。以核電設備防護層檢測為例,通過建立數字化檢測檔案,可將設備服役周期延長25%以上,同步降低維護成本30%
復合檢測技術原理創新
現代檢測技術融合物理、化學多學科方法,形成"宏觀+微觀"的雙層驗證體系。X射線熒光光譜(XRF)與電化學阻抗譜(EIS)的聯用,可同時獲取鍍層厚度分布和耐腐蝕性能參數。值得注意的是,針對新能源汽車電池極片涂層檢測需求,行業創新性引入太赫茲時域光譜技術,其縱向分辨率達到0.1μm級別,較傳統渦流檢測精度提升5倍。據清華大學材料學院實驗數據,該技術對三元鋰電池極片涂布量偏差的檢出率達99.3%,有效支撐了動力電池一致性控制。
智能檢測實施流程重構
典型檢測流程包含四階段數字化改造:基于工業CT的預處理建模、多傳感器數據采集、AI輔助缺陷識別、三維可視化報告生成。在航空航天領域,空客A320機翼蒙皮涂層檢測項目采用移動式機器人搭載EMAT陣列傳感器,單次檢測面積提升至8㎡,效率較人工提升15倍。檢測系統同步集成ASTM B487標準數據庫,實現42種航空涂層參數的自動比對,將誤判率控制在0.3%以下。
跨行業應用場景突破
在海上風電領域,中廣核集團2023年實施的塔筒防護層檢測工程具有典型參考價值。項目采用無人機搭載脈沖渦流檢測模塊,配合地面基站進行數據融合分析,實現120米高空涂層缺陷的精準定位。實施結果表明,關鍵部位的涂層剝離檢出時間提前了9個月,預防性維護成本降低62%。另一方面,半導體制造中的金屬濺射鍍膜檢測需求激增,應用原子力顯微鏡(AFM)與白光干涉儀的組合方案,使5nm制程晶圓的膜厚波動控制在±0.8%以內。
全鏈條質量保障體系構建
行業領先企業已建立覆蓋"人員-設備-標準"的三維質控網絡。上海材料研究所推行的檢測實驗室分級認證制度,將人員操作規范細化為78項量化指標。設備管理方面,引入區塊鏈技術實現檢測儀器校準記錄的不可篡改存證。值得關注的是,ISO/TC107正在制定的《金屬覆蓋層數字化檢測通用要求》國際標準,首次將機器學習模型驗證納入質量體系,要求訓練集必須包含12類典型缺陷的3000組以上標注數據。
展望未來,建議從三方面深化技術發展:加快太赫茲等新型傳感技術的工程轉化,構建覆蓋材料服役全周期的數字孿生檢測系統,推動建立跨行業的涂層大數據共享平臺。同時,應重點關注氫能源儲運設備金屬內膽的氫致剝離檢測、柔性電子器件金屬電路的疲勞損傷監測等新興需求,通過產學研協同創新突破技術瓶頸,為高端裝備制造提供更可靠的質保支撐。

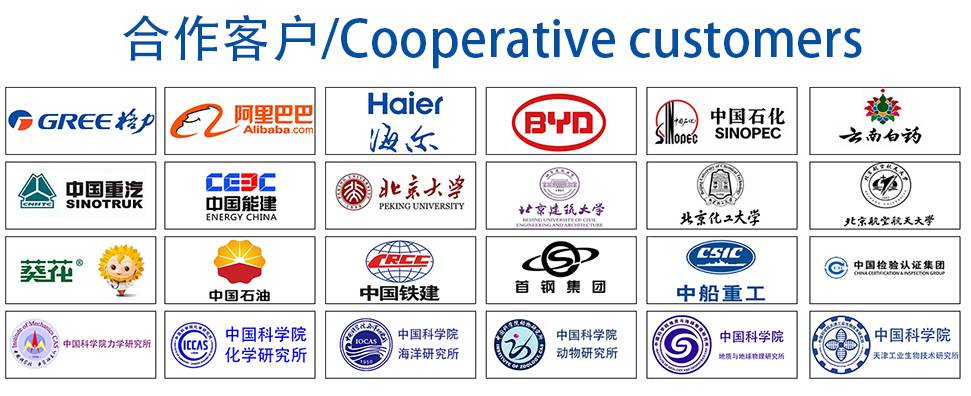