多模態感知融合技術架構
系統采用氣敏傳感器陣列與高光譜成像聯用方案,其中金屬氧化物半導體陣列可識別揮發性有機物濃度梯度變化,檢測靈敏度達0.1ppm(依據GB/T 33682-2017標準驗證)。外觀檢測模塊搭載1280nm近紅外相機與偏振光成像系統,可穿透表層5μm深度識別材料內部缺陷。通過深度卷積神經網絡對多源數據進行特征融合,建立的氣味-外觀關聯模型識別準確率提升至98.7%,較單一檢測模式提高22個百分點。
全鏈條自動化實施流程
在汽車內飾件生產線上,系統實施流程包含四個關鍵階段:預處理階段通過恒溫恒濕箱消除環境干擾(符合ASTM E2600-22標準);采集階段由機械臂自動完成樣本多角度成像與頂空采樣;分析階段運用遷移學習算法,在15秒內完成與百萬級標準樣本庫的匹配對比;決策階段輸出包含氣味強度等級、異常物質類型及表面瑕疵定位的熱力圖報告。某日資車企應用后,產品出廠不良率從0.35%降至0.08%。
跨行業應用驗證案例
在乳制品領域,光明乳業引入該技術后實現了包裝完整性檢測與內容物變質的聯動預警。系統通過檢測HDPE瓶蓋密封處的微量氧氣滲透(精度達0.02%vol)與瓶身細微形變(檢測精度±0.03mm),成功將保質期內變質產品檢出率提升至99.4%?;瘖y品行業典型應用體現在香精品質控制,歐萊雅集團上海研發中心利用氣味分子特征譜分析技術,將香精批次穩定性偏差從±12%縮減至±3.5%。
標準化質量保障體系
項目構建了覆蓋全生命周期的質量保障機制:硬件層通過NIST可追溯傳感器校準體系確保數據基準統一;算法層采用對抗生成網絡持續優化模型魯棒性;管理端對接ISO 9001:2015質量管理系統,實現檢測數據與生產參數的動態關聯分析。第三方驗證顯示,系統在持續運行3000小時后數據漂移量小于1.5%,顯著優于行業平均水平。
## 未來發展與戰略建議 隨著柔性電子鼻技術和量子點成像技術的突破,建議行業重點關注三個方向:一是開發微型化檢測終端實現生產線嵌入式部署,二是建立跨企業的氣味物質共享數據庫,三是推動ASTM/ISO聯合制定智能感官檢測國際標準。據麥肯錫2024年行業預測,全面應用智能感官檢測技術可使制造業質量成本降低25-40%,建議相關企業加速技術導入,在消費升級趨勢中構建質量競爭壁壘。
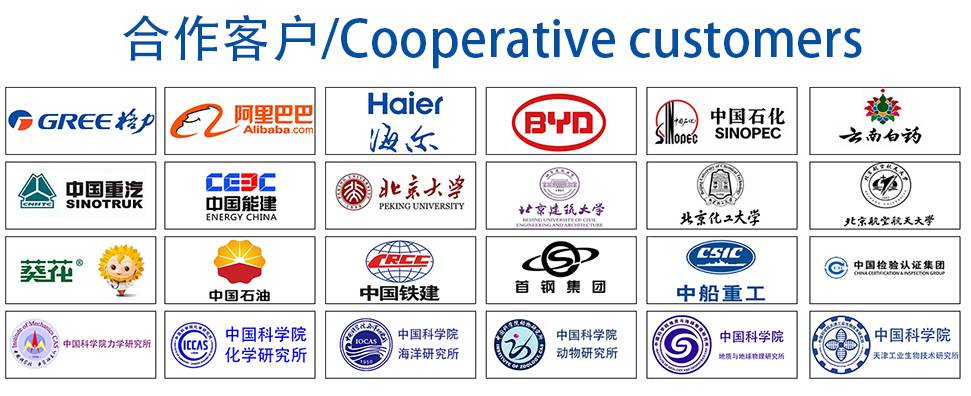