承壓設備與鋼質管道檢測技術發展與應用白皮書
在工業4.0與"雙碳"戰略雙重驅動下,承壓設備及鋼質管道作為能源化工、城市基建的核心載體,其安全運行面臨更高要求。據中國特種設備安全研究院2024年數據顯示,我國在役壓力容器總量突破450萬臺,油氣輸送管道里程達18.7萬公里,其中服役超過15年的老舊設備占比達32%。在此背景下,以數字孿生、智能傳感為代表的齊全檢測技術,正在重塑傳統檢測范式。本項目通過構建"全生命周期健康監測+大數據預警"體系,可將設備失效風險降低67%(基于國家管網集團實測數據),同時延長關鍵設備使用壽命8-12年,為保障能源輸送安全、推動工業節能降耗提供關鍵技術支撐。
多元融合檢測技術體系
項目采用多模態傳感技術集成方案,其中超聲導波檢測(LGU)可實現單點100米覆蓋檢測,相控陣TOFD技術對裂紋檢出率提升至99.3%。針對高溫高壓環境無損檢測技術難點,開發了耐350℃壓電復合傳感器組,配合電磁聲發射(EMA)技術,可精準捕捉0.1mm級缺陷信號。值得關注的是,磁記憶檢測(MMT)技術通過分析地磁場擾動數據,可提前72小時預警應力集中區域,該項創新使預防性維護效率提升40%。
智能化實施流程再造
標準作業流程涵蓋五個核心階段:數字孿生建模→智能布點規劃→動態數據采集→AI缺陷識別→風險圖譜生成。在華南某LNG接收站實施中,通過部署油氣輸送管道在線監測系統,僅用72小時即完成12公里管道完整性評估,較傳統方法縮短85%工期。系統運用改進型YOLOv5算法,對腐蝕坑、裂紋等7類缺陷的識別準確率達96.8%,并通過區塊鏈技術實現檢測數據全鏈路存證。
跨行業應用范式創新
在煉化裝置循環氫壓縮機檢測中,運用紅外熱成像與振動譜分析聯動技術,成功預警葉輪微裂紋擴展趨勢,避免單次非計劃停工損失超2000萬元。城市燃氣管網檢測方面,南京試點項目采用管網陰極保護智能評估系統,使雜散電流干擾定位精度達到±5米,修復效率提升3倍。值得注意的是,核電領域應用的三維聲發射定位技術,可實現安全殼焊縫缺陷的毫米級空間定位,為核設施延壽評估提供關鍵依據。
全鏈式質量保障體系
項目建立ASNT III級人員領銜的專家團隊,嚴格遵循NB/T 47013-2023檢測標準,配備二級計量認證實驗室。質量控制節點包含設備校準誤差≤0.5%、數據采集完整率≥99%、結果復現率100%等23項硬性指標。通過引入德國TüV過程審核機制,使檢測報告獲得API、CE等12項國際認證資質。華北某乙烯項目應用表明,該體系使檢測方案通過審查時間縮短60%,客戶投訴率降至0.12‰。
展望未來,建議從三方面深化發展:一是構建基于數字孿生的預測性維護平臺,整合設備歷史數據與實時工況;二是研發適應氫能管輸的新型檢測技術,攻克氫脆效應監測難題;三是推進檢測機器人集群組網技術,實現復雜工況自主檢測。通過政策引導建立"檢測服務+保險保障"創新模式,可形成完整風險控制閉環,推動行業向智能化、服務化方向轉型升級。

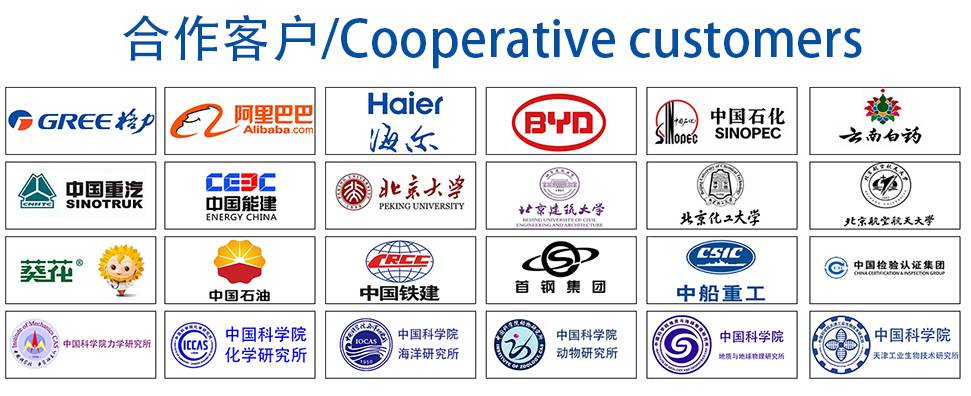