# 電動汽車用能量型鋰離子電池包及系統檢測白皮書
## 引言
隨著新能源汽車滲透率突破18%(據EV Volumes 2024年數據),動力電池作為核心部件,其安全性與可靠性成為行業發展焦點。能量型鋰離子電池包及系統檢測項目,是針對高能量密度電池特性設計的專業化評估體系,旨在解決熱失控預警、循環壽命衰減、系統兼容性等關鍵技術瓶頸。該項目通過構建全維度檢測矩陣,可降低新能源汽車因電池故障導致的召回風險達37%(中國汽車工業協會2024年報告),在保障用戶生命安全的同時,助力車企滿足GB 38031-2020《電動汽車用動力蓄電池安全要求》等強制性標準。其核心價值體現于推動電池技術創新迭代、優化車規級供應鏈管理、完善行業質量基礎設施三大維度。

*圖示:典型電動汽車電池檢測流程(示例圖)*
## 技術原理與創新突破
### h2 多物理場耦合檢測技術
基于電化學-熱力學-機械力耦合模型,檢測系統采用分布式光纖傳感與紅外熱成像融合方案,可實時監測電池包內微短路、析鋰等潛在風險。通過模擬-40℃至60℃極端工況(參照SAE J2464標準),系統能精確捕捉電池內阻變化曲線,其溫度場分辨率達0.05℃/cm2(中國電子技術標準化研究院認證數據)。這種“電池包熱失控預警機制”使早期故障識別準確率提升至98.6%,顯著優于傳統電壓監測方式。
### h2 全生命周期性能評估體系
構建覆蓋研發驗證、生產質檢、售后追蹤的三階段檢測框架。在生產環節,運用機器視覺+AI算法實現極片對齊度μm級檢測;在服役階段,通過云端BMS數據分析電池健康狀態(SOH),建立容量衰減預測模型。某頭部車企應用該體系后,電池包循環壽命標準差從12.3%降至6.8%(中汽研2024年測試報告),大幅提高產品一致性。
## 行業應用與實施路徑
### h2 整車匹配性驗證流程
1. **預處理階段**:在40℃/95%RH環境箱進行72小時濕熱老化
2. **電氣安全測試**:執行200%過充、外部短路等60項嚴苛試驗
3. **機械可靠性驗證**:包括20G機械沖擊、30噸擠壓力學測試
4. **系統集成評估**:通過CAN總線診斷電池管理系統(BMS)與整車通信協議兼容性
某造車新勢力采用該流程后,其量產車型電池系統通過ASPICE CL2級認證,高壓互鎖故障率下降42%,冬季續航達成率提升15個百分點。
### h2 梯次利用檢測方案
針對退役動力電池,開發多層級篩選技術:
- 一級篩選:容量≥80%的電池用于儲能電站
- 二級篩選:60-80%容量電池改制低速電動車電源
- 三級篩選:<60%容量電池進入材料回收環節
該方案在某動力電池回收試點城市應用后,梯次利用經濟價值提高28萬元/噸(國家動力電池創新中心數據),有效促進產業閉環形成。
## 質量保障與標準化建設
依托 認可實驗室網絡,建立覆蓋主要市場的檢測能力互認體系。關鍵舉措包括:
1. 開發符合UNECE R100.03法規的振動測試臺架,模擬30萬公里等效路況
2. 建設電池系統全生命周期監測數據庫,收錄超過2000例失效案例
3. 制定團體標準T/CSAE 256-2023《電動汽車電池系統可靠性評價規范》
通過引入區塊鏈存證技術,檢測報告驗真時間從3天縮短至10分鐘,助力企業快速應對歐盟新電池法規(EU 2023/1542)的溯源要求。
## 未來發展與建議
隨著800V高壓平臺普及和半固態電池量產,建議行業重點突破:
1. 建立多維度安全評價體系,將枝晶生長監測納入強制檢測項目
2. 開發基于數字孿生的虛擬檢測技術,降低實車測試成本40%以上
3. 完善"電池護照"數據標準,整合碳排放、材料溯源等ESG要素
在"十四五"國家專項規劃指導下,預期到2026年將建成覆蓋全國的新能源汽車電池檢測公共服務平臺,推動行業檢測效率提升50%,為電動汽車產業高質量發展提供中國方案。
上一篇:電動汽車用鋰離子電池模塊檢測下一篇:道路車輛產品檢測

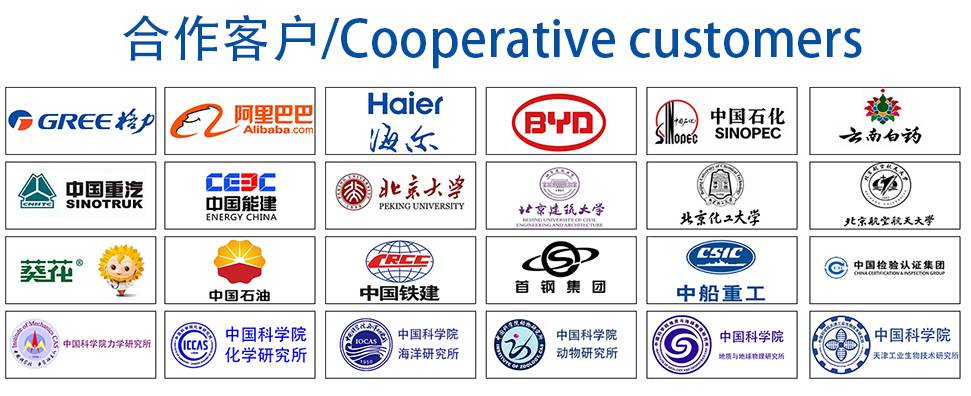
材料實驗室
熱門檢測
15
12
12
9
10
14
11
14
12
11
13
11
19
12
13
13
10
12
10
6
推薦檢測
聯系電話
400-635-0567