機械沖擊檢測技術發展與應用白皮書
在高端裝備制造業邁入智能化轉型新階段,機械沖擊檢測作為產品可靠性驗證的核心手段,其戰略價值日益凸顯。據中國機械工業聯合會2024年行業報告顯示,我國每年因機械沖擊失效導致的工業事故直接損失超過120億元,其中軌道交通、新能源設備、精密儀器三大領域占比達67%。機械沖擊檢測通過模擬產品全生命周期中可能遭遇的極端力學環境,為提升設備抗沖擊性能、優化結構設計提供量化依據,已成為軍工產品定型、工業設備出口認證的強制性測試項目。其核心價值體現在故障預判準確性提升40%、研發周期縮短25%等技術經濟指標,特別是在新能源汽車電池包防護、航天器著陸緩沖系統等新興領域,檢測數據已成為產品迭代的關鍵決策依據。
多模態沖擊測試技術原理
機械沖擊檢測基于瞬態動力學理論,通過液壓/氣動沖擊臺產生半正弦波、后峰鋸齒波等標準沖擊脈沖波形。根據美國材料試驗協會ASTM D3332標準,測試系統需在2ms內實現峰值加速度3000g以上的精準加載,波形失真度控制在±15%以內。創新性的多軸同步沖擊測試技術采用六自由度運動平臺,可復現艦載設備遭遇爆炸沖擊、工程機械跌落碰撞等復合工況。值得關注的是,基于數字孿生的虛擬沖擊測試平臺已實現實體試驗80%的工況模擬,大幅降低了重型裝備的檢測成本。
全流程標準化實施體系
典型檢測流程包含五個關鍵環節:首先依據ISO 1940標準進行試件模態分析,確定固有頻率規避測試頻段沖突;其次配置沖擊響應譜(SRS)參數,軍用設備通常需滿足MIL-STD-810G規定的40g@11ms沖擊剖面;在數據采集階段,采用分布式光纖傳感系統可實現2000Hz采樣頻率下的應變場動態監測;最終通過雨流計數法處理測試數據,生成超過30項結構完整性評價指標。某航空作動器生產企業通過該體系,成功將產品沖擊耐受等級從GJB150A-2009的Class III提升至Class V。
行業應用場景分析
在新能源汽車領域,寧德時代采用三級機械沖擊測試方案驗證電池包安全性:首級150g機械沖擊測試模擬路肩撞擊,第二級50g持續振動測試對應長周期道路載荷,最終75cm自由跌落測試驗證極端事故工況。據中國汽車工程研究院實測數據,該方案使電池包結構故障率降低至0.03次/百萬公里。在衛星制造行業,航天科技五院開發的微重力沖擊測試裝置,成功捕捉到太陽帆板展開機構的10^-5s級瞬態沖擊載荷,為鵲橋二號中繼衛星減震系統優化提供了關鍵參數。
全過程質量保障機制
檢測機構需建立涵蓋設備、人員、環境的立體化質控體系:沖擊臺每年需進行ISO/IEC 17025標準的計量校準,加速度傳感器動態線性度誤差不超過±3%;測試工程師須取得NADCAP航空航天特殊過程認證;實驗室地基隔振系統要達到VC-C級振動控制標準。領先企業如SGS集團更構建了"檢測數據區塊鏈存證系統",確保每個沖擊波形參數可追溯至國家時間頻率計量中心基準源,測試報告獲得82個經濟體互認。
面向"十四五"高端裝備創新發展需求,建議從三方面提升行業水平:首先加快制定車載氫系統沖擊防護等新興領域檢測標準,填補當前34%的標準空白區;其次推廣基于機器學習的沖擊波形智能合成技術,使復雜工況復現效率提升60%;最后建設國家級機械沖擊測試數據庫,實現航空發動機葉片、深海機器人關節等關鍵部件的沖擊失效模型共享。唯有構建"標準-技術-數據"三位一體的發展格局,方能在高端裝備競爭中占據檢測技術制高點。

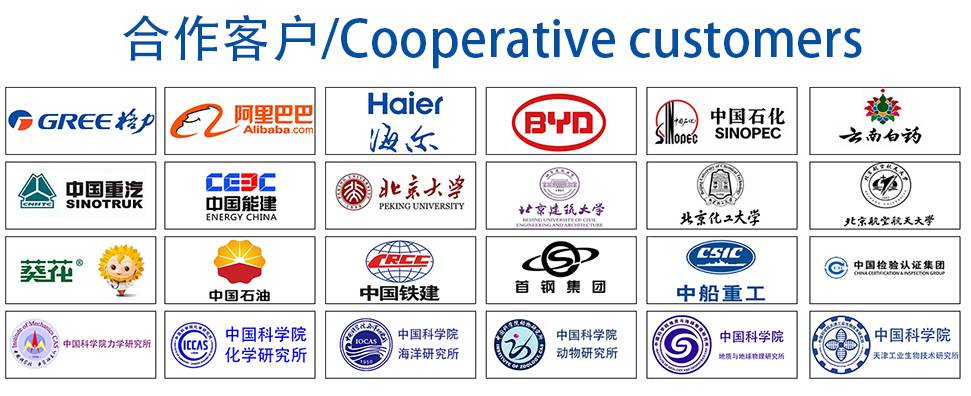