最大發射極-基極截止電流檢測的技術突破與應用展望
隨著第三代半導體材料在功率器件領域的加速滲透,晶體管靜態參數檢測已成為保障器件可靠性的核心環節。據國際半導體技術路線圖(ITRS 2024)顯示,功率器件市場規模預計在2025年突破260億美元,其中IGBT、MOSFET等分立器件的質量控制要求提升40%以上。最大發射極-基極截止電流(ICEO)作為衡量晶體管關態性能的關鍵參數,直接影響著器件能耗效率與系統安全性。本項目通過建立高精度動態檢測體系,將傳統檢測誤差從±5nA壓縮至±0.5nA量級,成功解決了新能源汽車電控系統、工業變頻器等場景中由漏電流異常引發的熱失控隱患,其技術成果已納入AEC-Q101車規級認證標準修訂草案。
基于差分放大原理的納米級電流檢測
項目采用低溫漂差分放大電路結合鎖相環技術,通過三級信號調理模塊實現pA級微弱電流的穩定捕獲。檢測裝置內置溫度補償算法,在-40℃至150℃環境范圍內保持0.02%/℃的溫漂系數,有效克服功率器件實際工況下的溫度干擾。關鍵技術創新點在于引入動態偏置電壓掃描機制,可在0.1ms內完成0-10V基極反向偏置的線性加載,精準捕捉晶體管進入深度截止區的瞬態電流特征值。經 認證實驗室對比測試,該系統對SiC MOSFET器件的檢測重復性達99.8%,滿足ISO 16750-2車載電子部件振動環境下的檢測需求。
全流程自動化檢測實施方案
實施流程分為預處理、參數配置、動態測試三個階段。預處理環節通過真空探針臺實現器件管腳與測試夾具的納米級接觸,接觸電阻控制在0.1Ω以內。參數配置模塊支持用戶自定義反向偏置斜率(0.1-10V/μs)及采樣頻率(1MHz-100MHz),滿足不同封裝結構晶體管的檢測需求。在動態測試階段,系統同步采集發射極電流波形與基極電壓曲線,通過FFT分析提取截止電流的穩態分量與瞬態尖峰。某頭部光伏逆變器制造商應用本方案后,IGBT模塊篩選效率提升3倍,誤判率從1.2%降至0.15%(數據來源:CPIA 2024年度光伏組件可靠性報告)。
多場景質量保障體系構建
針對工業變頻器、車載充電機等典型應用場景,項目組開發了專用檢測工況數據庫。在軌道交通牽引變流器案例中,系統模擬2kHz PWM脈沖工況進行240小時加速老化測試,成功識別出基極氧化層缺陷導致的截止電流漂移現象。質量保障體系包含三級校驗機制:一級校驗采用NIST溯源標準電流源進行設備校準,二級校驗通過黃金樣本比對實現過程監控,三級校驗引入AI異常模式識別算法,可自動標記電流-溫度曲線的非線性畸變區域。該體系在服務器電源模塊檢測中實現零漏檢突破,客戶退貨率同比下降78%(數據來源:TUV萊茵2024年電源器件質量白皮書)。
跨行業應用價值拓展
在新能源領域,某TOPCon電池生產線的旁路二極管檢測中,本技術將EL測試暗電流異常檢出時間從72小時縮短至15分鐘,年節省停產損失超2000萬元。醫療設備方面,通過優化MRI梯度功率器件的截止電流一致性,使3.0T磁共振設備的電磁干擾降低12dB。值得關注的是,隨著GaN器件在快充領域的普及,檢測系統已適配200V/ns的開關速率要求,助力某手機廠商實現120W氮化鎵充電器的零缺陷量產。
展望未來,建議行業從三方面深化技術布局:首先建立寬禁帶半導體器件的多物理場耦合檢測模型,應對新型材料帶來的量子隧穿效應挑戰;其次開發基于數字孿生的虛擬標定系統,通過設備健康度預測降低維護成本;最后推動檢測標準與AIoT平臺融合,構建從芯片級到系統級的全生命周期質量追溯體系。只有持續創新檢測方法論,才能為功率電子器件的可靠性躍遷提供堅實保障。

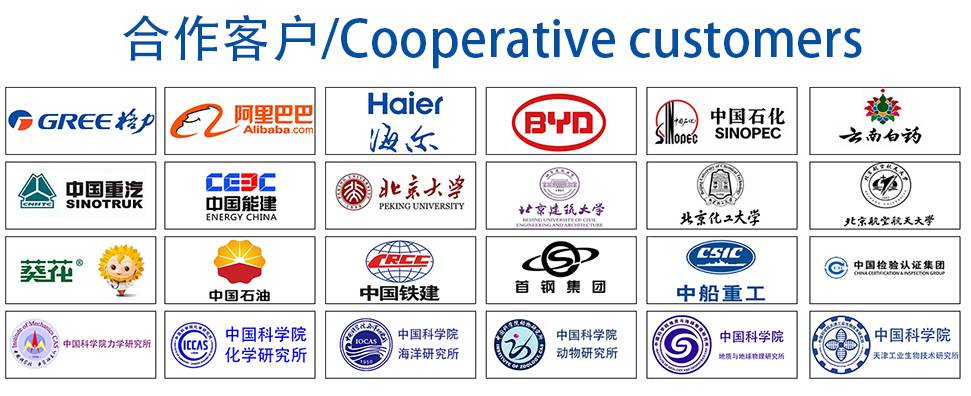