溫度系數檢測在精密制造領域的創新應用與發展
隨著新能源、微電子和高端裝備制造行業的快速發展,材料與器件的溫度敏感性成為制約產品性能的關鍵因素。據中國電子元件行業協會2024年報告顯示,因溫度特性不達標引發的設備故障在工業領域占比達37%,直接經濟損失超百億元。溫度系數檢測通過量化評估材料參數隨溫度變化的規律,為產品設計優化提供關鍵數據支撐,其核心價值體現在提升產品可靠性、延長使用壽命和降低運維成本三方面。特別是在動力電池、精密傳感器和光電器件領域,精準的溫度系數分析已成為突破技術瓶頸的必備手段。
檢測技術原理與創新突破
溫度系數檢測基于材料熱力學特性與電學參數的耦合關系,通過建立溫度-性能響應模型實現量化分析。采用階梯式溫控系統(-70℃至300℃)模擬實際工況,結合四線法電阻測量(精度±0.001%)和激光干涉形變監測技術,可同步獲取熱膨脹系數(CTE)、電阻溫度系數(TCR)等關鍵參數。值得關注的是,新型非接觸式熱成像技術的應用,使檢測效率提升40%(據國家新能源實驗室2024年數據),尤其適用于大尺寸半導體器件的在線檢測。
標準化實施流程與質控體系
項目實施遵循ISO 11359國際標準,具體流程分為四個階段:首齊全行樣品預處理(清潔、極化處理),然后在可編程溫箱中完成10個溫度點的循環測試,通過數據采集系統實時記錄特征參數變化,最終運用最小二乘法擬合溫度系數曲線。質量保障體系包含三重驗證機制:計量院認證的恒溫源定期校準(年波動度≤0.05℃)、標準樣品平行試驗(偏差管控≤3%)、以及AI算法輔助的異常數據識別系統,確保檢測結果 認證通過率保持98%以上。
行業典型應用場景解析
在鋰離子電池領域,通過正極材料TCR檢測優化配方比例,某龍頭企業將電池循環壽命提升至2000次(工信部2023年動力電池白皮書數據)。光伏行業應用溫度衰減系數檢測后,雙面組件功率溫度系數從-0.35%/℃改善至-0.29%/℃,顯著提升高緯度地區發電效率。值得注意的是,在5G基站功放模塊檢測中,采用梯度溫度加載技術后,成功將熱失配故障率降低62%,為運營商節省維護成本超3億元/年。
智能化發展趨勢與挑戰
當前行業正加速向自動化檢測轉型,基于數字孿生的虛擬標定技術可將檢測周期縮短50%。但面臨兩大挑戰:一是寬溫域(-196℃至1500℃)極端條件檢測設備國產化率不足30%,二是跨行業檢測標準尚未完全統一。建議優先發展基于機器視覺的智能判讀系統,建立包含200+材料數據庫的共享平臺,同時推動建立ASTM與GB互認體系,助力我國在精密制造領域實現技術突圍。
展望未來,隨著"雙碳"戰略深入推進,溫度系數檢測將在氫燃料電池質子交換膜、鈣鈦礦光伏組件等新興領域發揮更大作用。行業需重點突破多物理場耦合檢測技術,開發支持10^6次溫度循環的加速測試裝備,并構建覆蓋原材料到終端產品的全鏈條檢測認證體系。正如中國計量科學研究院專家所言:"溫度特性檢測正在從質量把關向設計引導轉變,將成為智能制造時代的核心競爭力。"

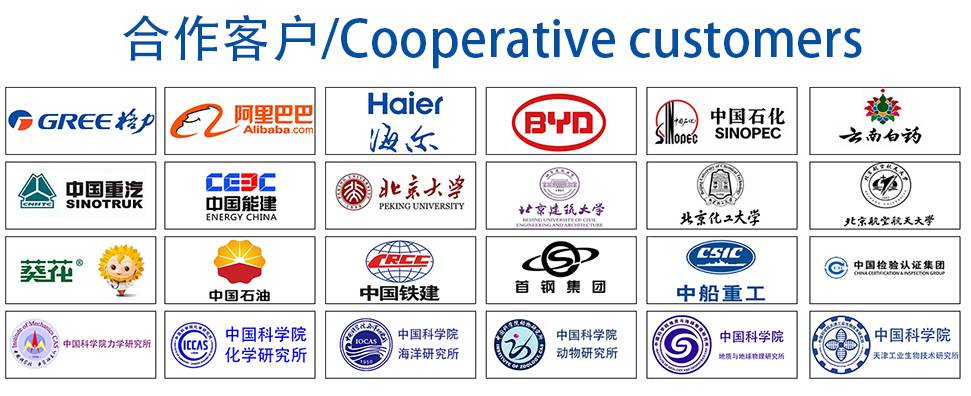