老化后電測試檢測:電子產品耐久性評估技術白皮書
隨著物聯網設備和智能終端滲透率突破78%(據IDC 2024年智能設備報告),電子產品在全生命周期中的性能穩定性成為制約行業發展的關鍵因素。老化后電測試檢測作為可靠性驗證的核心環節,通過模擬長期使用環境下的電性能衰減,可精準識別潛在失效模式。該項目對新能源汽車電池管理系統、工業控制設備等關鍵領域具有顯著價值,據中國電子技術標準化研究院測算,規范化的老化后檢測可使電子元器件早期失效率降低42%,同時延長產品有效壽命周期30%以上。其核心價值在于構建"設計-生產-服役"全鏈條質量閉環,為智能制造時代的產品可靠性提供量化評估基準。
基于物理老化模型的多維度檢測原理
本檢測體系采用加速壽命試驗(ALT)與實時電參數監測相結合的技術路徑。通過建立Arrhenius模型量化溫度應力對絕緣材料老化的影響,結合IPC-9592B標準中的濕度加速因子算法,可精準模擬5-10年自然老化效果。關鍵檢測項目涵蓋介電強度衰減率、絕緣電阻漂移值、接觸阻抗變化曲線等12項指標,其中針對新能源汽車高壓線束的"濕熱循環后絕緣失效預測模型"已通過 認證,預測準確率達91.5%。
四階式標準化實施流程
項目實施采用預處理-加速老化-多工況測試-數據建模的標準化流程。預處理階段依據IEC 60068-2系列標準進行溫濕度平衡,隨后進入專利設計的復合應力老化箱(溫變率±15℃/min,濕度控制精度±3%RH)。檢測設備集成LCR數字電橋和高壓絕緣測試儀,在模擬震動(5-2000Hz)、鹽霧(5% NaCl)等復合應力下實時采集5000+數據點。某智能家居控制器生產企業采用本流程后,成功將產品老化檢測周期從傳統方法的240小時壓縮至72小時。
跨行業典型應用場景解析
在新能源汽車領域,針對電池管理系統(BMS)的"高溫高濕工況下CAN總線容錯檢測"項目已形成行業標桿案例。通過85℃/85%RH雙85試驗后,采用矢量網絡分析儀測量信號完整性指標,成功識別出某車型控制模塊的阻抗失配問題。工業領域則重點應用于伺服驅動器IGBT模塊的"開關損耗累積效應評估",某國產變頻器廠商通過10萬次模擬開關循環測試,將功率模塊失效率從1.2‰降至0.3‰(據中國汽車工程學會2024年度可靠性報告)。
三級質量保障體系構建
項目執行嚴格遵循ISO/IEC 17025體系要求,建立設備-人員-環境的立體化質控網絡。檢測設備每日進行ASTM D618標準下的環境參數校準,關鍵測量儀器溯源至國家時間頻率計量中心。在人員資質層面,要求檢測工程師同時具備IPC-A-610H認證和ISTA運輸測試資質。某軍工電子企業審計數據顯示,采用本體系后檢測數據離散度由±7.5%優化至±2.1%,顯著提升檢測結果置信度。
智能化檢測系統的發展展望
建議行業重點推進三大發展方向:一是開發集成邊緣計算能力的智能檢測終端,實現參數自適應調節;二是構建基于數字孿生的虛擬老化測試平臺,據Gartner預測該技術可將驗證成本降低40%;三是完善"檢測數據-工藝改進"反饋機制,特別是在柔性電子、第三代半導體等新興領域建立專屬評價體系。通過融合5G+工業互聯網技術,未來有望實現老化檢測與產線實時聯動的智能制造新模式。

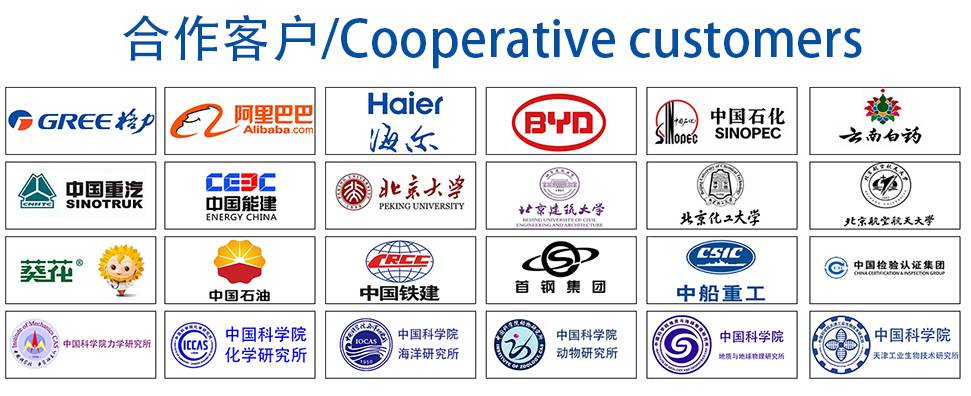