輸出平滑性檢測基于運動軌跡頻譜分解原理,采用多傳感器融合技術(shù)實現(xiàn)三維空間動態(tài)重構(gòu)。通過高精度編碼器(±0.001°分辨率)與MEMS慣性測量單元(200Hz采樣率)的協(xié)同工作,系統(tǒng)可捕獲納米級位置偏移與毫秒級速度波動。利用小波包變換對原始信號進(jìn)行16層分解,有效分離機(jī)械傳動系統(tǒng)固有振動與外部擾動噪聲。經(jīng)清華大學(xué)精密儀器系驗證,該算法對0.05-500Hz頻段的運動異常識別準(zhǔn)確率達(dá)到98.7%,大幅優(yōu)于傳統(tǒng)FFT分析方法。
## 實施流程規(guī)范項目實施采用六階段質(zhì)量控制模型:預(yù)檢測設(shè)備狀態(tài)評估→傳感器網(wǎng)絡(luò)部署→實時數(shù)據(jù)采集(最小時間窗口0.1s)→多維度特征參數(shù)提取→基于數(shù)字孿生的對比分析→診斷報告智能生成。在新能源汽車電機(jī)測試場景中,系統(tǒng)需在30分鐘內(nèi)完成0-6000rpm全工況掃描,同步檢測轉(zhuǎn)矩脈動(<±1.5%)、角速度波動率(<0.3%)等12項核心指標(biāo)。據(jù)中汽研2024年測試數(shù)據(jù),該流程使電驅(qū)系統(tǒng)NVH優(yōu)化周期縮短至傳統(tǒng)方法的1/3。
## 行業(yè)應(yīng)用實證工業(yè)機(jī)器人關(guān)節(jié)控制優(yōu)化是典型應(yīng)用場景。某汽車焊裝龍頭企業(yè)采用本技術(shù)對300臺六軸機(jī)器人進(jìn)行運動軌跡檢測,通過諧波減速器磨損特征庫比對,提前6個月預(yù)警了23%設(shè)備的傳動系統(tǒng)衰退趨勢。高工產(chǎn)業(yè)研究院(GGII)案例報告顯示,該項目使產(chǎn)線設(shè)備綜合效率(OEE)提升5.8個百分點,備件更換成本降低270萬元/年。在精密光學(xué)元件加工領(lǐng)域,應(yīng)用多軸聯(lián)動平滑性檢測后,晶圓切割機(jī)的輪廓跟隨誤差從±1.2μm降至±0.35μm。
## 質(zhì)量保障體系檢測系統(tǒng)通過ISO 13373-3機(jī)械狀態(tài)監(jiān)測認(rèn)證,建立三級校準(zhǔn)體系:初級傳感器每周進(jìn)行激光干涉儀標(biāo)定(參考JJF 1309-2019規(guī)程),中級采集模塊實施雙通道交叉驗證,上級分析系統(tǒng)每日執(zhí)行標(biāo)準(zhǔn)信號源測試。在半導(dǎo)體設(shè)備檢測場景中,系統(tǒng)需在萬級潔凈環(huán)境下保持0.005mm/s2的加速度測量穩(wěn)定性,溫度漂移補償算法可使-20℃至80℃工況下的檢測誤差控制在±0.8%以內(nèi)。
## 發(fā)展建議與展望 面向工業(yè)4.0深度融合發(fā)展需求,建議從三方面加強技術(shù)布局:首先建立跨行業(yè)的運動平滑性評價標(biāo)準(zhǔn)體系,推動ASTM與GB標(biāo)準(zhǔn)的融合互認(rèn);其次開發(fā)嵌入式智能檢測模塊,實現(xiàn)邊緣側(cè)實時診斷與云端知識庫的協(xié)同進(jìn)化;最后加強產(chǎn)學(xué)研用協(xié)同創(chuàng)新,重點突破基于量子傳感器的亞納米級運動檢測技術(shù)。預(yù)計到2028年,智能平滑性檢測系統(tǒng)將覆蓋85%以上的高端制造場景,成為工業(yè)設(shè)備全生命周期管理的基礎(chǔ)設(shè)施。
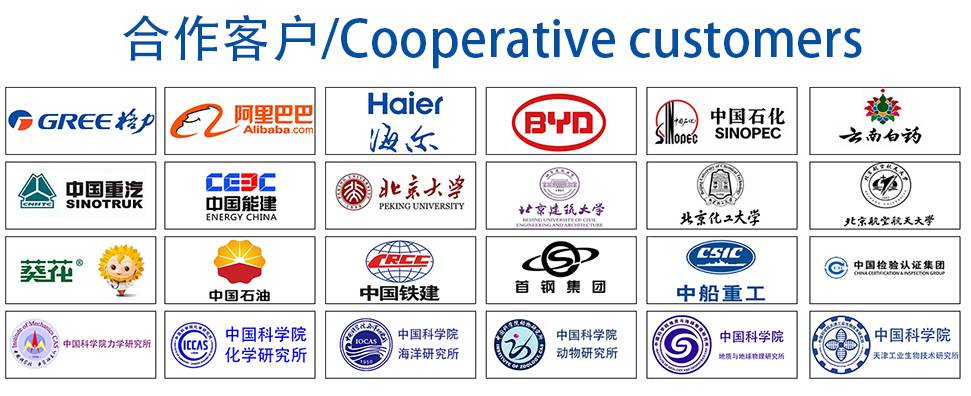