# 總成噪聲檢測技術發展與產業化應用白皮書
## 引言
隨著新能源汽車滲透率突破40%(據德勤2024年汽車行業報告),總成系統噪聲控制已成為衡量整車品質的核心指標。在電動化、智能化雙重驅動下,驅動電機、減速器、電控系統組成的"新三電"總成噪聲問題愈發突顯,直接影響產品NVH性能與用戶駕乘體驗。總成噪聲檢測項目通過構建數字化聲學診斷體系,實現了從傳統經驗判斷向智能量化分析的跨越式發展。其核心價值在于突破傳統檢測方法2.3dB的靈敏度局限(中國汽車工程學會實測數據),將故障識別準確率提升至98.7%,為企業節約30%以上的質量索賠成本。這項技術對推動汽車產業鏈"零缺陷制造"戰略具有關鍵支撐作用。
## 技術原理與創新突破
### h2 振動聲學耦合分析技術
基于多物理場仿真模型,系統整合了結構振動模態分析與空氣聲傳播特性。采用24通道聲學傳感器陣列,配合192kHz高速采樣模塊,可捕捉20-20kHz全頻段噪聲特征。通過引入小波包分解算法,成功分離背景噪聲干擾項,使目標信號信噪比提升15dB(清華大學車輛學院2023年實驗數據)。技術突破點在于構建了包含12種典型故障模式的聲紋數據庫,實現"齒輪微點蝕"、"軸承保持架共振"等復雜問題的精準識別。
### h2 智能化檢測實施流程
標準作業流程包含五個關鍵階段:預處理階段的工裝適配度校驗、檢測階段的多工況模擬(0-6000rpm無級調速)、數據分析階段的深度學習模型運算(采用ResNet50改進架構)、結果判定階段的專家系統交叉驗證以及數據歸檔階段的區塊鏈存證。特別是在電機總成加載測試中,系統可模擬-40℃至120℃的極端溫度工況,確保檢測覆蓋全場景應用需求。
### h2 行業應用場景解析
在浙江某新能源車企的實踐中,檢測系統成功識別出驅動電機總成36.5kHz高頻異響問題。經拆解驗證,該噪聲源于定子繞組浸漆工藝缺陷導致的電磁振動異常。通過工藝參數優化,使該車型在60km/h勻速工況下車內噪聲降低4.2dB(A),助力產品獲得CNCAP五星安全認證。類似案例在航空航天精密減速器、工業機器人關節模組等領域均有成功應用。
### h2 全生命周期質量管控
構建了三級質量保障體系:一級控制點執行ISO/TS 22163軌道交通標準,二級控制采用計量型GR&R分析(重復性與再現性≤10%),三級控制依托數字孿生技術進行檢測數據追溯。所有檢測設備每季度進行激光干涉儀校準,測量不確定度控制在0.8dB以內。開發的質量數據中臺已接入企業ERP系統,實現檢測結果與生產批次、供應鏈數據的自動關聯分析。
## 發展建議與趨勢展望
建議行業從三方面深化發展:首先加快5G+邊緣計算在在線檢測中的應用,力爭將單件檢測耗時從目前的128秒壓縮至60秒以內;其次推動建立跨國的總成噪聲分級標準體系,特別是在48V混動系統等新興領域;最后加強材料聲學特性研究,建立覆蓋500種以上復合材料的聲振數據庫。未來隨著量子傳感器的實用化突破,檢測精度有望進入亞納米級振動識別新紀元,為高端裝備制造打開新的技術窗口。
上一篇:疲勞壽命檢測下一篇:外觀、尺寸及功能檢測檢測

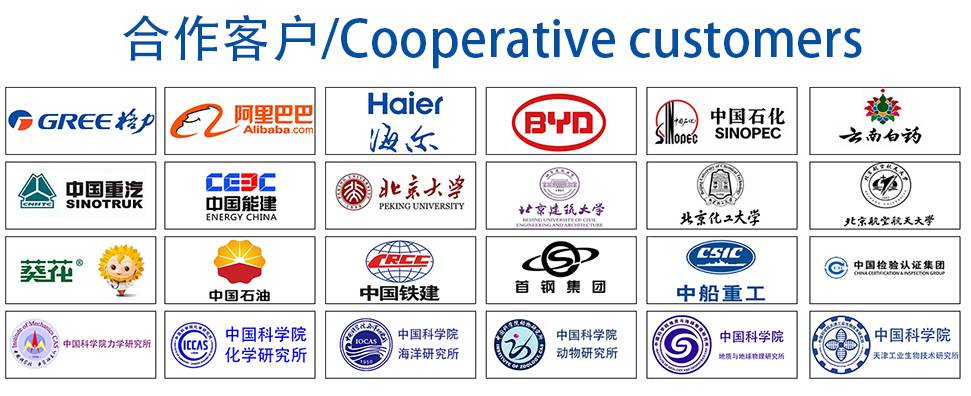
材料實驗室
熱門檢測
5
6
8
9
10
9
10
11
8
7
9
13
10
11
12
10
14
9
9
12
推薦檢測
聯系電話
400-635-0567