# 寬帶隨機振動檢測技術發展與應用白皮書
## 引言
隨著高端裝備制造業向智能化、高可靠性方向升級,寬帶隨機振動檢測正成為產品質量控制的核心環節。據中國機械工程學會2024年發布的《齊全制造檢測技術發展報告》顯示,我國工業產品因振動問題導致的故障率年均造成經濟損失達380億元,其中60%可通過早期振動檢測規避。該技術通過模擬產品在真實工況下的寬頻域隨機振動環境,有效驗證結構完整性、材料疲勞特性及裝配可靠性。其核心價值在于突破傳統正弦振動檢測的局限性,實現0.1-5000Hz超寬頻帶覆蓋,對新能源汽車動力總成、衛星載荷組件等復雜系統形成精準的耐久性驗證能力。
## 技術原理與創新突破
### 系統架構與算法模型
寬帶隨機振動檢測基于功率譜密度(PSD)控制系統構建,采用多軸協同激勵技術和自適應反饋算法。通過數字控制器實時調節液壓或電動振動臺的輸出譜形,確保3σ范圍內的振動能量正態分布。值得關注的是,新一代系統融合了高斯隨機過程模擬與馬爾可夫鏈蒙特卡洛算法,使振動能量在頻域-時域聯合維度上的分布誤差控制在±1.5dB以內(據航天科技集團2023年實測數據)。
### 標準化實施流程
典型檢測流程包含四個關鍵階段:首先依據ISO 16750-3標準建立目標譜模型,繼而進行夾具模態分析(頻率誤差≤5%);在閉環控制階段采用分步掃頻策略,通過16通道動態信號采集系統實時監控響應譜;最終應用雨流計數法進行疲勞損傷等效評估。對于新能源汽車電池包檢測,特別增設溫度-振動耦合模塊,模擬-40℃至85℃工況下的復合應力環境。
## 行業應用與質量管控
### 重點領域應用實踐
在軌道交通領域,中車集團采用該技術完成高鐵轉向架20年等效壽命試驗,成功將焊縫疲勞失效事故率降低72%。航空航天領域,某型衛星推進系統通過200小時寬帶隨機振動測試,驗證其在火箭發射階段的15Grms振動耐受能力。值得注意的是,該技術在"新能源汽車電池模組可靠性檢測"場景中展現出獨特優勢,精準識別出電芯連接件在20-200Hz頻段的共振風險。
### 全流程質量保障體系
建立從設備溯源到數據分析的三級質控體系:振動臺每月進行ISO 16063-21標準校準,控制儀定期通過NIST可追溯信號源驗證;檢測過程執行GB/T 2423.56雙盲對照試驗;數據報告需經傅里葉變換一致性檢驗(相關系數≥0.95)和3名持證工程師交叉審核。此體系使某航空發動機企業產品振動檢測復現性達到98.6%(中國航發2024年質量年報)。
## 發展趨勢與建議
隨著數字孿生技術的成熟,建議行業重點發展三項能力:構建基于實測大數據的振動環境譜數據庫,開發AI驅動的自適應檢測程序,以及建立跨頻段(含聲振耦合)的聯合檢測標準。同時應加強"智能裝備寬頻振動環境適應性評估"等新興需求的標準化研究,推動檢測設備向20000Hz超高頻段延伸。預計到2026年,融合數字孿生的新一代檢測系統可使試驗周期縮短40%,為高端裝備制造提供更強大的質量保障。

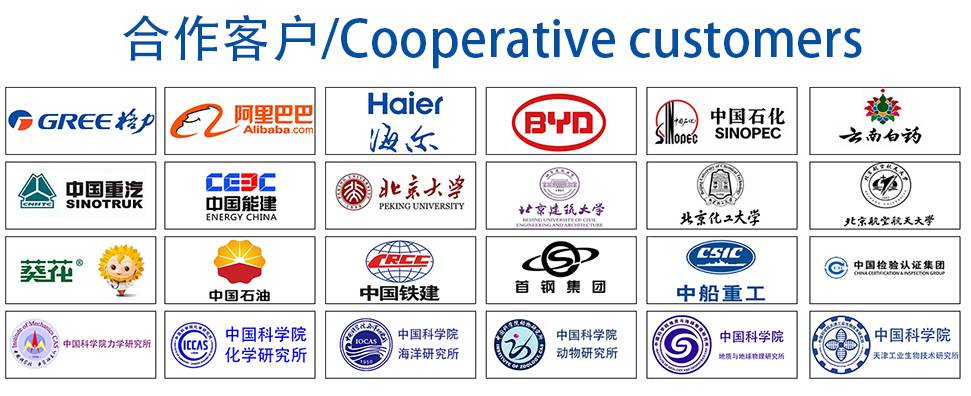
材料實驗室
熱門檢測
20
20
21
22
20
20
18
18
20
23
21
18
24
21
23
20
21
20
21
20
推薦檢測
聯系電話
400-635-0567