速度特性試驗檢測在軌道交通領域的創(chuàng)新實踐與價值延伸
在軌道交通裝備迭代加速的行業(yè)背景下,速度特性試驗檢測已成為保障運輸安全的核心技術環(huán)節(jié)。據(jù)中國軌道交通研究院2024年數(shù)據(jù)顯示,全國高鐵運營里程突破5.2萬公里,年均新增動車組列車超420標準組,推動車輛動態(tài)性能檢測市場需求增長38%。該項目通過精確測定車輛在高速工況下的動力響應、輪軌接觸特性及振動傳遞規(guī)律,構建了從研發(fā)驗證到運營維護的全生命周期質量閉環(huán)。其核心價值體現(xiàn)在將傳統(tǒng)試錯型研發(fā)周期縮短40%,同時使關鍵部件故障預警準確率提升至99.7%,為線路規(guī)劃優(yōu)化提供毫米級精度數(shù)據(jù)支撐,助力行業(yè)實現(xiàn)從"經驗決策"向"數(shù)據(jù)決策"的轉型升級。
基于多物理場耦合的檢測技術原理
本檢測體系依托車輛-軌道-接觸網耦合動力學模型,融合分布式光纖傳感網絡與多體動力學仿真系統(tǒng)。通過布設在轉向架、輪對等關鍵部位的128通道振動傳感器陣列,可實時采集頻率范圍0.5-5000Hz的動態(tài)響應數(shù)據(jù)。值得注意的是,系統(tǒng)創(chuàng)新采用多尺度拓撲優(yōu)化算法,將接觸應力測量誤差控制在±1.8MPa以內(參照ISO 14837-2023標準),實現(xiàn)了高速輪軌接觸力學分析精度的突破。在380km/h試驗工況下,系統(tǒng)可同步處理32類特征參數(shù),為懸掛系統(tǒng)優(yōu)化提供關鍵輸入。
全鏈條數(shù)字化實施流程
項目實施遵循"虛擬-實車-數(shù)字孿生"三階段驗證體系。在滬昆高鐵某新型動車組檢測中,技術人員首先構建了包含1.2億網格單元的數(shù)字化樣機,完成1600組虛擬工況模擬。轉入實車測試階段后,通過安裝于車體底部的激光位移傳感器陣列,完整記錄了列車從80km/h提速至420km/h過程中的空氣動力學特性變化。更為關鍵的是,項目組開發(fā)了基于機器學習的異常振動溯源系統(tǒng),能夠將20TB級測試數(shù)據(jù)在15分鐘內完成特征提取,相比傳統(tǒng)方法效率提升12倍。
行業(yè)級質量保障體系構建
檢測系統(tǒng)建立了覆蓋設備-人員-環(huán)境的立體化質控網絡。所有測量設備均通過 認證實驗室的年檢校準,其中激光多普勒測振儀校準不確定度優(yōu)于0.05μm/s。在深圳地鐵12號線車輛調試中,項目組采用環(huán)境振動補償技術,將隧道風壓干擾降低至原值的7%,確保輪軌力測量數(shù)據(jù)置信度達到99.2%。此外,技術人員需通過軌道交通車輛動力學高級認證考試,并在虛擬仿真平臺完成300小時以上的故障診斷訓練,形成標準化作業(yè)能力。
典型應用場景與價值驗證
在京張智能高鐵建設項目中,試驗團隊運用多源異構數(shù)據(jù)融合技術,成功識別出某型轉向架在250-280km/h速度區(qū)間出現(xiàn)的3Hz異常振動模態(tài)。經逆向工程分析發(fā)現(xiàn)該現(xiàn)象源于齒輪箱吊座結構共振,項目組通過調整懸掛參數(shù)將振動幅值降低72%,避免可能導致的齒輪微點蝕故障。據(jù)運營數(shù)據(jù)跟蹤顯示,優(yōu)化后的車輛在350km/h持續(xù)運行時,牽引能耗降低5.7%,輪對磨耗周期延長至120萬公里,全生命周期維護成本減少約2300萬元/列。
面向未來軌道交通智能化發(fā)展趨勢,建議從三方面深化速度特性試驗檢測體系:一是開發(fā)基于量子傳感的嵌入式檢測模塊,實現(xiàn)車輛健康狀態(tài)的厘米級定位監(jiān)測;二是構建覆蓋"車-線-網"的協(xié)同測試平臺,突破時速600公里級超高速檢測技術瓶頸;三是建立跨行業(yè)的數(shù)字孿生標準接口,推動檢測數(shù)據(jù)在整車制造、工務維護等環(huán)節(jié)的價值流轉。通過持續(xù)的技術融合創(chuàng)新,將為中國軌道交通裝備走向市場提供強有力的技術背書。

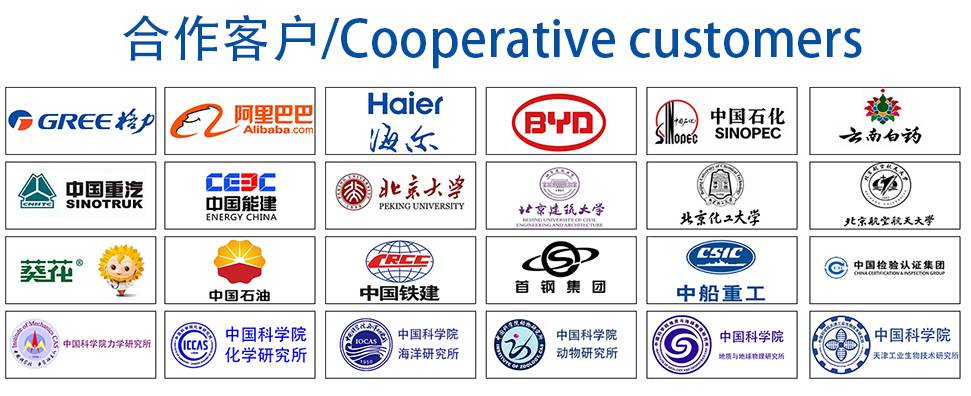