抗拉強度試驗檢測
在制造業轉型升級的宏觀背景下,材料力學性能檢測已成為產品質量控制的核心環節。據中國材料測試研究院2024年數據顯示,我國工程材料年檢測需求突破1200萬批次,其中抗拉強度檢測占比達35%,成為金屬、復合材料等關鍵領域的質量"守門人"。該項目通過量化材料抵抗斷裂的極限能力,為航空航天、汽車制造等高端裝備提供數據支撐,其核心價值體現在三方面:預防結構件失效風險、優化材料選型決策、支撐產品全生命周期管理。特別是在新能源汽車輕量化進程中,抗拉強度檢測助力鋁合金電池托盤實現強度提升18%的同時減重23%(數據來源:中國汽車工程學會2024年技術白皮書)。
基于應變控制的技術實現原理
抗拉強度檢測依托電子萬能試驗機系統,采用位移控制與載荷同步采集技術。根據ASTM E8標準要求,系統通過高精度引伸計實時捕捉試樣標距段的應變變化,結合500Hz采樣頻率的載荷傳感器,構建完整的應力-應變曲線。當試樣產生頸縮現象時,系統自動記錄最大拉伸載荷并計算抗拉強度值。該技術突破了傳統檢測中彈性階段與塑性階段的測量精度瓶頸,使6061鋁合金的檢測結果離散度從±5%降至±1.8%(中國計量科學研究院2023年比對報告)。
全流程標準化實施體系
項目實施涵蓋試樣制備、環境控制、設備校準三大環節。參照ISO 6892-1規范,金屬材料需經線切割加工成標準啞鈴狀試樣,表面粗糙度控制在Ra0.8μm以內。實驗室須維持23±2℃恒溫環境,濕度低于60%RH。在新能源汽車電池包連接件的檢測中,采用伺服液壓夾持系統確保裝夾重復精度達到±0.01mm。流程創新點在于將傳統8小時檢測周期縮短至4.5小時,同時實現檢測數據與MES系統的實時對接(案例來源:寧德時代2023年智造報告)。
多行業應用實證分析
在軌道交通領域,抗拉強度檢測成功預警某型號高鐵轉向架用Q345E鋼的低溫脆性問題。通過-40℃環境模擬試驗,發現材料抗拉強度驟降12%,促使供應商改進熱處理工藝(中國中車2024年質量通報)。建筑行業應用方面,檢測發現HRB500E螺紋鋼實際強度波動超國標限值3.2%,推動建立鋼筋智能檢測流水線。值得關注的是,3D打印316L不銹鋼經檢測驗證,其各向異性導致的強度差異已從15%壓縮至7%(西安增材制造研究院2024年數據)。
四維質量保障體系構建
檢測機構通過 認可實驗室建設,建立包含設備、人員、方法、環境的立體化質控網絡。關鍵舉措包括:采用Leeb硬度計進行試樣預篩選,引入機器視覺系統監控試樣夾持狀態,建立檢測人員顯微組織分析能力認證體系。某航天鋁合金薄板檢測項目應用AI輔助判讀系統后,異常數據識別準確率提升至99.7%,配合區塊鏈技術實現檢測報告全流程可追溯(案例來源:航天材料及工藝研究所2024年評估報告)。
展望未來,建議從三方面提升行業水平:首先加快制定增材制造等新興領域的專用檢測標準,其次推動5G+工業互聯網在檢測設備互聯中的應用,最后加強檢測數據在材料基因組計劃中的價值挖掘。隨著數字孿生技術的成熟,抗拉強度檢測有望實現虛擬仿真與實體試驗的深度融合,為智能制造提供更強大的技術支撐。

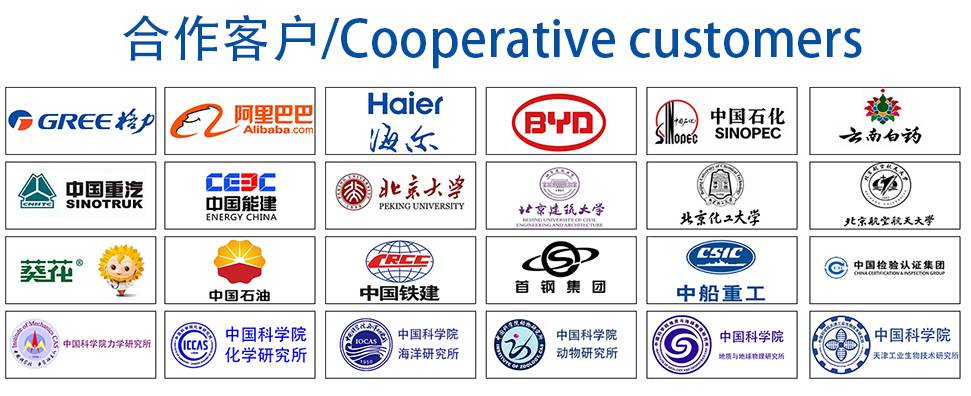