動態密封性能試驗檢測:關鍵檢測項目與方法
一、動態密封性能試驗的核心檢測項目
1. 泄漏量測試
- 目的:量化動態工況下的介質滲出量,評估密封件的密閉能力。
- 測試方法:
- 直接測量法:收集密封界面泄漏的介質體積或質量,通過精密儀器(如流量計、稱重傳感器)記錄數據。
- 間接測量法:利用壓力衰減法或示蹤氣體檢測(如氦質譜檢漏儀)推算泄漏率。
- 評判標準:根據工況壓力、介質類型及行業規范(如ISO 6194、GB/T 14211)設定允許泄漏閾值。例如,高壓液壓系統通常要求泄漏量≤0.1 mL/h。
2. 摩擦特性測試
- 目的:測量密封件與運動部件間的摩擦力或扭矩,優化密封設計以減少能耗與磨損。
- 測試方法:
- 摩擦力測試:通過力傳感器實時監測往復或旋轉運動中密封件的摩擦力。
- 扭矩測試:對旋轉密封件施加恒定轉速,記錄驅動軸扭矩變化(如ASTM D3417)。
- 關鍵參數:摩擦系數、啟動力矩、運行穩定性。
3. 耐壓性能測試
- 目的:驗證密封件在動態工況下承受壓力波動(如脈沖壓力)的能力。
- 測試方法:
- 靜態耐壓測試:逐步加壓至額定壓力的1.5倍,保壓期間監測泄漏。
- 動態壓力測試:模擬實際工況壓力循環(如0~30 MPa高頻波動),記錄密封件疲勞失效前的循環次數。
- 標準參考:ISO 3601-3(液壓氣動用密封圈試驗標準)。
4. 溫度適應性測試
- 目的:評估密封件在極端溫度(低溫脆化、高溫老化)下的密封性能。
- 測試方法:
- 高低溫循環試驗:在溫度箱中進行-50°C至200°C的交替循環,監測泄漏量變化。
- 高溫耐久性測試:恒溫環境下長期運行,觀察材料膨脹或硬化導致的密封失效。
- 典型標準:SAE J200(汽車密封材料耐溫等級分類)。
5. 耐磨性與壽命測試
- 目的:模擬長期運動工況,預測密封件使用壽命。
- 測試方法:
- 加速磨損試驗:提高運動頻率或負載,通過累積磨損量推算實際壽命。
- 實際工況模擬:在試驗臺架上復現真實工作條件(如液壓缸往復運動次數)。
- 關鍵指標:磨損量、表面粗糙度變化、密封唇口完整性。
6. 介質兼容性測試
- 目的:驗證密封材料與接觸介質(油、水、化學試劑等)的相容性。
- 測試方法:
- 浸泡試驗:將密封件置于介質中,定期檢測體積膨脹率、硬度變化。
- 動態介質循環:在介質流動條件下測試溶脹、腐蝕或化學反應的影響。
- 評判依據:體積變化率≤10%、硬度變化≤15%(參考ASTM D471)。
7. 振動與沖擊測試
- 目的:模擬運輸或工作環境中的機械振動對密封性能的影響。
- 測試方法:
- 振動臺試驗:施加正弦振動或隨機振動(頻率5~2000 Hz),監測泄漏情況。
- 沖擊試驗:通過自由落體或氣動沖擊臺模擬瞬時沖擊載荷。
- 參考標準:MIL-STD-810(軍用設備環境試驗方法)。
二、動態密封性能試驗設備與流程
1. 試驗設備
- 動態密封試驗臺:可調節壓力、速度、溫度的專用設備(如伺服液壓試驗機)。
- 數據采集系統:集成壓力傳感器、扭矩儀、溫度控制器等,實時記錄數據。
- 環境模擬裝置:高低溫箱、介質循環系統、振動臺等。
2. 試驗流程
- 預處理:密封件按標準(如ISO 2230)進行溫濕度平衡。
- 安裝調試:密封件裝入模擬工況的夾具,校準傳感器。
- 分階段測試:按順序進行泄漏、摩擦、耐壓等測試,避免交叉干擾。
- 失效分析:對失效密封件進行顯微觀察(SEM)、材料硬度測試等。
三、試驗結果分析與應用
1. 數據分析
- 繪制泄漏率隨時間/壓力變化曲線。
- 對比不同材料(如NBR、FKM、PTFE)的摩擦系數與壽命。
- 通過威布爾分布模型預測密封件可靠性。
2. 優化方向
- 改進密封結構(如副唇設計、波紋補償)。
- 選擇耐高溫、低摩擦材料(如填充聚四氟乙烯)。
- 調整工況參數(降低峰值壓力、優化潤滑條件)。
四、行業標準與規范
標準號 | 名稱 | 適用范圍 |
---|---|---|
ISO 3601-3 | 液壓氣動系統O形圈動態密封試驗方法 | 往復與旋轉密封件 |
GB/T 3452.2 | 液壓氣動用O形圈性能試驗規范 | 國內密封件質量控制 |
SAE J2597 | 旋轉軸唇形密封件試驗程序 | 汽車傳動系統密封 |
ASTM D6545 | 橡膠密封件加速老化試驗方法 | 材料耐候性評估 |
五、
轉成精致網頁

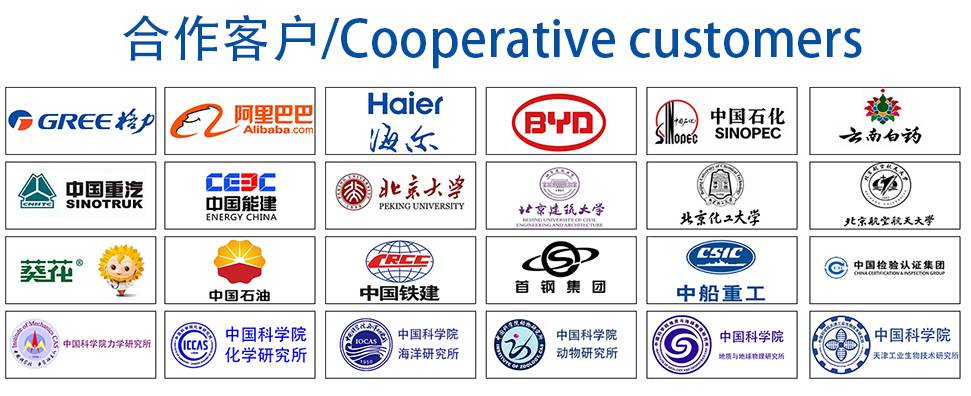
材料實驗室
熱門檢測
推薦檢測
聯系電話
400-635-0567