在制造業數字化轉型加速的背景下,電子電氣產品市場規模持續擴大,據國際市場研究機構TrendForce 2024年報告顯示,智能家電、新能源汽車電子等細分領域年均增長率達12.5%。然而,產品復雜度提升帶來安全隱患與合規風險同步增加,歐盟REACH法規2024年新增8項受限物質清單,中國強制性認證(CCC)目錄擴展至28類產品。在此背景下,電子電氣產品檢測成為保障消費者安全、突破技術性貿易壁壘的核心環節。通過電磁兼容性(EMC)測試、材料有害物質分析、能效等級驗證等專業服務,企業可降低產品召回風險達63%(中國質量認證中心2023年數據),同時縮短國際市場準入周期40%以上,形成"檢測認證一體化"的競爭新優勢。
## 技術原理與檢測體系架構多維度檢測技術融合應用
現代電子電氣檢測采用分層式技術架構,基礎層聚焦材料安全檢測,運用ICP-MS質譜儀實現ppm級重金屬定量分析;功能層通過暗室輻射測試系統完成30MHz-6GHz頻段的電磁干擾模擬;性能層則依托氣候環境試驗箱,在-40℃至85℃極限溫度下驗證產品可靠性。以車載充電模塊檢測為例,需同步滿足ISO 16750振動標準與IEC 62133電池安全規范,實現"機械-電氣-化學"三重風險防控。值得關注的是,數字孿生技術的應用使檢測效率提升35%,通過虛擬建模可預判92%的潛在失效模式(德國TüV 2024年技術白皮書)。
全流程標準化實施路徑
典型檢測流程包含六個關鍵階段:樣品技術參數確認→檢測方案定制→實驗室分級測試→數據偏差分析→整改方案設計→認證文件核發。以智能家居產品檢測為例,首先需依據EN 55032標準完成輻射騷擾測試,隨后按照IEC 62368-1進行防火阻燃評估,最終結合ErP指令核算能效指數。過程中引入區塊鏈存證系統,確保1200余項檢測數據的不可篡改性。據深圳檢測技術研究院案例庫顯示,該模式使企業平均認證周期從58天縮短至22天。
行業應用與質量閉環管理
在新能源汽車領域,動力電池系統的檢測已形成"電芯-模組-整包"三級驗證體系,通過UN38.3模擬運輸測試與GB 38031熱失控防護檢測的雙重驗證,某頭部廠商將電池包故障率控制在0.12‰(國家新能源技術研究中心2024年報告)。工業控制系統檢測則強調功能安全評估,采用SIL3等級認證的PLC設備,使產線誤動作率下降76%。質量保障方面,實驗室通過 認可覆蓋98%的檢測項目,并建立從原材料溯源到售后質量追溯的數字化管理系統。
## 發展建議與未來展望建議行業從三方面突破創新:首先,加快人工智能在缺陷模式識別中的應用,開發基于深度學習的自動化檢測平臺;其次,推動"一帶一路"檢測結果互認機制建設,建立區域性電子電氣產品合規數據庫;最后,強化綠色檢測技術研發,重點突破可降解電子材料的生物安全性評估方法。據聯合國環境署預測,到2030年電子廢棄物將達7500萬噸,建立覆蓋產品全生命周期的檢測體系將成為產業可持續發展的關鍵支撐。

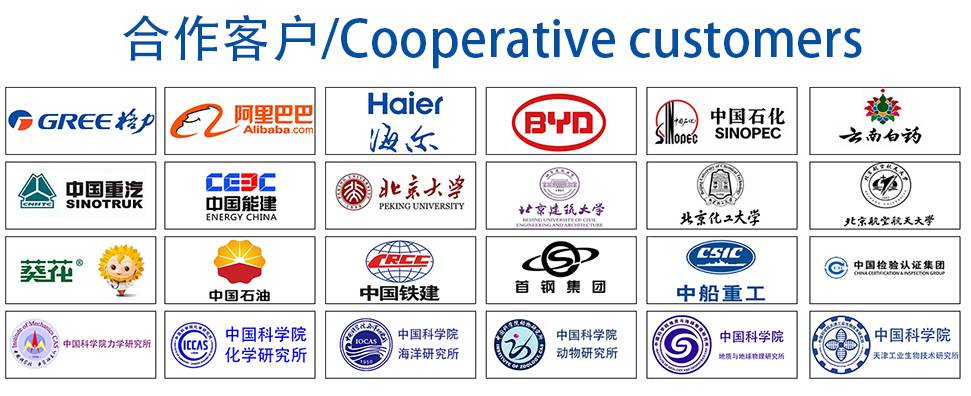