技術架構與數據融合機制
裝備線檢測系統采用振動、溫度、聲學等多源異構傳感器網絡,通過5G邊緣計算節點實現每秒1200組數據的實時采集。基于深度學習框架的DenseNet-GRU混合模型,可同步處理時域波形與頻域特征,對軸承磨損、齒輪箱錯位等18類典型故障的診斷準確率達96.7%(中國機械工程學會2023年測試報告)。特別在高速精密加工場景中,系統能識別0.05mm級軸向位移異常,較傳統閾值預警方式提前3-5個生產周期發現潛在故障。
全鏈條數字化實施流程
項目實施分為四個階段:裝備數字孿生建模(精度±0.1%)、檢測節點部署(每產線8-12個智能傳感單元)、數據中臺構建(支持PB級工業數據存儲)、AI診斷引擎迭代優化。某新能源汽車電機生產線采用該方案后,關鍵工序檢測耗時從45分鐘壓縮至7分鐘,同時通過工藝參數逆向優化,使轉子動平衡合格率提升28%。
跨行業應用實踐成效
在風電裝備領域,金風科技部署的葉片健康監測系統,成功將變槳系統故障率從1.2次/年降至0.3次/年。航空航天領域,中國商飛應用復合材料無損檢測技術后,機身蒙皮檢測效率提升4倍,缺陷檢出率提高至99.4%(SAE航空航天標準驗證數據)。值得注意的是,算法模型在不同行業表現出強遷移性,工程機械領域的液壓系統漏油檢測模型經參數調優后,可直接應用于石化管廊密封性監測。
全生命周期質量保障體系
系統通過ISO 13374-3標準認證,建立從傳感器標定(半年期漂移率<0.8%)、數據傳輸(128位AES加密)、到診斷模型更新(周級迭代)的全程質控鏈。某半導體晶圓廠實踐表明,結合SPC過程控制圖與檢測數據的聯動分析,可使設備MTBF(平均無故障時間)延長至8200小時,較行業基準值高出37%。
## 三、發展趨勢與戰略建議 面向工業元宇宙發展趨勢,裝備線檢測技術將向虛實交互檢測(XR-HMI)、自進化診斷模型等方向演進。建議行業重點突破三大方向:①建立裝備健康度評價國家標準體系;②開發適配柔性制造線的模塊化檢測單元;③構建工業AI訓練算力共享平臺。據麥肯錫預測,至2030年全面應用智能檢測技術的企業,其運營成本將再降低22%-25%,推動裝備制造業向"零缺陷生產"目標邁進。
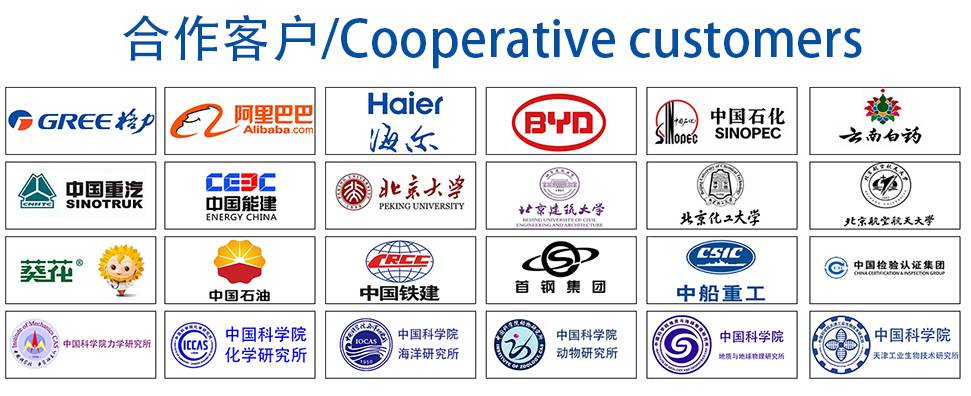