防噴器檢測的重要性與核心內容
防噴器(Blowout Preventer,BOP)是石油、天然氣鉆井作業中至關重要的安全設備,主要用于控制井口壓力、防止井噴及油氣泄漏事故。由于其工作環境復雜且風險極高,定期對防噴器進行系統性檢測是保障鉆井安全的核心環節。檢測不僅涉及設備本身的性能驗證,還包括對密封性、耐壓性、控制系統和應急功能的全面評估。根據國際標準(如API 16A)及行業規范,防噴器檢測需涵蓋多個關鍵項目,確保其能夠在高壓、高溫及腐蝕性環境下穩定運行。
防噴器檢測的核心項目
1. 外觀與結構完整性檢查
通過目視檢查、超聲波探傷或磁粉檢測等手段,排查防噴器殼體、閘板、密封面等部位的裂紋、腐蝕或變形。重點檢查法蘭連接處、焊縫和活動部件的磨損情況,確保無結構性缺陷影響承壓能力。
2. 密封性能測試
利用低壓(≤3.5MPa)和高壓(≥額定工作壓力)兩種模式,對防噴器的環形密封、閘板密封及連接部位的密封性進行測試。采用氮氣或清水作為介質,通過保壓試驗驗證泄漏率是否符合API 16A標準(泄漏量≤0.4L/min)。
3. 液壓系統與控制系統檢測
檢查液壓管線、儲能器、控制閥組的功能可靠性,模擬緊急關斷工況測試響應時間(通常要求≤45秒)。同時驗證遠程控制箱、聲光報警裝置的聯動性能,確保在斷電或故障時能觸發應急操作。
4. 壓力循環與疲勞測試
按照SY/T 5053.1標準進行額定壓力(如70MPa、105MPa)下的多次循環測試,評估防噴器在長期使用中的抗疲勞性能。超壓測試(1.5倍額定壓力)用于驗證設備的極限承壓能力。
5. 材料與防腐性能分析
對關鍵部件進行金相分析、硬度測試和化學成分檢測,確認材料符合ASTM A182標準。通過鹽霧試驗或涂層測厚儀評估防腐涂層的有效性,防止酸性氣體或鹽水環境導致的腐蝕失效。
6. 歷史數據與維護記錄核查
調取設備的維修記錄、更換零件清單及以往檢測報告,分析是否存在重復性故障或未修復隱患。同時核對防噴器的使用年限與設計壽命,為報廢或改造提供依據。
檢測周期與認證要求
根據API RP 53規范,常規檢測周期為21天(海上鉆井)或按月進行(陸上鉆井)。檢測完成后需出具第三方認證報告(如DNV或ABS),并粘貼檢驗合格標簽。未通過檢測的防噴器必須立即停用并返廠維修,確保鉆井作業零風險。

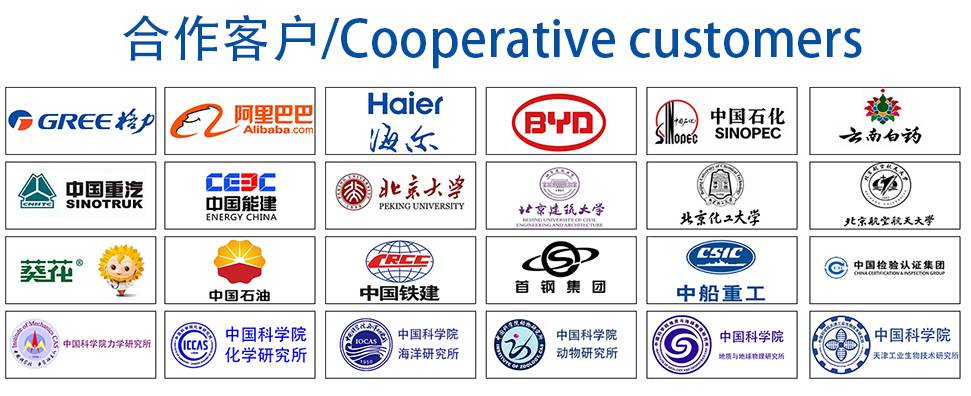