電動汽車動力蓄電池模塊檢測:保障安全與性能的核心環節
隨著電動汽車的快速普及,動力蓄電池作為車輛的核心部件,其安全性、可靠性和使用壽命直接關系到整車的性能和用戶體驗。動力蓄電池模塊檢測是生產、研發及售后環節中不可或缺的流程,旨在通過科學方法驗證電池的化學穩定性、能量密度、循環壽命及環境適應性等關鍵指標。隨著電池技術迭代加速(如三元鋰電池、磷酸鐵鋰電池的廣泛應用),檢測項目的精細化與標準化已成為行業關注焦點。國際標準(如GB/T 31484、ISO 6469)及企業內控規范共同構成了檢測體系的基礎,確保電池在全生命周期內滿足安全、環保和經濟效益需求。
檢測項目一:安全性能測試
安全性能測試是電池檢測的首要環節,涵蓋過充、過放、短路、擠壓、針刺等極端工況模擬。例如,通過過充實驗驗證電池管理系統的保護機制是否有效,防止熱失控風險;針刺測試則模擬電池內部短路時的耐受力,評估隔膜材料和電解液的穩定性。測試需在恒溫恒濕環境中進行,并記錄電壓、溫度變化及是否出現泄漏、起火等現象。
檢測項目二:容量與能量密度驗證
通過充放電循環測試(如1C/3C倍率充放電)測定電池的實際容量與標稱值的偏差,同時評估能量密度是否符合設計要求。測試需在不同溫度(-20℃至55℃)下進行,以模擬實際使用環境對電池性能的影響。容量衰減率(如1000次循環后容量保持率≥80%)是衡量電池壽命的重要指標。
檢測項目三:溫度適應性及熱管理測試
電池的溫控能力直接影響其效率和安全性。檢測包括高低溫充放電性能、熱沖擊試驗(如-40℃至85℃快速溫變)以及熱蔓延抑制能力測試。通過紅外熱成像儀監測模塊內部溫度分布,驗證散熱設計是否合理,確保電池在極端氣候下仍能穩定工作。
檢測項目四:機械強度與耐久性評估
模擬車輛行駛中的振動、沖擊和碰撞場景,采用機械振動臺進行隨機振動測試(頻率2-200Hz),檢測電池模塊的固定結構、連接件及外殼的可靠性。同時進行機械沖擊測試(如50g加速度沖擊),驗證電池在碰撞事故中的抗變形能力,防止內部短路風險。
檢測項目五:一致性測試與BMS功能驗證
針對電池模組內單體電芯的電壓、內阻、容量一致性進行嚴格篩選,避免“木桶效應”導致整體性能下降。此外,對電池管理系統(BMS)的均衡控制、故障診斷及通信協議進行檢測,確保其能實時監控電池狀態并執行保護策略,提升系統可靠性。
結語
動力蓄電池模塊檢測貫穿于設計、生產、裝車及回收全流程,是保障電動汽車安全性和市場競爭力的關鍵環節。隨著固態電池、鈉離子電池等新技術的發展,檢測標準與方法將持續升級,推動行業向更高安全等級和更優性能方向邁進。

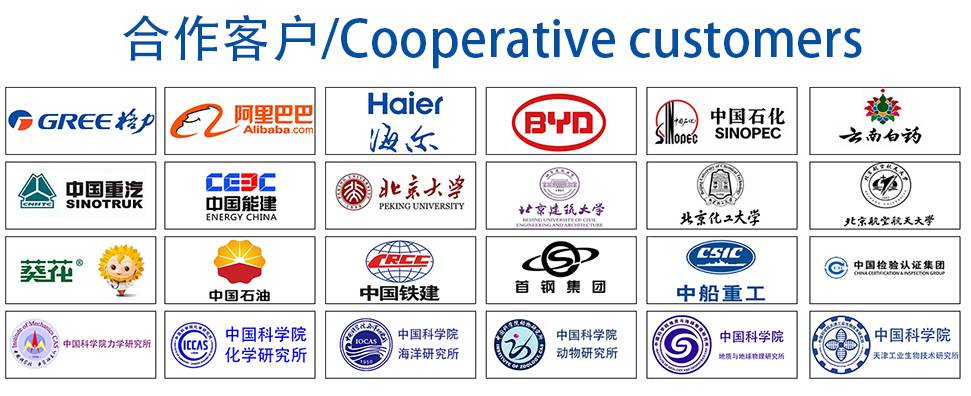