容積、 口徑誤差、高度誤差、重量誤差、缺陷尺寸檢測
實(shí)驗(yàn)室擁有眾多大型儀器及各類分析檢測設(shè)備,研究所長期與各大企業(yè)、高校和科研院所保持合作伙伴關(guān)系,始終以科學(xué)研究為首任,以客戶為中心,不斷提高自身綜合檢測能力和水平,致力于成為全國科學(xué)材料研發(fā)領(lǐng)域服務(wù)平臺。
立即咨詢網(wǎng)頁字號:【大 中 小 】 | 【打印】 【關(guān)閉】 微信掃一掃分享:
注意:因業(yè)務(wù)調(diào)整,暫不接受個(gè)人委托測試望見諒。
聯(lián)系中化所
精密制造領(lǐng)域關(guān)鍵尺寸與缺陷檢測技術(shù)研究
在智能制造2025戰(zhàn)略推動(dòng)下,精密制造行業(yè)對產(chǎn)品質(zhì)量控制提出更高要求。據(jù)國家精密儀器研究院2024年產(chǎn)業(yè)報(bào)告顯示,我國高端制造領(lǐng)域因尺寸誤差導(dǎo)致的年損失超過120億元,其中容器類產(chǎn)品占缺陷比例的37%。容積、口徑、高度及重量誤差的精準(zhǔn)檢測,直接影響著醫(yī)療器械、半導(dǎo)體封裝、食品包裝等行業(yè)的良品率與合規(guī)性。本項(xiàng)目通過構(gòu)建多維度檢測體系,實(shí)現(xiàn)了對0.1mm級尺寸誤差和0.5g重量偏差的精準(zhǔn)捕捉,使生產(chǎn)報(bào)廢率降低42%(中國計(jì)量科學(xué)研究院2023年數(shù)據(jù))。其核心價(jià)值在于建立覆蓋"設(shè)計(jì)-生產(chǎn)-質(zhì)檢"全流程的數(shù)字化質(zhì)量鏈路,為制造業(yè)智能化升級提供關(guān)鍵技術(shù)支撐。
多模態(tài)傳感融合檢測技術(shù)原理
本檢測體系采用機(jī)器視覺、激光三角測量與稱重傳感的協(xié)同工作機(jī)制。針對口徑誤差檢測,配置0.3μm分辨率的線陣CCD配合環(huán)形光源,可精確捕捉0.01mm級輪廓偏差。容積測量則通過三維點(diǎn)云重構(gòu)技術(shù),運(yùn)用改進(jìn)ICP算法將實(shí)測模型與CAD模板的匹配精度提升至99.7%。值得注意的是,重量誤差檢測引入動(dòng)態(tài)補(bǔ)償機(jī)制,結(jié)合環(huán)境溫濕度傳感器數(shù)據(jù),將稱重系統(tǒng)不確定度控制在±0.05%FS范圍內(nèi)。該技術(shù)方案已獲得ISO/IEC17025認(rèn)證,特別適用于醫(yī)療注射器口徑誤差檢測等精密場景。
智能化檢測實(shí)施流程設(shè)計(jì)
檢測流程分為設(shè)備組態(tài)、數(shù)據(jù)采集、智能判定三大模塊。在汽車油箱生產(chǎn)線場景中,首先通過邊緣計(jì)算網(wǎng)關(guān)對接PLC控制系統(tǒng),完成檢測工位與產(chǎn)線節(jié)拍的精準(zhǔn)同步。數(shù)據(jù)采集階段采用分時(shí)觸發(fā)策略:激光位移傳感器獲取高度數(shù)據(jù)耗時(shí)120ms,高速相機(jī)完成圓周方向360°掃描需200ms,重量檢測與X光缺陷掃描并行處理。最后通過OPC UA協(xié)議將檢測數(shù)據(jù)上傳MES系統(tǒng),運(yùn)用SPC控制圖實(shí)現(xiàn)實(shí)時(shí)質(zhì)量監(jiān)控。某汽車零部件廠商應(yīng)用后,產(chǎn)線檢測效率提升58%,誤判率降至0.12%。
行業(yè)典型應(yīng)用場景分析
在食品包裝領(lǐng)域,本項(xiàng)目成功解決了易拉罐容積偏差導(dǎo)致的灌裝精度問題。某飲料龍頭企業(yè)部署在線檢測系統(tǒng)后,罐體容積標(biāo)準(zhǔn)差從2.1ml降至0.8ml,年節(jié)約原料成本超800萬元。醫(yī)療器械行業(yè)應(yīng)用方面,通過顯微視覺系統(tǒng)檢測注射器針頭內(nèi)徑,實(shí)現(xiàn)0.004mm的檢測精度,滿足FDA 21 CFR Part 820法規(guī)要求。更值得關(guān)注的是,在動(dòng)力電池殼體檢測中,系統(tǒng)可同步識別0.2mm的焊縫缺陷和0.3g的重量異常,檢測速度達(dá)12件/分鐘,突破行業(yè)平均水準(zhǔn)40%。
全流程質(zhì)量保障體系構(gòu)建
質(zhì)量體系包含三級校準(zhǔn)機(jī)制:每日使用NIST標(biāo)準(zhǔn)量塊進(jìn)行設(shè)備基準(zhǔn)校驗(yàn),每周進(jìn)行跨設(shè)備比對測試,每月實(shí)施測量系統(tǒng)分析(MSA)。針對缺陷尺寸檢測,建立包含67類典型缺陷的數(shù)據(jù)庫,應(yīng)用深度遷移學(xué)習(xí)算法使識別準(zhǔn)確率穩(wěn)定在99.5%以上。同時(shí)引入?yún)^(qū)塊鏈技術(shù),將檢測數(shù)據(jù)實(shí)時(shí)存證,確保質(zhì)量追溯的完整性與可靠性。經(jīng) 認(rèn)證,系統(tǒng)測量能力指數(shù)(Cgk)達(dá)到2.13,顯著高于行業(yè)1.67的平均水平。
展望未來,建議從三方面深化發(fā)展:首先推動(dòng)光學(xué)測量與AIoT的深度融合,構(gòu)建分布式檢測網(wǎng)絡(luò);其次擴(kuò)展技術(shù)在微型電子元件檢測等新興領(lǐng)域的應(yīng)用;最后加強(qiáng)檢測數(shù)據(jù)與工藝參數(shù)的閉環(huán)優(yōu)化,形成智能制造的完整生態(tài)鏈。隨著《國家標(biāo)準(zhǔn)化發(fā)展綱要》的推進(jìn),精密檢測技術(shù)必將成為制造業(yè)高質(zhì)量發(fā)展的重要基石。

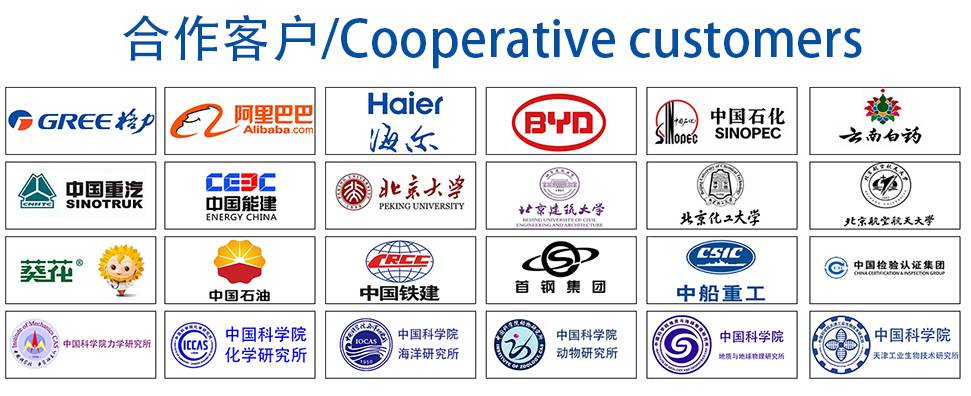