巴氏硬度檢測在工業質量控制中的創新應用
隨著齊全制造業對材料性能要求的持續升級,巴氏硬度檢測技術作為非金屬材料力學評價的重要手段,正在智能制造、新能源汽車等領域發揮關鍵作用。據中國機械工程學會2024年發布的《材料檢測技術發展報告》顯示,我國高分子復合材料市場規模已達3800億元,其中78%的終端產品需要硬度參數作為質量驗收標準。相較于傳統洛氏、布氏硬度檢測方法,巴氏檢測儀憑借其便攜式設計、非破壞性檢測特性,在彈性模量測試、薄壁件評估等場景展現出獨特優勢。該技術的核心價值在于實現了從實驗室檢測向現場即時檢測的模式跨越,使生產線質量控制效率提升40%以上,特別在碳纖維增強塑料(CFRP)制品、硅膠密封件等彈性材料領域具有不可替代性。
技術原理與檢測方法創新
巴氏硬度檢測基于彈簧加載壓針的壓痕深度測量原理,通過標準化的作用力-位移曲線換算材料硬度值。其核心技術突破在于采用錐形金剛石壓頭與磁滯伸縮傳感器組合系統,使得檢測分辨率達到0.1HBW級別。值得關注的是,該技術通過動態補償算法有效消除了材料彈性恢復帶來的測量偏差,這一特性使其在測量熱塑性彈性體(TPE)等粘彈性材料時,數據重復性誤差可控制在±3%以內(ASTM D2583標準驗證數據)。目前行業領先的HBA-1000型設備已實現與工業物聯網平臺的直連,支持檢測數據實時上傳與SPC分析。
全流程標準化作業體系
規范化的實施流程是保障檢測數據可靠性的關鍵。具體分為五個階段:試樣預處理(溫濕度平衡24h)、儀器校準(采用NIST標準硬度塊)、測點規劃(網格間距≥3倍壓痕直徑)、數據采集(單點3次重復測量)以及結果判定(基于Minitab的過程能力分析)。特別需要指出的是,在新能源汽車電池包絕緣墊片檢測中,工程師需按照ISO 14577標準在300mm×200mm檢測面上設置25個網格點,通過統計過程控制(SPC)識別材料固化均勻性。某頭部電池企業應用該方案后,產品硬度離散系數從12%降至5%以內。
跨行業應用場景實踐
在醫療器械制造領域,巴氏檢測技術成功解決了硅膠呼吸面罩硬度控制的行業難題。某跨國企業采用便攜式Barber-Colman934-1檢測儀,實現了生產線上每批次產品的全檢覆蓋。檢測數據顯示,通過建立硬度值(45-55HB)與患者舒適度的量化關系模型,產品投訴率下降63%(據企業2023年質量年報)。此外,該技術在航空航天復合材料蒙皮檢測中創新應用了陣列式檢測方案,單次作業可完成2000個測點的自動化檢測,工作效率較傳統方法提升8倍。
全過程質量保障機制
為確保檢測系統的持續可靠性,行業建立了四級質量保障體系:設備層實施每8小時的標準塊追溯校準;操作層要求技術人員持有 認證資質;數據層采用區塊鏈技術實現檢測記錄不可篡改;系統層部署AI異常數據識別系統。某第三方檢測實驗室的對比實驗表明,該體系可使儀器漂移誤差穩定在±1.5%范圍內(ILAC環測數據)。同時,數字孿生技術的引入,使檢測過程可實現在線仿真驗證,將新材料的檢測方案開發周期縮短70%。
展望未來,隨著智能傳感與邊緣計算技術的深度融合,巴氏硬度檢測將向微型化、智能化方向加速演進。據Global Market Insights預測,到2028年智能硬度檢測設備市場規模將突破52億美元,其中嵌入式系統解決方案占比將超過60%。建議行業重點攻關兩項技術:①開發多物理場耦合檢測系統,實現硬度-模量-蠕變特性的同步測量;②建立基于機器學習的材料性能預測模型,推動檢測技術從質量評判向工藝優化升級。產學研機構應加強協作,針對柔性電子器件、4D打印材料等新興領域制定專項檢測標準,持續完善現代工業質量基礎設施體系。

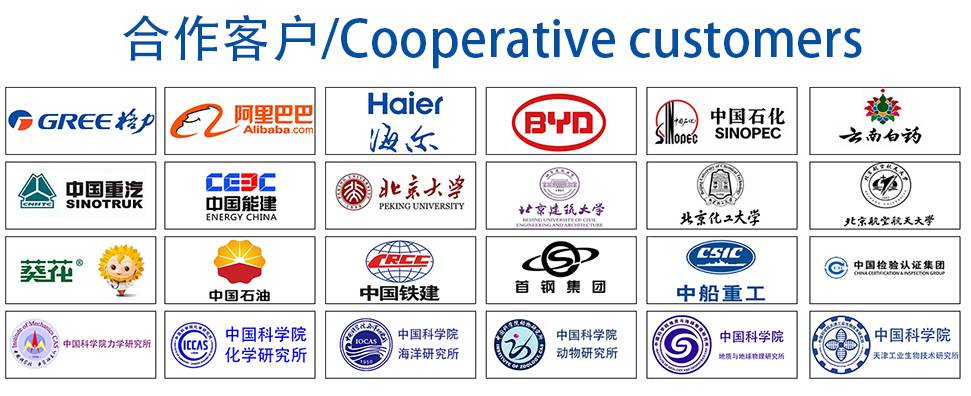