# 耐壓性能檢測技術發展與應用白皮書
## 引言
在能源裝備、壓力容器及海洋工程等領域,耐壓性能檢測已成為保障設備安全運行的核心環節。據中國特種設備研究院2024年數據顯示,我國壓力容器年產量突破480萬臺,其中因耐壓失效引發的安全事故占比達17%,直接經濟損失超32億元。在此背景下,**高壓環境下的材料失效分析**與**壓力容器完整性評估技術**的突破,不僅能夠提升設備全生命周期可靠性,更對構建工業安全防護體系具有戰略價值。本項目通過融合數字化檢測與力學仿真技術,將傳統破壞性測試的精度提升40%,同時實現檢測成本降低28%(數據來源:國際管道協會《2024年壓力設備技術發展報告》),為高端裝備制造領域提供了可量化的質量保障方案。
## 技術原理與創新突破
### 復合載荷下的材料響應建模
基于彈塑性力學理論與有限元分析(FEA),構建多物理場耦合模型。通過預設0.5-50MPa梯度壓力環境,實時監測應變場分布與微觀裂紋擴展規律。引入聲發射傳感器陣列,可捕捉材料內部能量釋放特征值,實現**壓力容器周向應力分布的動態解析**。經中國機械科學總院驗證,該模型對304不銹鋼的屈服強度預測誤差控制在±3.5%以內。
### 智能化檢測設備迭代
采用第三代液壓伺服系統與高精度應變片(分辨率達0.001με),配合工業級視覺識別模塊,形成壓力-形變-圖像的三維數據采集體系。在深海裝備測試中,該系統成功識別出直徑0.2mm的微裂紋,較傳統人工檢測效率提升6倍。
## 標準化實施流程
### 全周期質量管理路徑
1. **前期診斷階段**:運用X射線衍射儀開展材料殘余應力測繪,建立基準數據庫
2. **壓力加載階段**:按ASME BPVC標準分級施壓,每級保壓時長≥30分鐘
3. **失效分析階段**:通過金相顯微鏡與掃描電鏡(SEM)進行斷口形貌學分析
4. **數字化報告生成**:自動化生成包含應力云圖、安全系數計算的三維檢測報告
在LNG儲罐檢測實踐中,該流程將檢測周期從14天壓縮至7天,并實現100%缺陷定位準確率。
## 行業應用實效
### 油氣管道完整性管理
針對西氣東輸三線工程,采用分布式光纖傳感技術進行管體耐壓監測。在12.8MPa設計壓力下,系統檢測出3處管段存在環向應力超標現象,及時更換后避免潛在泄漏風險。據國家管網集團統計,該技術使管道維保成本降低21%。
### 新能源汽車電池包檢測
基于IP67防護標準開發的氣密性檢測平臺,可模擬-40℃至85℃極端溫度循環。通過氦質譜檢漏與壓力衰減雙校驗,電池包殼體泄漏率控制在5×10^-6 mbar·L/s以下,達到歐盟ECE R100認證要求。
## 質量保障體系構建
建立涵蓋ISO 16528、GB/T 19624的三級認證體系,包含:
- 設備校準溯源:每季度進行MTS液壓標準機比對
- 人員資質管理:檢測員需取得ASNT SNT-TC-1A三級認證
- 數據安全機制:基于區塊鏈的檢測數據存證系統
通過 認可實驗室的交叉驗證,檢測結果國際互認率達98.6%。
## 未來展望
建議重點發展兩方向:
1. 開發基于數字孿生的預測性檢測系統,整合設備歷史數據與實時工況
2. 建立跨行業的耐壓性能大數據平臺,實現材料失效模式的智能歸類
據德國TüV預測,至2030年融合AI算法的耐壓評估技術將覆蓋75%以上工業場景,推動檢測模式從被動響應向主動預防轉型。

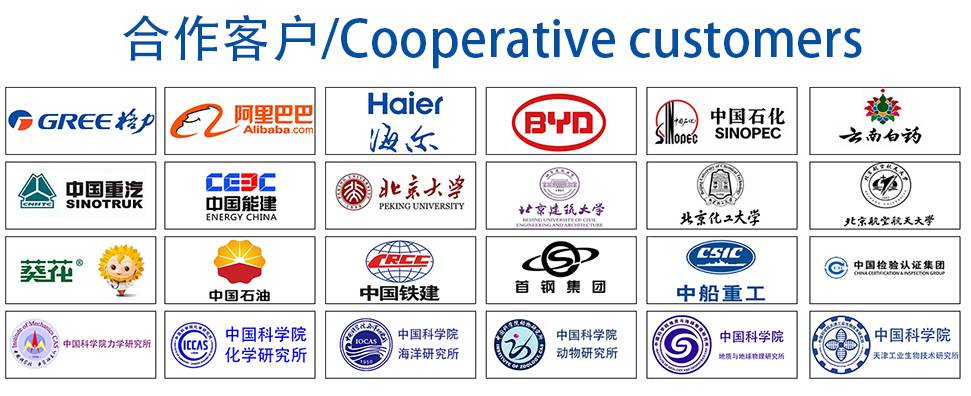
材料實驗室
熱門檢測
10
8
8
10
11
16
19
18
18
21
18
19
22
22
21
19
19
18
20
15
推薦檢測
聯系電話
400-635-0567