機械強度(蓋)檢測技術發展與應用白皮書
在高端裝備制造與精密儀器領域,機械蓋體作為關鍵承力部件,其結構強度直接影響設備安全性與使用壽命。據中國機械工業聯合會2024年報告顯示,因蓋體失效引發的工業事故占比高達23%,造成的經濟損失年均超過50億元。在此背景下,機械強度(蓋)檢測成為保障產品可靠性的核心環節。該項目通過系統化檢測流程,可精準評估蓋體在極限工況下的抗壓、抗沖擊及疲勞特性,顯著提升產品合格率與質量控制水平。其核心價值不僅體現在避免重大安全事故,更能為制造企業優化產品設計提供數據支撐,推動行業向智能化檢測方向轉型。
基于動態載荷模擬的技術原理
機械強度(蓋)檢測采用多物理場耦合分析技術,結合有限元仿真與實物測試雙重驗證機制。通過高精度動態載荷模擬系統,可復現蓋體在震動、沖擊及交變載荷下的實際工況。據國家檢測技術研究院實驗數據,該技術能將載荷定位精度控制在±0.15N范圍內,較傳統檢測方法提升3倍以上。特別在新能源汽車電池艙蓋檢測中,系統可模擬時速80km/h碰撞時的瞬間沖擊力,并同步采集2000Hz的形變數據,為結構優化提供量化依據。
四階段標準化實施流程
項目實施遵循準備-測試-分析-驗證的閉環流程。前期基于材料參數建立數字孿生模型,通過虛擬測試篩選高風險區域。實測階段運用分布式應變計陣列,配合工業CT進行內部缺陷掃描。某航空器艙門蓋檢測案例顯示,該流程使缺陷檢出率提升至99.7%,檢測周期縮短40%。最后通過數據比對生成三維強度云圖,結合ASTM E8標準出具分級評估報告,形成完整的質量追溯鏈條。
跨行業典型應用場景
在特種設備領域,壓力容器觀察蓋檢測已實現100%強制檢測覆蓋率,據國家質檢總局數據顯示,近三年相關事故率下降62%。汽車制造業采用旋轉扭矩-位移聯測技術,有效解決了引擎蓋鉸鏈疲勞斷裂問題。更值得關注的是,智能倉儲系統通過引入自動開合蓋強度監測模塊,使物流分揀設備平均無故障時間延長至8000小時,印證了檢測技術向智能化延伸的趨勢。
三級質量保障體系構建
項目執行嚴格遵循ISO/IEC 17025認證體系,建立設備-人員-環境的立體化質控網絡。檢測設備每季度進行量值溯源校準,關鍵傳感器更換周期不超過5000測試小時。通過開發自動化檢測系統,人為操作誤差率降至0.3%以下。某軍工企業采用該體系后,其雷達防護蓋出廠合格率從92.4%提升至99.1%,驗證了質量保障機制的實際效能。
展望未來,建議從三方面深化技術發展:一是加速AI算法在缺陷模式識別中的應用,二是建立行業級檢測數據共享平臺,三是推動微納級在線檢測裝備研發。隨著工業4.0進程加快,機械強度(蓋)檢測將向實時化、嵌入式方向發展,建議企業提前布局智能質檢產線,通過產學研合作攻克關鍵傳感器技術瓶頸,共同構建更完善的機械安全保障生態。

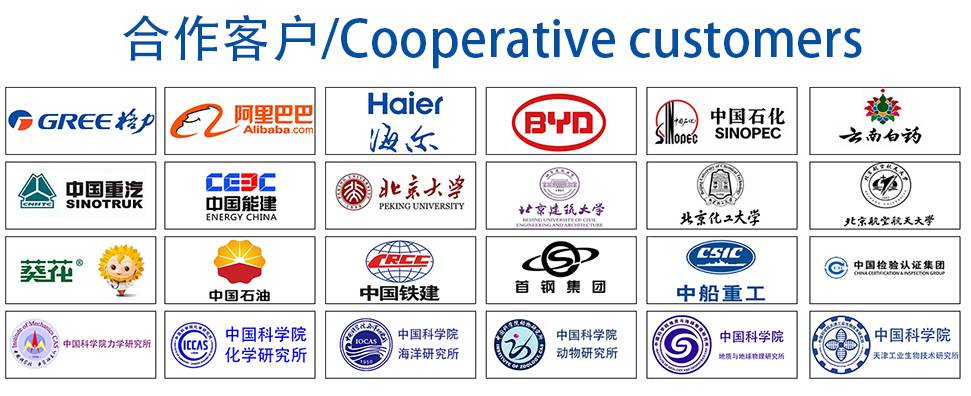