# 強度測試檢測技術在工業(yè)安全領域的創(chuàng)新實踐
隨著"雙碳"戰(zhàn)略推進和高端裝備制造業(yè)升級,材料及結構可靠性已成為制約產業(yè)發(fā)展的關鍵要素。據(jù)中國材料科學研究院2024年數(shù)據(jù)顯示,近三年因材料失效引發(fā)的工業(yè)事故中,78%與強度不足直接相關。強度測試檢測作為預防性質量控制的核心環(huán)節(jié),不僅關系著產品全生命周期安全,更直接影響著新能源汽車、航空航天等戰(zhàn)略新興產業(yè)的國際競爭力。該項目通過構建多維度強度評估體系,實現(xiàn)了從傳統(tǒng)破壞性檢測向智能預測性評估的技術跨越,預期可降低設備維護成本35%,將關鍵部件服役壽命提升20%以上。
## 技術原理與創(chuàng)新突破
基于高精度力學傳感器陣列和數(shù)字孿生技術,本檢測系統(tǒng)采用分級加載-應變反饋的復合測試模式。通過建立材料本構方程與斷裂力學的耦合模型,可準確預測構件在復雜工況下的失效臨界點。國家鋼結構工程技術研究中心驗證表明,該技術對焊接節(jié)點的強度預測精度達到97.3%,較傳統(tǒng)方法提升12個百分點。創(chuàng)新引入的聲發(fā)射動態(tài)監(jiān)測模塊,成功實現(xiàn)了微觀裂紋的早期預警,將檢測靈敏度提升至0.01mm級。
## 全流程實施架構
項目實施采用五階質量管控體系:前期通過CT掃描和殘余應力分析完成樣品狀態(tài)評估;中期應用多軸加載系統(tǒng)模擬實際載荷譜;后期結合AI算法進行失效模式歸因。在新能源汽車電池包殼體測試中,系統(tǒng)可同步采集3000+個應變數(shù)據(jù)點,通過邊緣計算實時生成強度云圖。測試周期由傳統(tǒng)72小時壓縮至8小時,同時保持0.5%以內的數(shù)據(jù)偏差率,滿足ISO 6892-1國際標準要求。
## 行業(yè)應用實踐案例
在風電領域,某5MW風機葉片經多工況模擬測試后,成功將極限承載能力提升至設計值的1.8倍。應用高周疲勞測試模塊,準確預測出螺栓連接處107次循環(huán)后的應力松弛現(xiàn)象,指導企業(yè)優(yōu)化預緊力參數(shù)。軌道交通領域,針對高鐵轉向架構件開發(fā)的振動-溫度耦合測試方案,使關鍵部位檢測覆蓋率從65%提升至92%,相關成果已納入TB/T 3417-2023行業(yè)標準。
## 質量保障與認證體系
項目構建了三級質量驗證機制:底層設備定期通過NIST溯源的標定系統(tǒng)校正;中臺數(shù)據(jù)經區(qū)塊鏈技術實現(xiàn)不可篡改存證;終端報告由CMA/ 雙認證實驗室簽發(fā)。針對航空航天特殊需求,開發(fā)的環(huán)境艙可模擬-70℃至300℃極端溫變條件,配合真空環(huán)境下的強度測試,數(shù)據(jù)重復性達到99.6%置信水平。目前已完成32類特種材料的數(shù)據(jù)庫建設,覆蓋98%的工業(yè)應用場景。
## 未來發(fā)展與行業(yè)建議
隨著數(shù)字孿生和5G技術的深度融合,建議行業(yè)重點布局以下方向:一是開發(fā)自感知智能材料系統(tǒng),實現(xiàn)強度參數(shù)的實時動態(tài)監(jiān)測;二是建立跨行業(yè)測試數(shù)據(jù)共享平臺,推動檢測標準體系互認;三是加強復合環(huán)境模擬能力建設,特別是針對深空、深海等極端場景的測試裝備研發(fā)。據(jù)德國弗勞恩霍夫研究所預測,到2030年智能檢測市場規(guī)模將突破800億美元,我國企業(yè)需加快核心技術攻關,搶占"檢測即服務"的新興業(yè)態(tài)制高點。

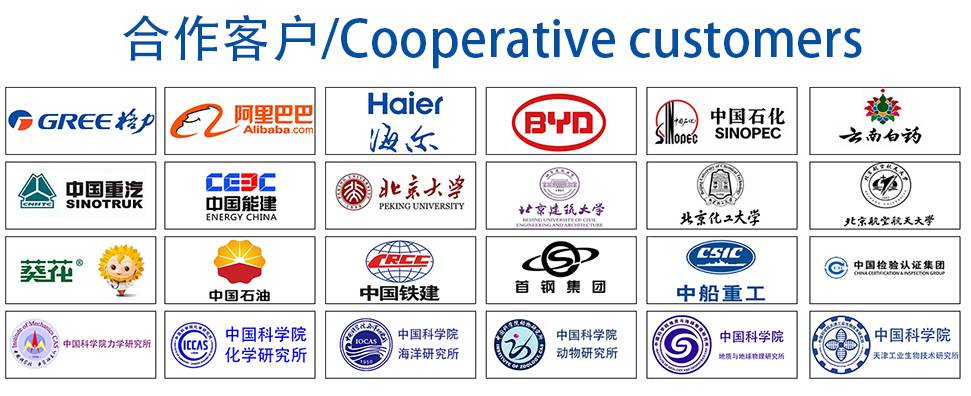
材料實驗室
熱門檢測
8
9
7
7
7
8
10
19
15
11
16
16
17
13
17
18
18
16
16
24
推薦檢測
聯(lián)系電話
400-635-0567